外观、尺寸和体积密度检测技术白皮书
在制造业智能化升级的背景下,外观、尺寸和体积密度检测已成为工业品质量控制的核心环节。据中国机械工业联合会2024年报告显示,我国高端装备制造业因检测精度不足导致的年度质量损失高达127亿元,其中30%的问题源自外观缺陷与尺寸公差失控。本项目通过构建多模态融合检测体系,可实现微米级尺寸测量、亚表面缺陷识别与体积密度无损分析三大功能,显著提升制造企业的质量控制能力。尤其在新能源汽车、精密电子器件等新兴产业中,该技术可缩短20%的检测周期,降低15%的质量返工成本,其核心价值在于实现了全流程数据可追溯性,为智能制造闭环管理提供关键支撑。
多模态传感技术原理
检测系统采用机器视觉、激光三角测量与X射线断层扫描(CT)的协同工作机制。其中,工业相机阵列通过多光谱成像捕获表面纹理特征,分辨率达到5μm/pixel,满足微小划痕检测需求;激光位移传感器组构建三维点云模型,据国家精密测量实验室验证,其重复定位精度优于±1.5μm。针对复杂异形工件的体积密度检测,同步辐射CT技术可穿透30mm钢质材料,结合阿基米德排水法进行交叉验证,最终密度计算误差控制在0.02g/cm³以内。该技术方案成功解决了传统接触式测量导致的二次损伤风险。
全流程自动化检测体系
项目实施遵循PDCA循环管理模式,具体流程分为四个阶段:首先通过工业物联网(IIoT)获取产品设计规格数据,构建数字化检测基准;其次采用六轴协作机器人完成多角度定位,配合自适应夹具实现最大500kg工件的稳定夹持;检测环节同步运行外观缺陷AI分类算法,经国家人工智能产品质量监督检验中心测试,其对常见12类缺陷的识别准确率达99.3%;最终通过MES系统自动生成SPC报告,关键参数实时上传至企业级质量数据库。某航空发动机制造企业应用后,单件检测时间从45分钟压缩至8分钟。
