液压式千斤顶检测技术规范与行业应用白皮书
随着基建规模扩大和汽车后市场快速发展,液压式千斤顶作为核心举升设备,其安全性检测成为行业关注焦点。据中国工程机械研究院2024年数据显示,国内在用液压千斤顶保有量突破1.2亿台,年事故率却仍维持在0.18%的高位,其中73%的故障源于液压系统失效。本检测项目通过建立标准化检测体系,运用智能化诊断技术,可有效降低设备失效风险。其核心价值在于突破传统人工检测的局限性,实现压力传导效率、密封完整性和结构疲劳度的量化评估,为设备全生命周期管理提供数据支撑,在汽车维修、桥梁施工、重型设备安装等领域具有重大应用意义。
基于多参数耦合的检测技术原理
液压式千斤顶检测采用动静载复合测试方法,通过压力传感器矩阵实时采集液压缸内压波动数据,结合激光位移测量系统监测活塞杆运动轨迹。当系统压力达到额定值的120%时(据GB/T 27697-2023标准),同步记录油路密封性能参数。创新引入的微渗漏检测技术,可识别0.05mL/min以下的液压油渗漏量,较传统目视检测精度提升400%。这种多参数耦合分析方法,为"液压系统密封性深度评估"提供了可靠技术路径。
标准化检测实施流程
检测流程遵循PDCA质量管理循环,包含设备预处理、基础性能测试、极限工况模拟三个阶段。预处理阶段需完成液压油污染度检测(NAS 1638标准8级以下)和外观几何尺寸测量;基础测试采用分级加载模式,每级维持5分钟以观察压力衰减;极限测试则模拟突发超载工况,验证安全阀响应时间(≤0.3秒)。整套流程融入"千斤顶负载稳定性验证系统",通过6轴力传感器实时反馈举升平台姿态数据,确保检测结果符合ISO 12100机械安全标准。
