# 耐盐水性检测技术发展与应用白皮书
## 引言
在海洋经济快速发展的背景下,海洋工程装备、船舶制造及沿海基础设施面临严峻的盐雾腐蚀挑战。据中国海洋工程研究院2024年统计数据显示,我国每年因海水腐蚀造成的直接经济损失超过3000亿元,其中材料耐盐水性不足导致的设备失效占比达42%。耐盐水性检测作为材料性能评价的核心环节,通过模拟海洋盐雾环境加速老化效应,可为材料选型、防腐工艺优化提供科学依据。其核心价值在于突破传统经验式设计局限,建立定量化的耐蚀性能分级体系,有效延长装备服役周期30%以上,在高端装备制造领域具有显著的降本增效作用。
## 技术原理与标准化体系
### 盐雾腐蚀作用机制
材料在盐雾环境中的失效源于电化学腐蚀与物理侵蚀的协同作用。当NaCl溶液形成电解质薄膜时,Cl⁻离子穿透金属表面钝化膜引发点蚀,同时盐晶体积聚产生的机械应力加速涂层剥离。ASTM B117标准规定的中性盐雾试验(NSS)通过5% NaCl溶液连续喷雾,可模拟典型海洋大气环境,验证材料在"海洋工程装备耐腐蚀认证"场景下的耐久性。

### 分级检测方法体系
现行检测矩阵包含三种递进式方案:基础级72小时盐雾试验评价表面腐蚀面积,进阶级配合干湿循环测试验证涂层附着力,专业级则引入电化学阻抗谱(EIS)量化电荷转移电阻值。根据ISO 9227标准,耐盐水性等级按腐蚀速率分为C1-C5五个级别,其中C4级(年腐蚀量<1.3μm)已成为海上风电塔筒材料的准入基准。
## 全流程检测实施方案
### 标准化作业流程
项目实施采用"预处理-加速老化-量化分析"三级架构:首先依据GB/T 10125进行试样表面清洁与划痕制备,随后在温湿度双控试验箱中完成480小时连续喷雾,最终通过三维形貌仪测量最大蚀坑深度,并配合能谱分析(EDS)确定腐蚀产物的元素构成。某船用钢板检测数据显示,经工艺改良后试样的腐蚀电流密度由1.25μA/cm²降至0.38μA/cm²,钝化效果提升67%。
### 智能化检测系统
新一代检测平台集成物联网传感器与机器学习算法,通过实时采集箱内pH值、电导率等12项参数,动态调节喷雾量实现精准环境模拟。青岛海工装备检测中心的实践表明,该系统将盐雾浓度控制精度从±15%提升至±5%,同时检测周期缩短20%。
