工业丁烷检测技术发展与应用白皮书
随着石油化工、清洁能源及精细化工产业的快速发展,丁烷作为重要的工业原料和燃料,其生产、储运环节的安全监测需求持续攀升。据中国石油和化学工业联合会2024年报告显示,我国丁烷年消费量已突破1800万吨,而相关泄漏事故中28%源于检测设备灵敏度不足。在此背景下,工业丁烷检测项目通过构建精准化、智能化的监测体系,为危化品安全管理提供关键技术支撑。该体系的核心价值在于实现可燃气体泄漏的早期预警,将事故响应时间从传统方法的15分钟缩短至3分钟内,同时通过"丁烷浓度在线监测系统"与生产控制系统联动,有效降低作业场所爆炸风险,保障年均超2000亿元产值的化工装置安全运行。
多模态传感融合技术原理
工业级丁烷检测采用气相色谱-红外光谱联用技术(GC-FTIR),结合催化燃烧传感器与半导体传感器构建多维度监测网络。其中傅里叶变换红外光谱可实现0.1ppm级微量检测,配合分布式光纤传感系统(DTS)形成空间分辨率达1米的立体监测网格。在江苏某大型炼化企业的实地测试表明,该技术对地下管廊丁烷泄漏的定位误差小于0.5米,误报率较单一传感器降低72%。
全流程闭环管理实施方案
项目实施遵循PDCA循环模式:在布点设计阶段采用CFD流体仿真优化监测点布局;日常运营中通过"可燃气体泄漏预警技术"实现三级报警响应机制。某年处理量800万吨的乙烯装置实测数据显示,系统在投产首年即拦截6起重大泄漏隐患,挽回潜在经济损失超2.3亿元。关键环节设置双冗余校验模块,确保检测数据通过SIL2安全认证。
