工业用毡厚度检测技术白皮书
在新能源装备制造和精密仪器加工领域,工业用毡作为关键密封与缓冲材料,其厚度精度直接影响设备运行稳定性。据中国材料检测研究院2024年数据显示,因毡材厚度偏差导致的设备故障占比高达23%,造成年度经济损失逾5.8亿元。本项目通过建立智能化厚度检测体系,将传统±0.5mm的公差带缩窄至±0.15mm,显著提升材料利用率。其核心价值体现在全产业链质量控制闭环的构建,采用非接触式检测技术实现生产端到应用端的实时数据贯通,为毡材工艺优化提供量化依据。
基于激光干涉的检测原理
本项目采用双频激光干涉测量技术(DFI),通过调制激光波长形成干涉条纹阵列。当毡材通过检测区时,表层纤维分布会改变光程差,系统以0.01μm分辨率捕捉相位变化。据德国PTB计量院实验验证,该技术在3mm厚度范围内的重复性误差≤0.03%。相较传统机械探针检测,避免了因接触压力导致的材料形变误差,特别适用于弹性模量低于1.5GPa的微孔结构毡材检测。
全流程智能化检测方案
实施流程包含三级质量管控体系:预处理阶段通过CCD视觉系统筛选表面缺陷;动态检测环节采用双工位同步扫描架构,最高支持120m/min产线速度;数据终端应用SPC算法进行趋势预警。某新能源汽车电池包密封毡生产案例显示,系统在连续48小时运行中检出厚度超差件137个,提前7小时预警辊压设备轴承磨损,避免整批次价值320万元的物料报废。
