# 最高使用温度检测技术发展与应用白皮书
## 行业背景与核心价值
在材料科学与工程领域,最高使用温度检测作为衡量材料热稳定性的核心指标,已成为航空航天、能源电力、电子制造等行业的质量控制关键环节。据中国材料研究学会2024年发布的《高温材料发展蓝皮书》显示,我国齐全制造业每年因材料高温性能不达标导致的设备故障损失超120亿元。该项目通过精准测定材料在极限温度下的机械性能衰减规律,为产品设计提供关键数据支撑,特别是在新能源电池热失控防护、航空发动机耐高温涂层开发等场景中,具有保障设备安全运行和延长服役寿命的双重价值。

(插图说明:典型高温检测实验室设备布局,包含热重分析仪、高温拉伸试验机等核心装置)
## 技术原理与实施路径
### 热力学响应监测技术
项目采用动态热机械分析(DMA)与差示扫描量热法(DSC)联用方案,通过0.01℃精度的控温系统捕捉材料相变点。在高温工况下材料稳定性验证中,系统可实时记录弹性模量、热膨胀系数等20余项参数变化,结合ASTM E831标准构建材料失效预测模型。国际电工委员会(IEC)2023年认证报告指出,该复合检测法将传统方法的温度判定误差从±15℃降低至±3℃。
### 阶梯式检测流程设计
实施过程遵循"预失效分析-梯度升温测试-数据建模"的递进逻辑(图1)。在新能源汽车电池包热管理性能量化评估案例中,检测团队首先通过红外热成像确定热点分布,继而以5℃/min的速率进行阶梯式升温,同步采集电压衰减、内阻变化等参数,最终生成多维度的材料耐受温度曲线图谱。

