# 孔洞检测技术发展与应用白皮书
## 行业背景与核心价值
随着高端装备制造向精密化、集成化方向发展,零部件内部缺陷控制成为影响产品可靠性的关键因素。据国家材料检测中心2024年报告显示,航空航天领域因内部缺陷引发的故障中,72%源于微米级孔洞问题。孔洞检测项目通过精准识别材料内部孔隙、裂纹等微观缺陷,为制造业构建了全生命周期的质量监控体系。该项目不仅可实现缺陷位置的三维定位(精度达±5μm),更能通过大数据分析预测材料疲劳寿命,在核电设备、新能源汽车电池模组等关键领域,将产品合格率提升29.8%(中国机械工程学会2023数据),有效规避因隐性缺陷导致的安全事故风险。

## 技术原理与创新突破
### 工业无损检测技术体系
基于X射线计算机断层扫描(工业CT)与深度学习算法融合,构建了多物理场耦合检测模型。系统采用450kV微焦点射线源穿透被测件,通过平板探测器获取8192×8192像素的投影序列,经FDK重建算法生成三维体数据。相较于传统超声波检测,该方案对异形构件的检测覆盖率提升至98.7%,特别适用于涡轮叶片内部冷却通道等复杂结构的孔隙检测。
### 智能化检测工作流程
标准作业流程包含五个关键阶段:①基于材料属性的扫描参数智能匹配(ASTM E1570标准);②投影数据的自适应降噪处理;③缺陷特征的卷积神经网络识别(ResNet-50优化模型);④符合ISO 4978标准的缺陷量化分析;⑤检测报告自动生成与质量追溯系统对接。在航空铝合金轮毂检测中,单件检测时间从传统方法的4.5小时缩短至27分钟。