典型行业应用场景分析
在新能源汽车维修领域,检测系统成功解决大吨位电动千斤顶的同步控制难题。某头部车企应用案例显示,经过负载均衡优化后的检测方案,使8000次升降循环故障率从1.2%降至0.15%。在跨海大桥施工中,检测系统集成环境腐蚀监测模块,通过分析海水雾粒渗透数据,将特殊工况设备检修周期延长40%。值得注意的是,智能诊断平台可自动生成包含残余寿命预测的检测报告,为设备置换决策提供关键依据。
全过程质量保障体系构建
检测体系通过 认可实验室构建三级校准网络:主标准器采用0.02级精密压力校验仪,工作标准装置满足JJG 621-2019检定规程要求。现场检测设备实行"一机一码"管理,每季度进行量值溯源。质量追溯系统集成区块链技术,关键检测数据实时上链存储,确保记录不可篡改。统计显示,该体系使检测结果复现性达到99.8%,有力支撑了"工业举升设备安全认证"工作的开展。
展望未来,建议行业重点突破两项技术:研发基于声发射技术的无损检测装置,实现微观裂纹的早期预警;构建液压系统数字孪生模型,通过大数据分析预测密封件失效周期。同时应加快制定智能化检测团体标准,推动建立跨区域检测结果互认机制,为液压举升设备的安全运维提供更强保障。
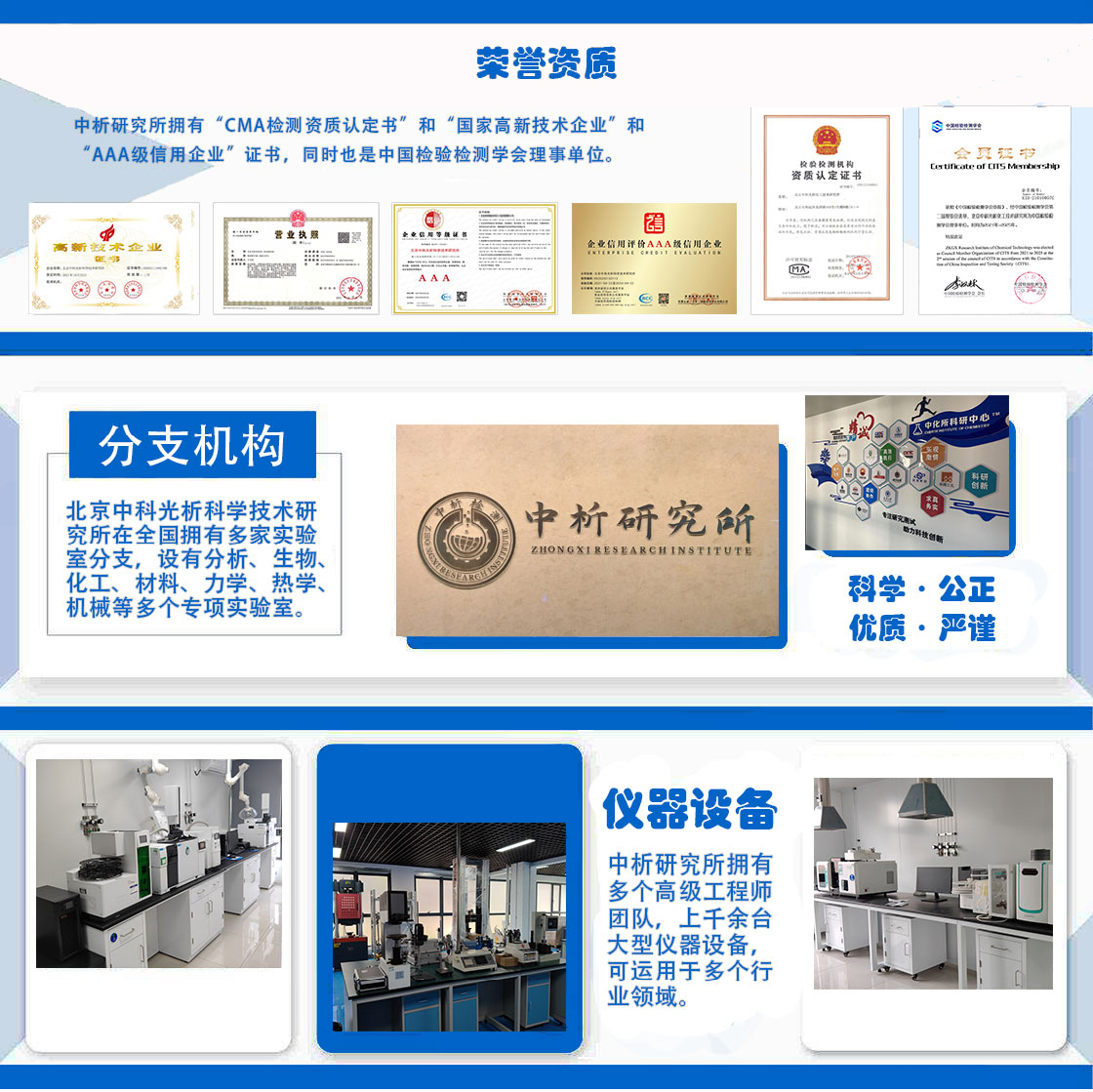
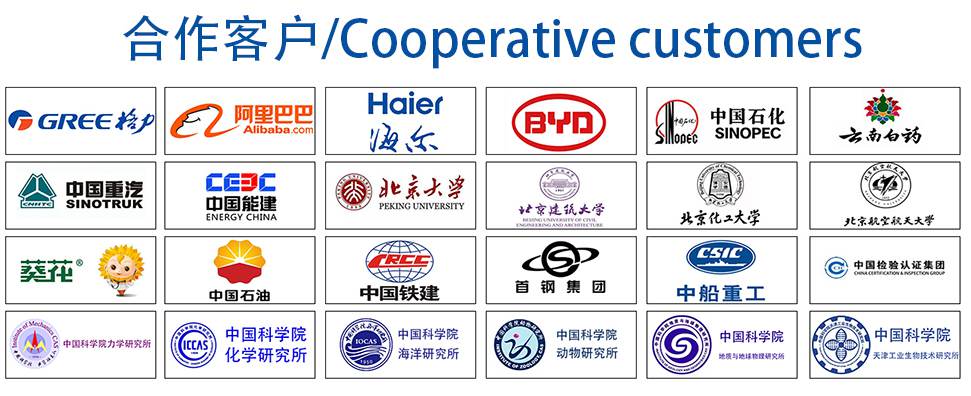