耐候性(外观)检测技术发展与行业应用白皮书
在气候变化加剧与材料性能要求提升的双重驱动下,耐候性检测已成为材料科学领域的重要研究方向。据Global Market Insights 2024年报告显示,老化试验设备市场规模预计在2030年突破28亿美元,年复合增长率达6.5%,其中外观保持性检测需求占比超过40%。该项目通过模拟极端气候条件,系统评估材料在紫外线、温湿度、盐雾等复合应力下的表观性能变化,对光伏组件、汽车涂层、建筑幕墙等行业的品质控制具有关键意义。其核心价值在于量化预测材料服役寿命,降低因外观失效导致的产品召回风险,据ASTM国际标准委员会测算,有效的外观耐候检测可减少30%以上的售后维护成本。
光化学老化机理与检测技术体系
耐候性检测基于光降解与热氧老化耦合作用原理,采用QUV紫外光老化箱和Q-SUN氙灯试验箱分别实现加速老化模拟。前者通过UVA-340灯管精准复现295-365nm太阳短波辐射,后者依托全光谱氙灯与喷淋系统还原湿热循环环境。检测过程需同步监测黄变指数ΔYI、光泽度保留率及表面裂纹扩展等关键指标,其中高分子材料老化机理分析表明,羰基指数每增加0.1%将导致抗冲击强度下降15%(据中国建筑材料研究院2023年数据)。
标准化检测流程与技术创新
实施流程遵循ISO 4892-3标准,建立"预处理-加速老化-性能评估"三阶段体系。某汽车制造商在新型电泳漆检测中,采用85℃/85%RH湿热环境叠加0.55W/m²紫外线辐照的复合方案,经2000小时测试后涂层粉化等级仍保持1级(SAE J2527标准)。行业头部检测机构已引入原位FTIR光谱技术,实现老化过程中化学结构变化的实时监控,检测效率较传统方法提升40%。
