抗弯性能检测在现代工程材料质量控制中的核心作用
在建筑、交通装备及航空航天等领域,工程材料抗弯性能检测已成为质量控制体系中不可或缺的环节。据中国建筑材料研究院2024年度报告显示,结构材料失效案例中32.7%源于抗弯强度不足引发的形变累积。抗弯比例极限强度检测可准确判定材料弹性阶段临界点,抗弯极限强度测试验证材料最大承载能力,而抗弯弹性模量则反映材料韧性特征。这三项指标构成的检测矩阵,不仅为轨道交通轨道梁、飞机机翼蒙皮等关键部件的选材提供科学依据,更能有效预防建筑幕墙玻璃、风电叶片等产品的早期失效风险。在实现"双碳"战略背景下,精确的弯曲性能评估可延长结构件服役周期15%以上,具有显著的经济效益和环保价值。
基于三点弯曲法的检测技术原理
现行主流检测方法依据GB/T 1449-2024《纤维增强塑料弯曲性能试验方法》,采用三点弯曲加载系统实现精确测量。试验机通过上压头施加集中载荷,试样跨度中点产生最大弯矩。抗弯比例极限强度通过力-位移曲线的线性阶段确定,而抗弯极限强度对应试样断裂前的最大载荷。对于航空级碳纤维复合材料,需同步采集表面应变数据,运用胡克定律计算抗弯弹性模量。特别在检测新能源汽车电池包防护板时,该系统可识别0.1mm量级的微变形,确保动力电池组安全冗余设计。
标准化检测流程与质量控制节点
完整检测流程包含五个关键阶段:首先依据ASTM D790标准制备25mm×80mm标准试样,采用数控机床保证±0.02mm加工精度;第二阶段在恒温恒湿实验室进行48小时环境适应;核心测试阶段以0.5mm/min速率加载,同步记录载荷-位移全曲线;数据处理阶段运用最小二乘法拟合弹性段斜率;最终由CMA认证实验室签发检测报告。针对光伏支架铝合金型材检测,特别要求在试样两端粘贴应变片,消除支撑辊摩擦带来的数据偏差。