## 行业应用场景解析
### 海上风电领域
针对风机塔架基座"盐雾环境下材料失效分析"难题,金风科技采用梯度检测方案:基础结构件执行2000小时扩展盐雾测试,传动系统组件增加30次热冲击循环。检测数据显示,经表面纳米化处理的法兰部件,在模拟南海环境下的腐蚀速率降低至0.12mm/年,较传统工艺提升3倍耐蚀性。
### 汽车零部件验证
新能源汽车电池托盘需通过GM9540P标准验证,该检测在85℃高温下进行240小时酸性盐雾(pH3.5)冲击。宁德时代检测报告显示,采用微弧氧化处理的铝合金壳体,经检测后表面仅出现Ⅱ级轻微腐蚀(GB/T 6461),成功满足北美市场准入要求。
## 质量保障与技术创新
### 三重校验机制
实验室资质认定(CMA)体系要求设备每日进行喷雾沉降量校准,每周开展参比试样对比试验,每季实施测量系统分析(MSA)。国家材料腐蚀科学数据中心2023年能力验证数据显示,头部机构盐雾试验箱的温度均匀性达±1.5℃,优于国标±2℃的技术要求。
### 交叉验证技术
为克服单一检测方法的局限性,行业领先机构已建立EIS(电化学阻抗谱)-SKP(扫描开尔文探针)-XCT(X射线断层扫描)多模态分析体系。上海材料研究所的对比试验证实,该方案可使腐蚀深度测量误差从12%压缩至3%以内。
## 发展趋势与建议
随着深海装备、氢能源储运等新兴领域发展,耐盐水性检测需向高压、多因子耦合方向延伸。建议行业重点突破两项技术:开发可模拟3000米水深压力的复合腐蚀试验舱,建立Cl⁻/H2S/SO₂多介质协同作用模型。同时推动检测标准与ASME、DNVGL等国际体系接轨,构建覆盖材料研发-工艺验证-服役监测的全生命周期评价体系,为"双碳"目标下的海洋经济发展提供技术支撑。
上一篇:低温柔度检测下一篇:质量损失和炭化体积检测
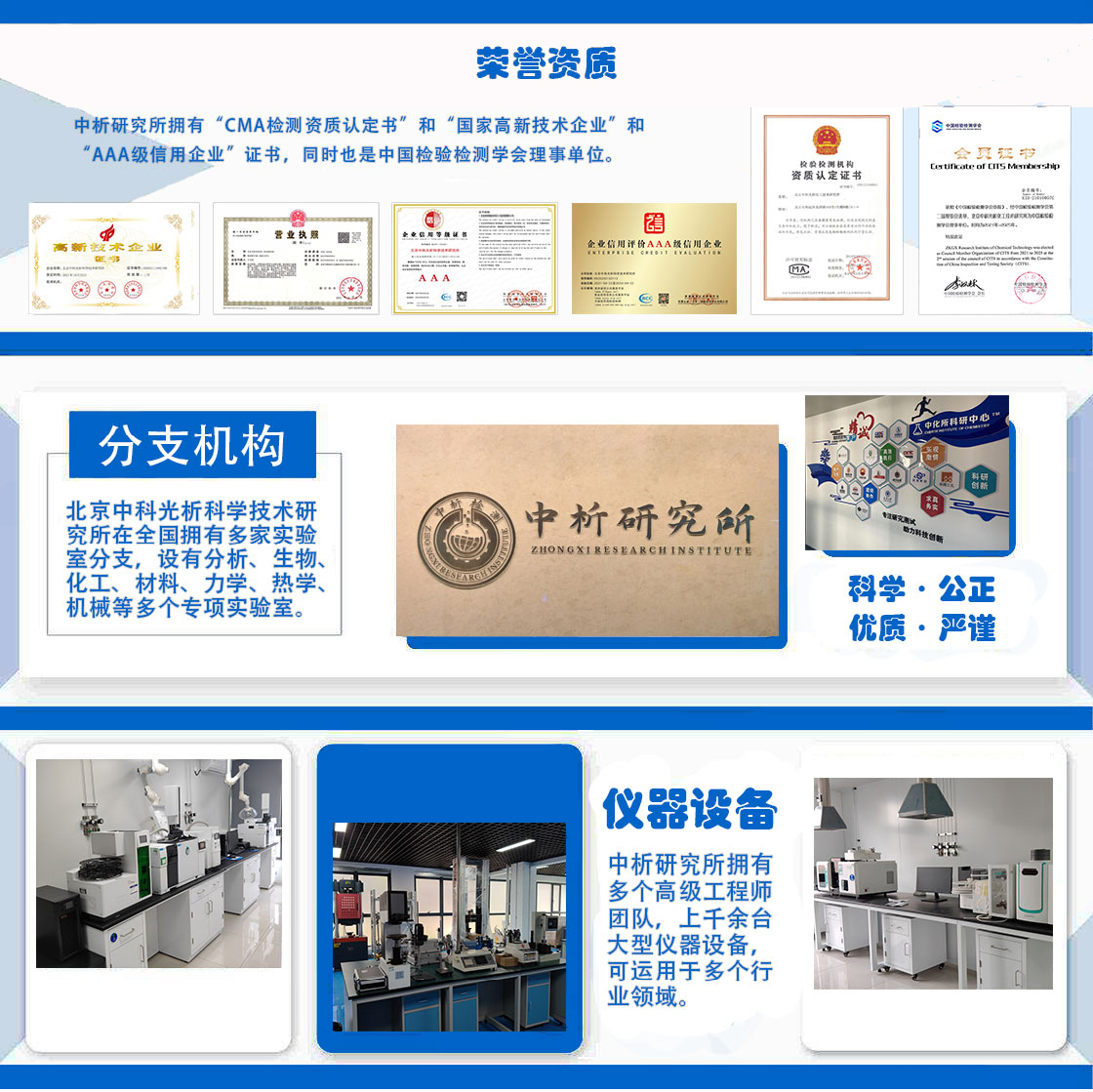
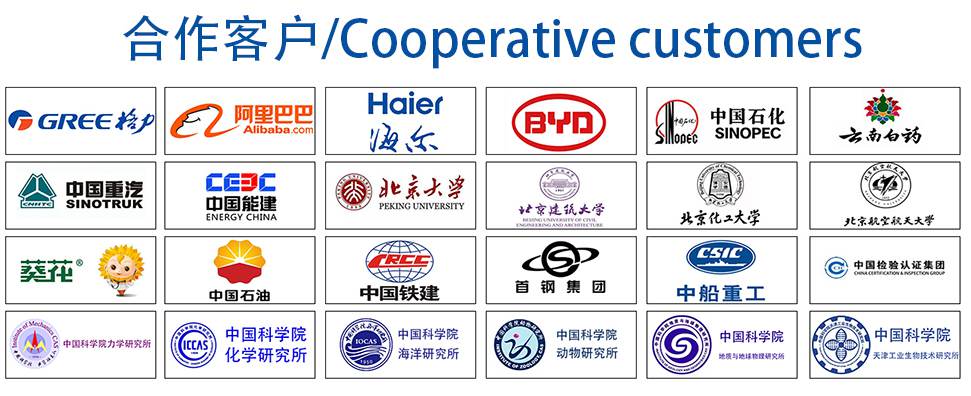
材料实验室
热门检测
26
23
22
23
22
20
20
21
21
21
23
21
19
21
21
21
21
19
25
21
推荐检测
联系电话
400-635-0567