跨行业应用与质量保障
在光伏领域,双玻组件通过300kWh/m²紫外剂量测试后,EVA胶膜黄变指数需控制在2.0以下(TUV莱茵认证要求)。某TOPCon电池厂商采用周期性冷凝-辐照交替方案,使封装材料透光率衰减率从年均3.2%降至1.8%(Fraunhofer ISE 2024年数据)。质量保障体系涵盖设备定期校准( CL01标准)、操作人员ASTM D7869资质认证及大数据比对分析平台,确保检测结果偏差率≤1.5%。
技术发展与产业建议
建议行业重点研发多因素耦合加速试验设备,开发基于机器视觉的表面缺陷自动评级系统。鼓励建立区域性大气暴露试验站网络,构建中国特殊气候带(如琼海湿热站、敦煌干热站)的自然老化数据库。推动制定《户外用复合材料耐候分级标准》,将动态机械分析(DMA)纳入强制检测项目,为"双碳"目标下的材料耐久性设计提供支撑。
随着AI技术在材料失效预测中的应用深化,耐候性检测正从单一参数测试向全生命周期模拟转变。建议产业链上下游协同建立"加速老化-实际服役"关联模型,发展基于数字孪生的虚拟检测技术。同时需加强热带雨林、工业大气等特殊环境的检测方法研究,为"一带一路"沿线基建项目提供精准的耐候性解决方案。
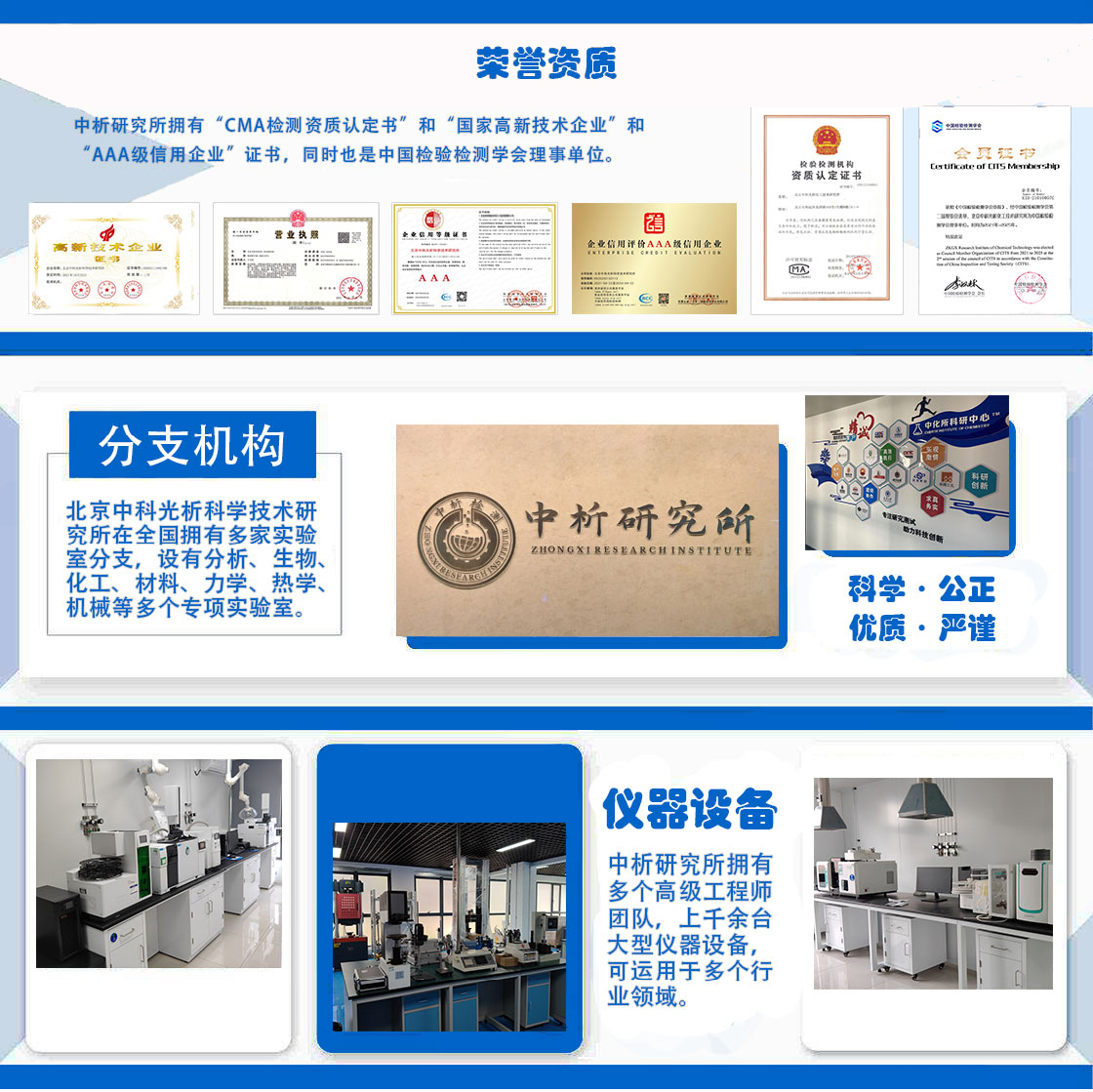
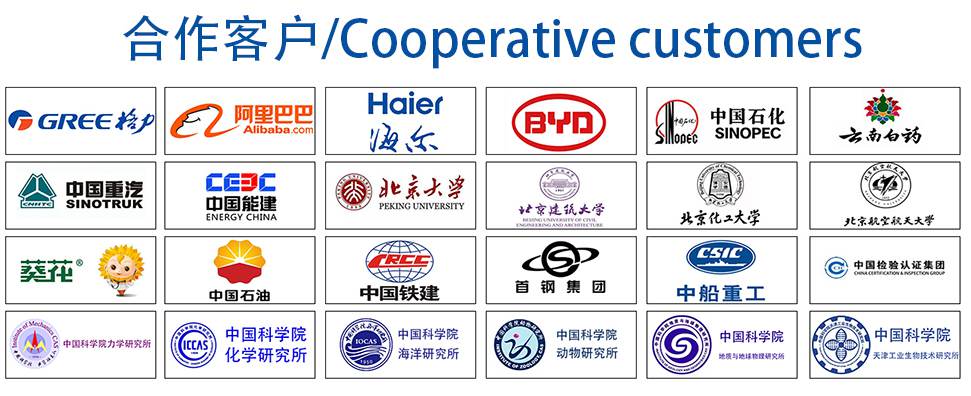