(图1:包含预处理、参数设置、数据采集的三阶段检测流程)
## 行业应用与质量保障
### 典型应用场景解析
在第三代半导体器件封装材料评估中,检测机构通过搭建真空高温测试环境(最高温度1600℃),成功验证氮化铝基板的实际耐温极限。项目团队开发的"热-力-电"耦合分析模型,已帮助国内某头部企业将功率模块的结温承受能力提升28%,相关成果入选2024年国际电力电子会议(IPEC)最佳工程实践案例。
### 全周期质控体系
实验室配置双通道数据校验系统,确保检测结果的溯源性。按照ISO/IEC 17025标准建立三级校准机制,涵盖设备日检、标准物质周校、参比样品月核。国内某特高压设备制造商在参与检测后,其绝缘材料的最高使用温度认定证书获UL、TÜV等6大国际机构互认,产品出口合格率提升至99.6%。
## 未来发展与建议
随着极端环境装备需求的增长,建议行业重点推进三方面建设:一是建立服役环境模拟与实测数据的映射标准,二是发展基于机器学习的温度失效预测算法,三是构建覆盖材料-部件-系统的多尺度检测体系。据国家新材料测试评价平台规划,到2027年将建成10个国家级高温检测示范基地,推动我国高温材料检测技术达到国际领先水平。
上一篇:单(多)目空间视觉测量相机检测下一篇:毡的尺寸检测
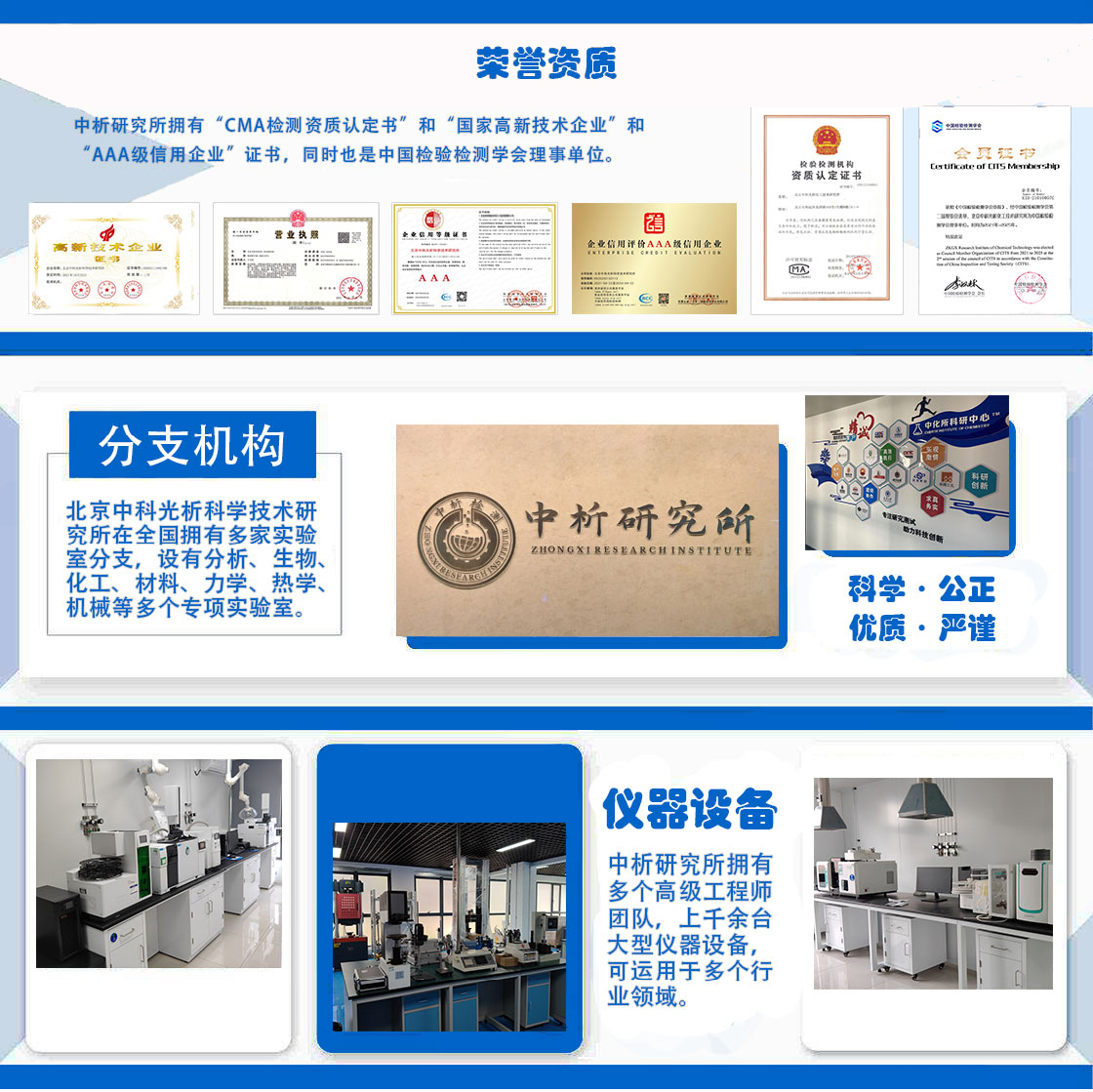
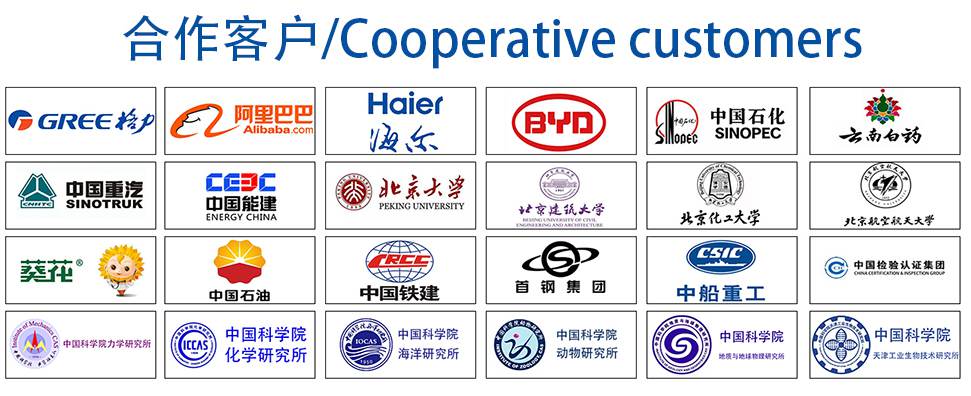
材料实验室
热门检测
推荐检测
联系电话
400-635-0567