垂直度与平整度检测技术指南
一、垂直度检测项目详解
1. 建筑工程检测
- 检测对象:承重墙、立柱、电梯井道、门窗框
- 工具方法:
- 激光垂准仪:发射垂直激光束,测量墙面偏移量(高层建筑精度达±3mm/100m)
- 经纬仪测绘:双面测量法消除仪器误差,适用于钢结构立柱安装
- 验收标准:
- 混凝土结构验收规范(GB50204):层高≤5m时允许偏差8mm
- 幕墙工程:立柱直线度偏差≤3mm/3m
2. 机械制造检测
- 关键部位:机床导轨、液压缸内壁、法兰盘端面
- 精密测量:
- 三坐标测量机(CMM):采用最小二乘法计算平面垂直度,重复精度0.5μm
- 直角尺+塞尺组合:适用于小型工件快速检测,0级直角尺公差3μm/100mm
- 行业标准:
- ISO 2768-1:未注公差等级m级允许0.3mm垂直度偏差
- 汽车发动机缸体:主轴承座垂直度要求≤0.02mm
二、平整度检测核心项目
1. 建筑地面检测
- 激光扫描系统:
- 三维激光扫描仪生成点云数据,计算标准差(SD值)
- 机场跑道要求SD≤2mm/3m直尺
- 关键参数:
- 国际平整度指数(IRI):高速公路要求IRI≤2.0m/km
- F-Number体系(F20-F60):半导体车间要求F50以上
2. 工业生产检测
- 钢板轧制检测:
- 在线激光轮廓仪:每秒2000点采样,检测波形弯曲度