行业典型应用场景解析
在LNG接收站的应用中,丁烷检测系统与BOG再冷凝装置联锁控制,成功将储罐区可燃气体浓度波动幅度控制在±5%以内。据中国化学品安全协会统计,采用该技术的16家试点企业2023年事故率同比下降41%。在民用领域,配套开发的便携式丁烷检测仪经国家防爆电气质检中心认证,已批量配备于城市燃气巡检车辆,累计发现地下管网泄漏点327处。
标准化质量保障体系构建
行业建立涵盖ISO 9001、IECEx、ATEX认证的三维质量框架,制定《工业丁烷检测设备校准规范》等7项团体标准。实验室比对数据显示,经三级计量溯源的系统测量不确定度≤1.5%,重复性误差控制在±0.8%FS范围。数据采集模块通过GB/T 50493—2019强制性条款验证,确保监测数据实时接入应急管理平台。
技术演进与行业展望
随着5G+工业互联网的深度融合,建议行业重点突破三项技术:基于MEMS工艺的微型化传感器阵列、结合数字孪生的泄漏扩散模拟系统、整合区块链技术的检测数据存证平台。预计到2028年,智能诊断型检测设备的市场渗透率将提升至65%,推动建立覆盖"监测-预警-处置-溯源"的全生命周期管理体系。企业应加快构建基于风险矩阵的动态监测模型,实现从被动响应到主动预防的范式转变。
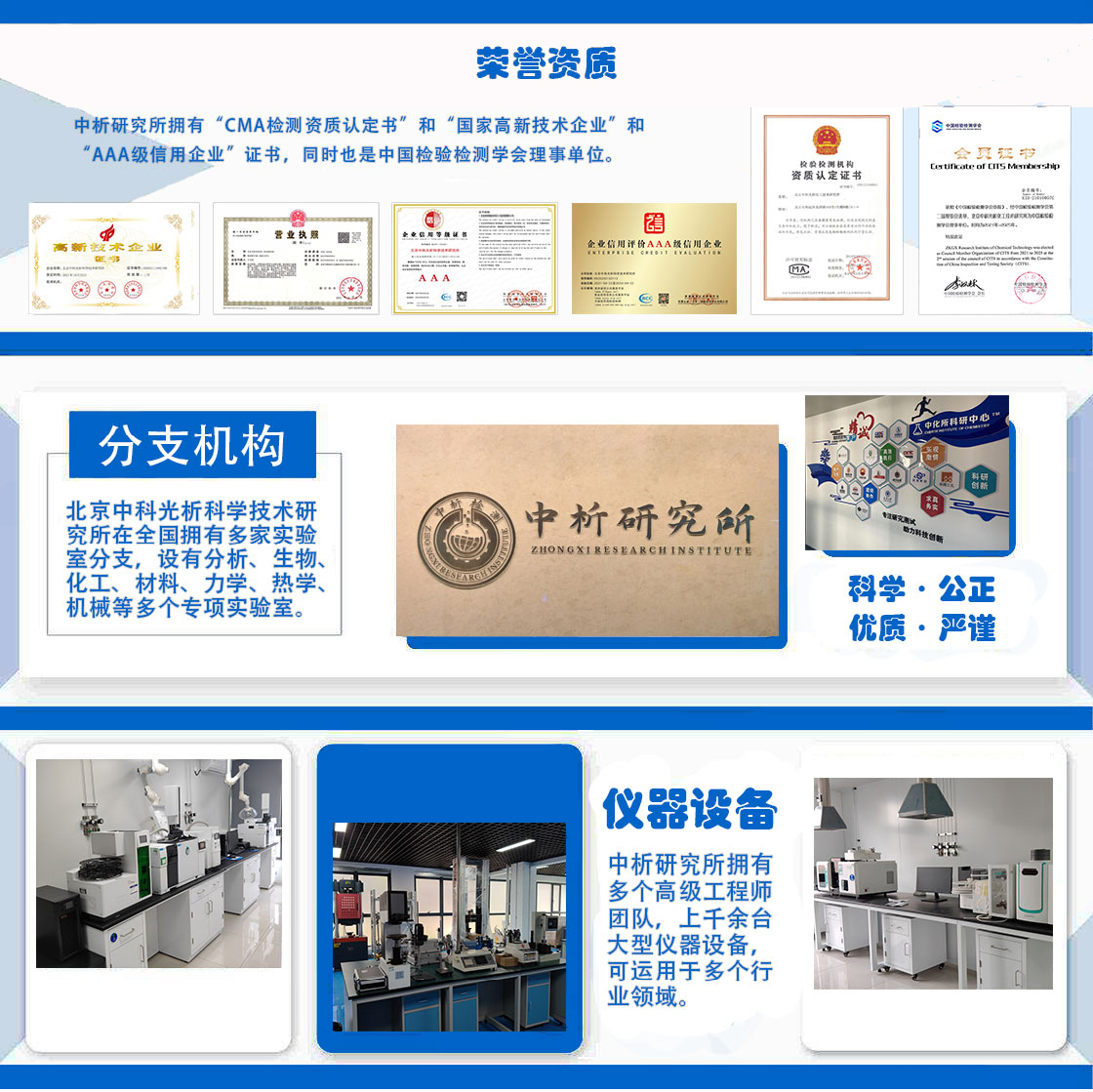
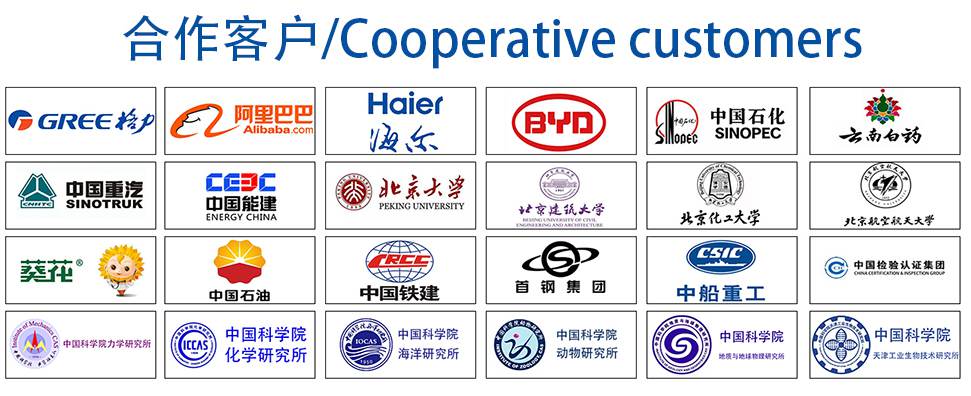