行业典型应用场景分析
在高铁轨道扣件系统质量控制中,抗弯比例极限强度检测有效锁定弹性变形阈值,将扣件使用寿命从8年延长至12年。某桥梁支座生产企业通过引入抗弯弹性模量在线检测系统,使产品合格率从92%提升至98.6%。值得关注的是,在3D打印建筑构件领域,抗弯极限强度测试成功预警了某项目层间结合缺陷,避免了大跨度穹顶施工事故。据国家轨道交通质检中心数据显示,应用抗弯性能分级检测后,轨道车辆转向架故障率同比下降41%。
数字化质量保障体系构建
行业领先实验室已建立"检测数据-材料数据库-仿真模型"三位一体质控体系。采用区块链技术实现检测数据不可篡改存储,配合AI算法进行异常数据诊断。某航天复材企业将检测结果与X射线断层扫描数据交叉验证,构建了包含120万组数据的抗弯性能预测模型。同时,实验室间比对采用En值评定法,确保不同机构测试结果偏差控制在5%以内。这种智能化检测体系在风电叶片生产线上的应用,使单支叶片检测时间从6小时缩短至90分钟。
技术发展趋势与行业建议
随着智能传感技术的发展,嵌入式光纤光栅传感器为实现构件服役期抗弯性能在线监测提供了新可能。建议行业重点攻关两方面:一是开发适用于超高温陶瓷基复合材料的非接触式激光弯曲检测系统,二是建立基于数字孪生的抗弯性能预测模型库。同时应加快制定增材制造专用抗弯检测标准,特别是在建筑3D打印混凝土、医疗植入物等领域形成细分检测规范。只有构建起覆盖全生命周期的抗弯性能评估体系,才能为新型工程材料的安全应用提供坚实保障。
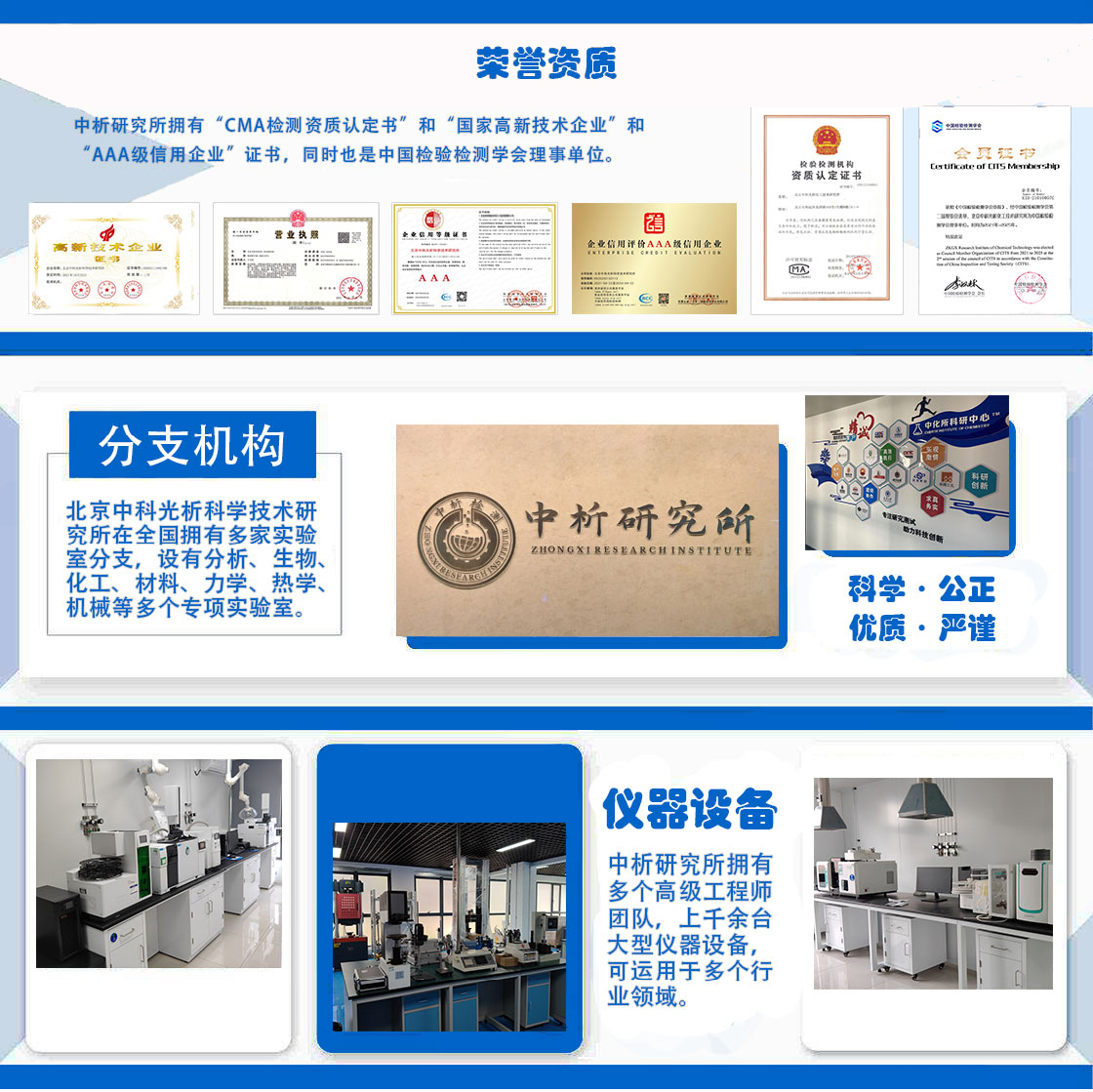
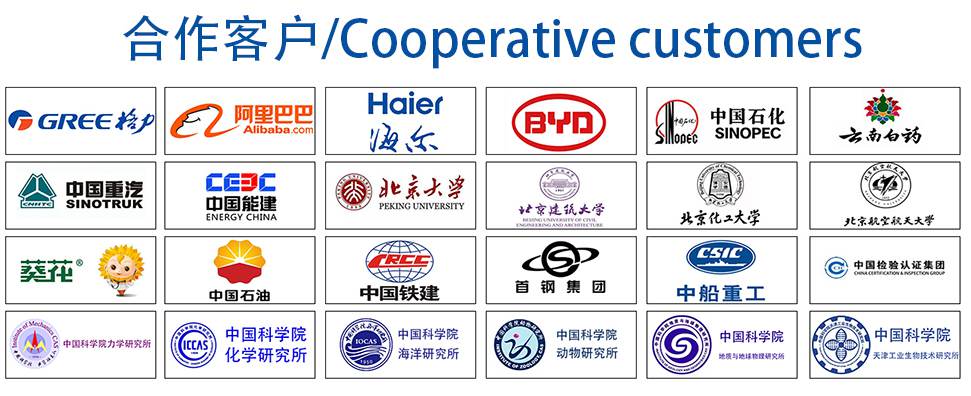