- 冷轧板带不平度要求≤3mm/m
- 光学平台检测:
- 干涉仪检测:λ/20精度(He-Ne激光λ=632.8nm)
- 大理石平台平面度分级:00级达0.5μm/1000mm
三、前沿检测技术对比
技术类型 | 检测效率 | 典型精度 | 适用场景 |
---|---|---|---|
激光跟踪仪 | 15点/分钟 | ±15μm+5μm/m | 大型装备组装 |
结构光扫描 | 2m²/分钟 | 0.05mm分辨率 | 异形曲面检测 |
无人机航测 | 50公顷/天 | 地面分辨率5cm | 土方工程验收 |
微波测距系统 | 连续监测 | 0.01mm分辨率 | 大坝变形监测 |
四、常见问题处理方案
-
- 偏差10-20mm:采用聚合物砂浆找平层修复
- 偏差>30mm:植入钢筋网片进行结构性加固
-
- 激光整平机施工:每小时浇筑200㎡,平整度可达2mm/2m
- 环氧自流平:固化后表面高差≤1mm/3m
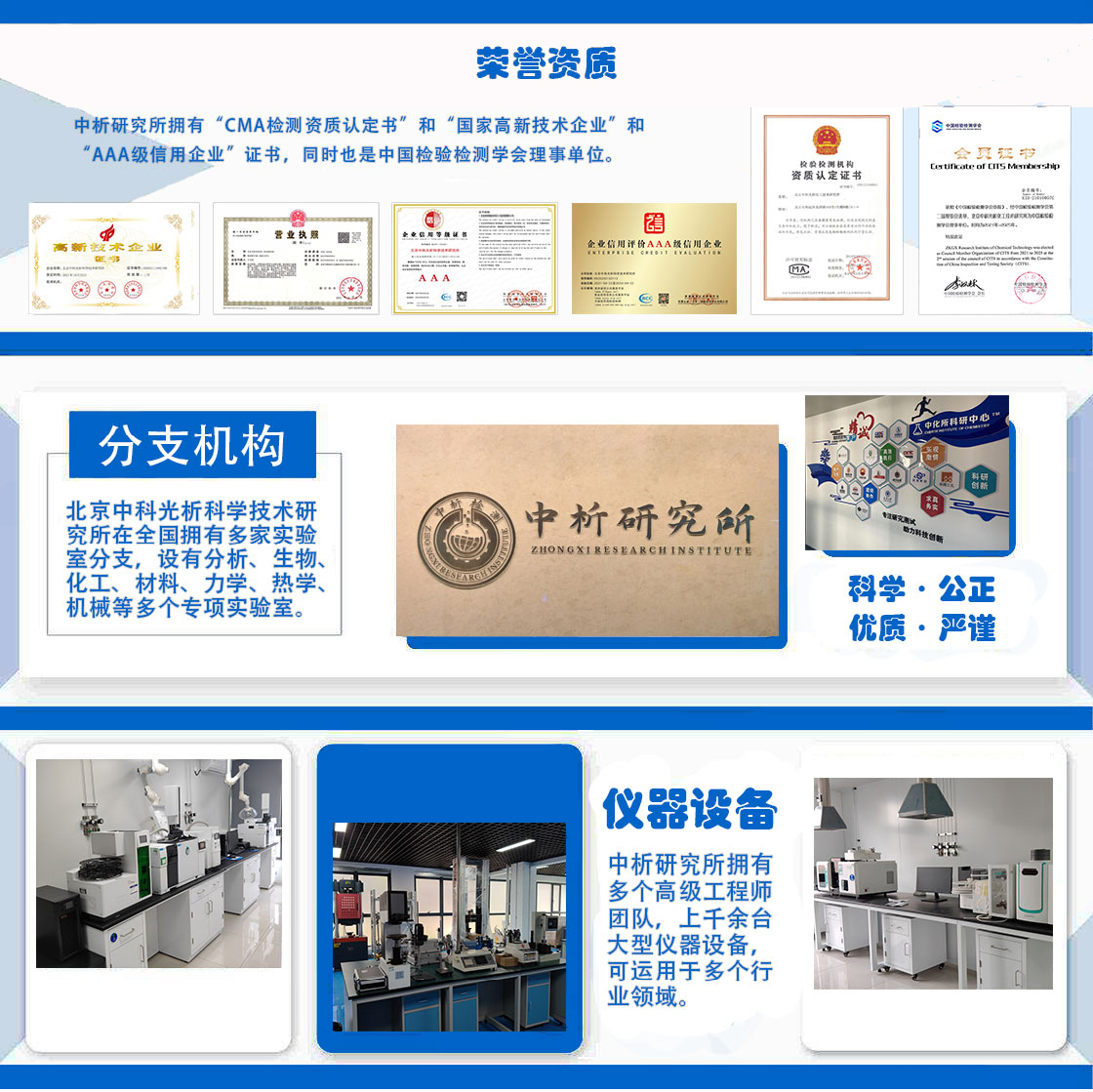
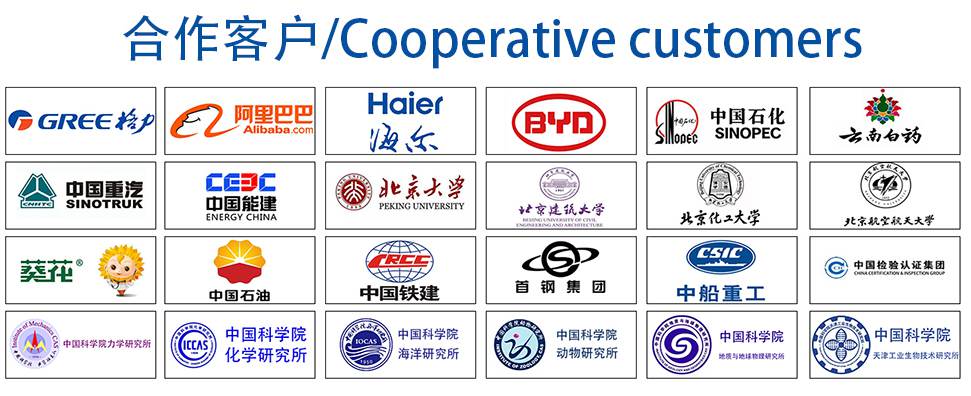
材料实验室
热门检测
29
32
31
32
51
45
55
47
50
52
43
55
44
52
45
48
43
50
45
45
推荐检测
联系电话
400-635-0567