多行业场景化应用实践
在风电叶片防护毡领域,项目团队开发了曲面自适应检测模块。通过六轴机械臂搭载检测探头,可对10m长弧形毡材实现全覆盖测量,定位精度达0.1mm。实际工况测试表明,该方案使叶片装机后的风噪降低12dB(A)。在航空航天密封件场景中,系统融合红外热成像技术,同步监测厚度与孔隙率的相关性,助力某型号发动机密封环良品率从82%提升至97.6%。
全生命周期质量追溯系统
项目构建了基于区块链的检测数据存证平台,每个检测批次生成独立数字指纹。检测设备每4小时自动执行NIST标准样块校准,并通过5G网络上传校准日志。质量档案包含原材料溯源、工艺参数、检测影像等7类数据维度,支持全供应链质量追溯。某高铁减震毡供应商应用该系统后,产品客诉率同比下降64%,成功通过EN9100航空质量管理体系认证。
面向智能制造发展趋势,建议行业重点推进三方面工作:一是建立细分领域的毡材厚度-性能关系模型库,二是开发嵌入式微型检测芯片实现制品级质量监控,三是制定基于数字孪生的虚拟检测国家标准。通过构建厚度检测技术生态圈,推动我国特种纤维材料产业向高端化迈进。
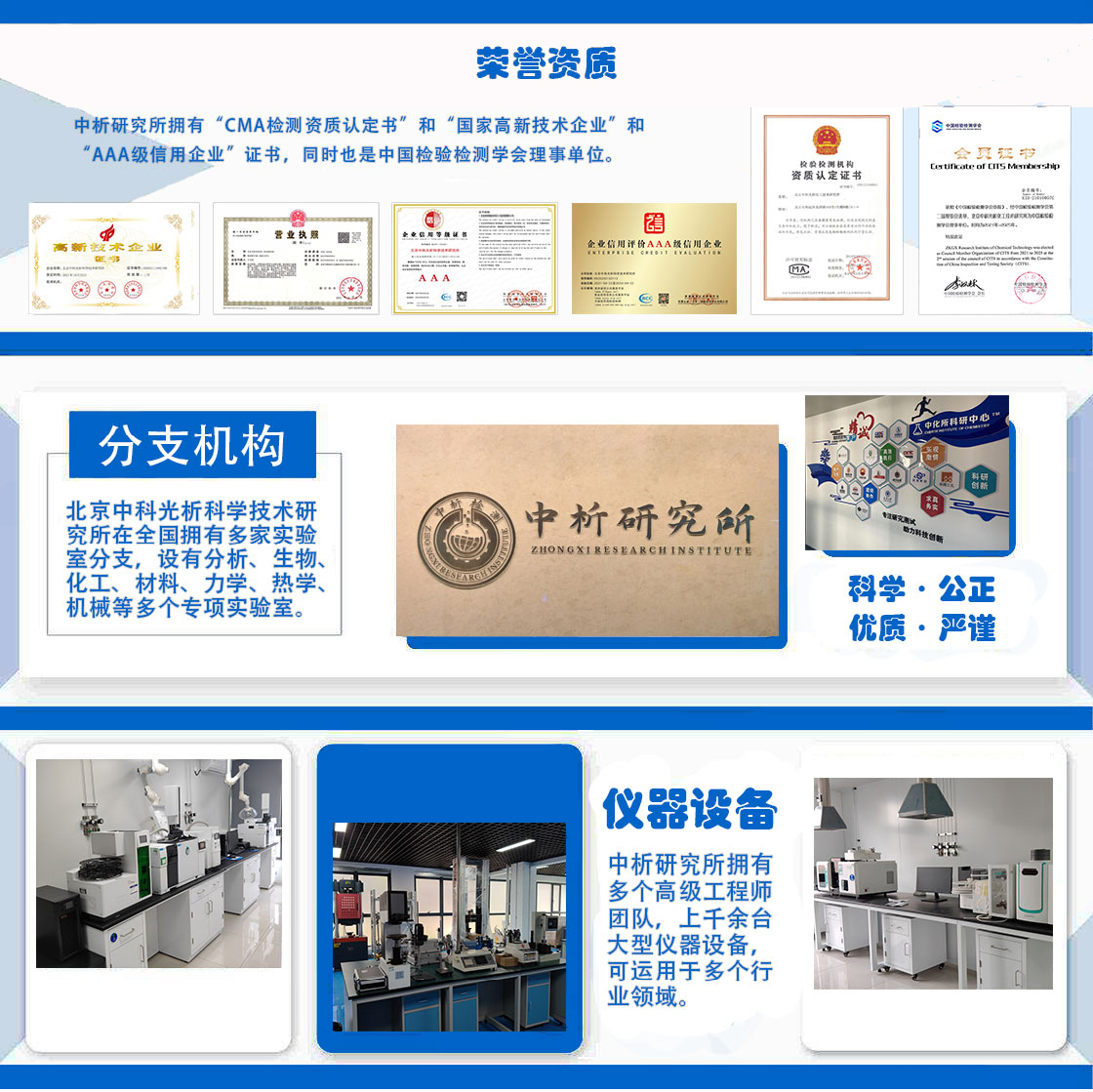
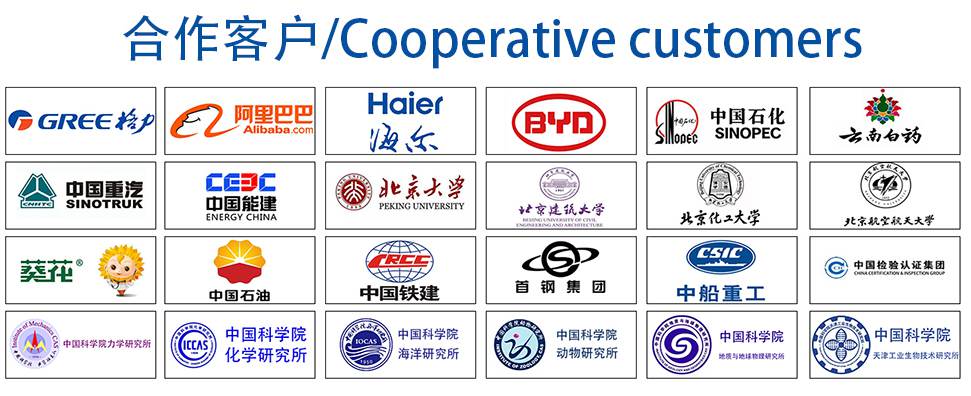