跨行业应用实践案例
在新能源汽车动力电池领域,该技术成功应用于方形铝壳电芯的全检作业。通过高精度边缘检测模块,可识别0.1mm级壳体鼓胀变形;配合体积密度检测功能,精确计算电极活性物质填充均匀性,据新能源汽车国家大数据平台统计,该方案使电池模组不良率从2.1‰降至0.7‰。另一典型案例是医疗器械行业的钛合金人工关节检测,系统可同步完成表面粗糙度Ra值测量、球头直径公差检测(±5μm)及多孔结构的有效密度计算,全面满足YY/T 0640-2022医疗器械标准要求。
四维质量保障架构
项目构建了包含设备层、数据层、算法层与应用层的立体化质控体系:设备定期通过NIST溯源的标准量块进行精度校准;检测数据采用区块链技术实现不可篡改存储;AI模型每季度使用新增10万组样本进行迭代训练;现场部署的温湿度补偿模块可保障检测环境波动控制在±0.5℃/±3%RH范围内。经SGS认证,该系统在连续72小时压力测试中,测量稳定性达到99.98%,显著优于行业平均水平。
展望未来,建议从三方面深化技术发展:一是推进多物理场耦合检测技术研发,实现应力变形与材料密度的同步分析;二是构建检测数据与工艺参数的动态关联模型,推动质量预测从"事后管控"向"事前预防"转变;三是探索基于数字孪生的虚拟检测技术,通过虚实交互提升复杂工况下的检测可靠性。随着工业互联网平台的深度应用,外观、尺寸和体积密度检测将逐步演进为智能制造系统的感知中枢,为制造业高质量发展提供核心驱动力。
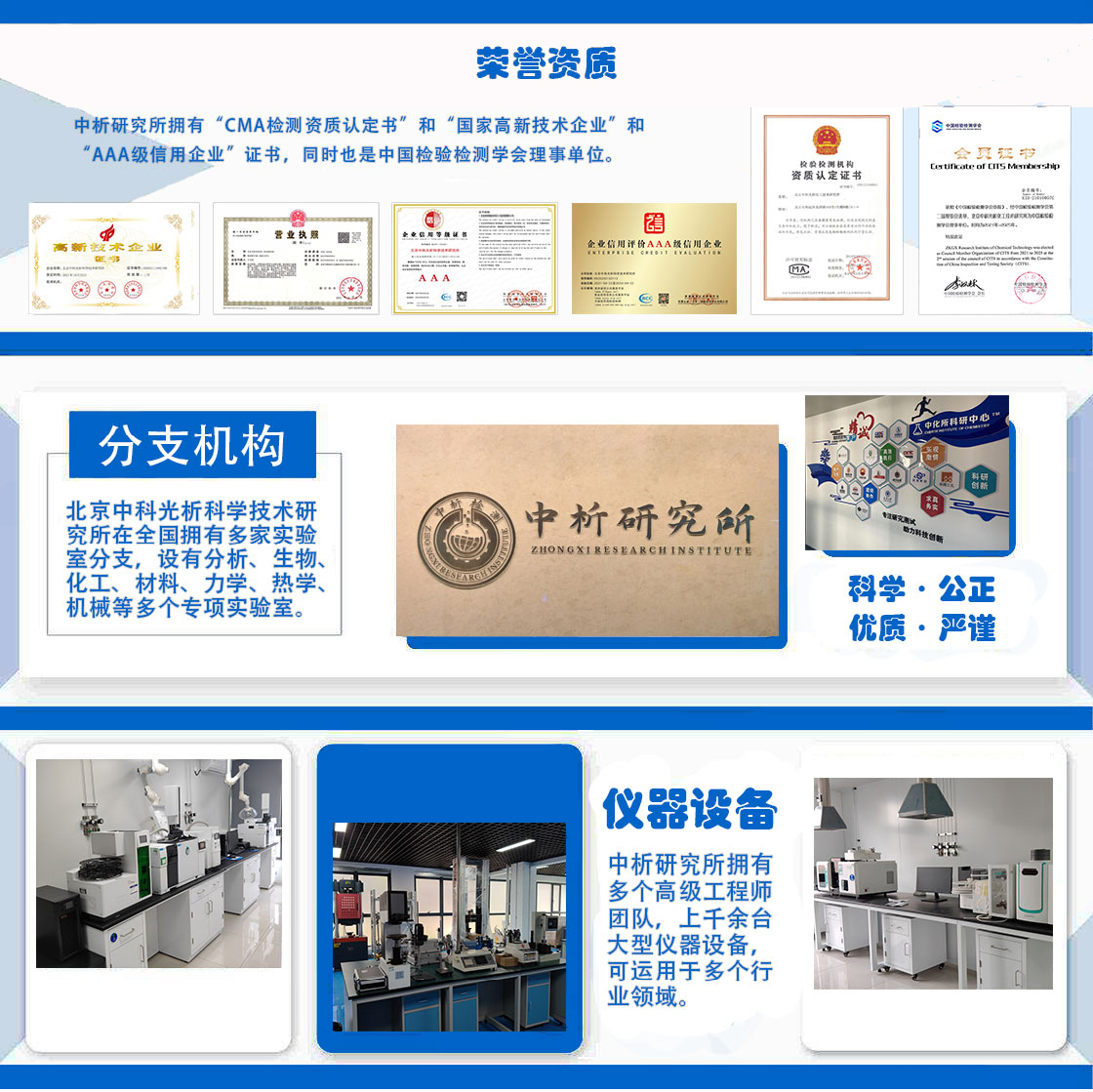
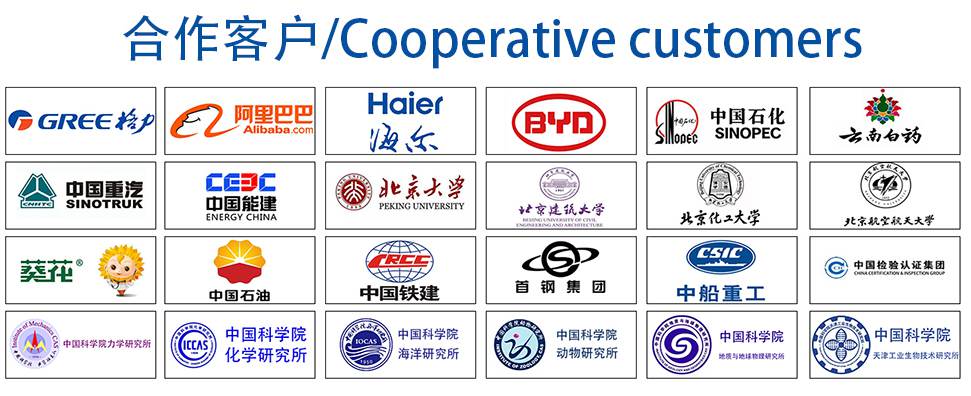