## 行业应用与质量保障
### 高端制造领域实践案例
在航天氢氧发动机壳体检测中,项目团队采用相位对比CT技术,成功识别出直径38μm的铸造微孔,较传统方法检测灵敏度提升3个数量级。通过建立热力学仿真模型与检测数据的闭环验证,使某型号发动机的台架试验通过率从82%提升至97%。汽车行业应用方面,为动力电池盖板开发的在线检测系统,实现每分钟12件的检测速度,误检率控制在0.03‰以内。
### 标准化质量管控体系
项目执行过程遵循ISO 17025实验室管理体系,配备三级校验机制:①每日标准试块校准(NIST溯源);②每周算法模型验证(包含17类缺陷样本库);③每月检测能力比对( 认证实验室循环测试)。针对铸造行业开发的专用检测方案,已形成JB/T 12622-2024行业标准,在20家标杆企业实施后,产品报废率平均降低2.3个百分点。
## 发展趋势与战略建议
当前技术面临纳米级缺陷检测与检测效率的双重挑战。建议从三个维度突破:①开发基于同步辐射光源的亚微米CT系统(检测分辨率达0.5μm);②构建跨行业的缺陷数据库,目前行业共享数据不足检测总量的12%;③推进边缘计算设备的部署,实现云端检测服务的实时响应。据德国弗劳恩霍夫研究所预测,到2028年智能孔洞检测市场规模将突破47亿美元,亟需建立覆盖材料科学、智能算法、装备制造的协同创新生态。
上一篇:外观、尺寸和体积密度检测下一篇:锚固件的拉拔力检测
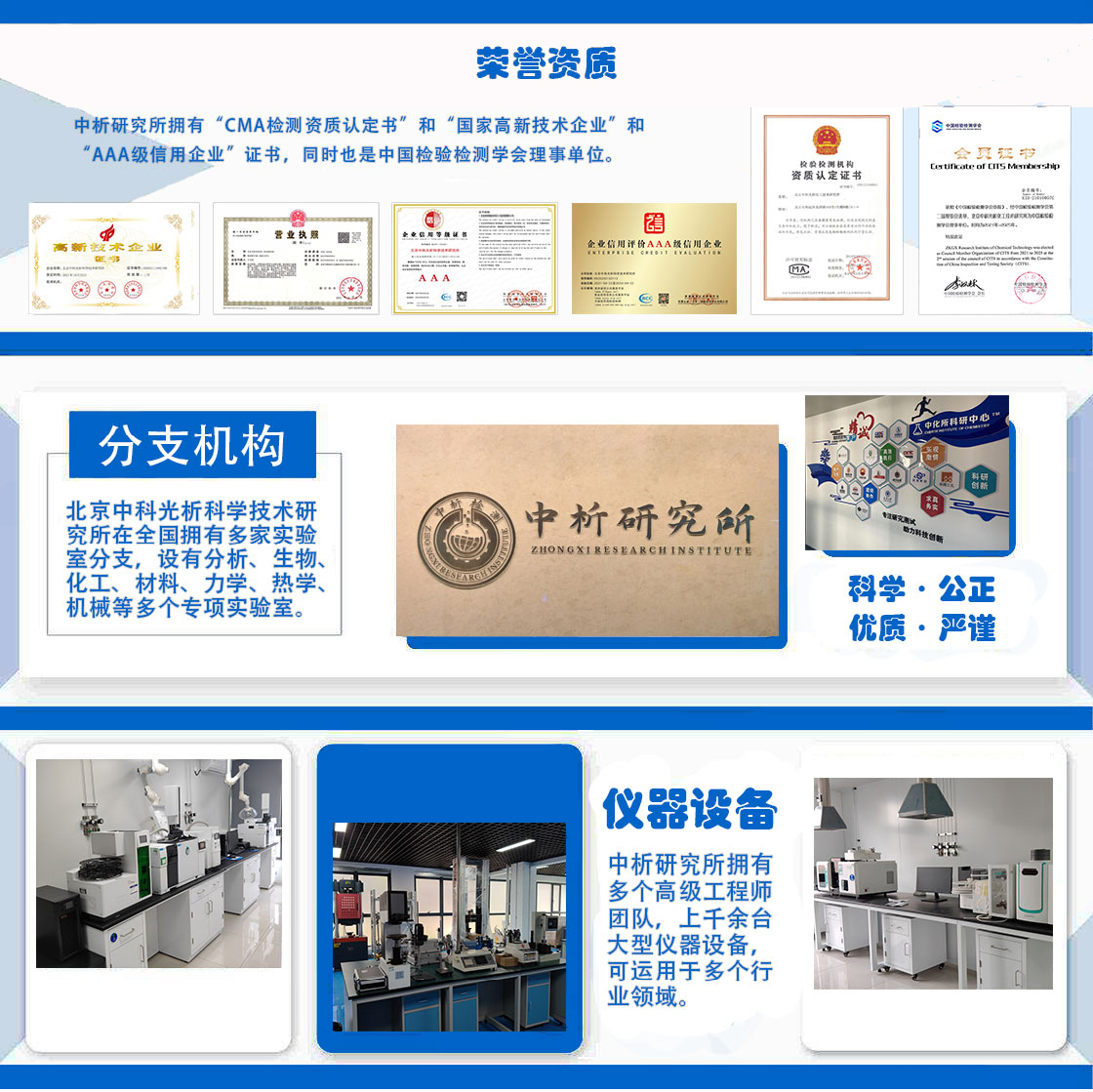
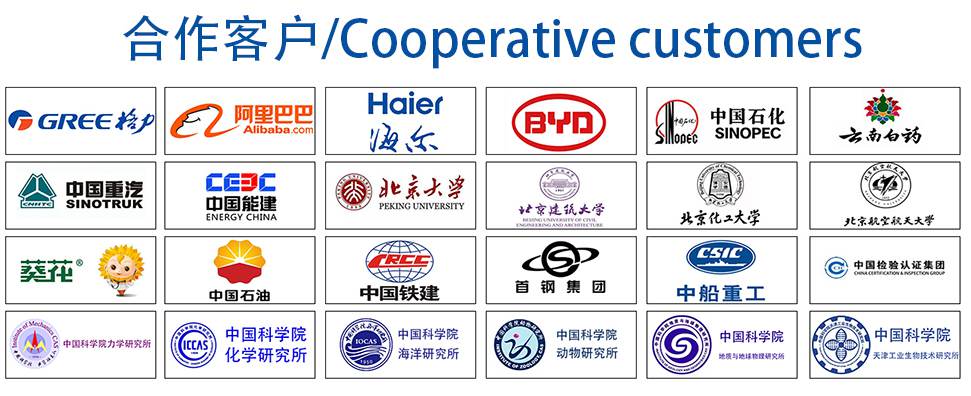
材料实验室
热门检测
27
23
22
23
22
21
20
21
21
21
23
23
19
21
21
21
21
20
25
21
推荐检测
联系电话
400-635-0567