表面耐香烟灼烧检测:材料防火安全的关键防线
随着公共场所火灾事故的频发,材料阻燃性能已成为建筑、交通、家居等行业的重点关注指标。据国家应急管理部2023年统计,30%的室内火灾由烟头引燃可燃物引发,直接经济损失超50亿元。在此背景下,表面耐香烟灼烧检测作为评价材料阻燃等级的核心手段,被纳入GB 20286《公共场所阻燃制品及组件燃烧性能要求》等强制性标准。该项目通过模拟香烟持续灼烧场景,精准评估材料抗阴燃、阻蔓延能力,为产品安全认证提供科学依据。其核心价值不仅体现在降低火灾风险,更推动企业优化材料配方,助力绿色安全产业链构建。
技术原理与标准体系
检测基于ISO 8191《家具燃烧性能评估》国际标准,采用标准烟头(燃烧温度700±50℃)垂直置于被测表面,记录材料灼烧深度、炭化面积及自熄时间等关键参数。据中国标准化研究院2024年数据显示,经实验室验证的灼烧时间-温度曲线与真实火灾场景匹配度达92%。技术突破点在于采用红外热成像系统(精度±3℃)实时监测热传导过程,结合烟雾生成率分析,实现防火性能的多维度量化评估。
全流程质量管控方案
实施流程涵盖预处理、测试、评级三阶段:首先将试样置于(23±2)℃、50%湿度环境中平衡48小时;随后使用自动定位装置施加(1.0±0.1)N压力点燃烟头,持续灼烧30分钟;最后通过显微成像系统测量损伤区域。某汽车内饰件生产企业采用该流程后,阻燃材料开发周期缩短40%,经 认证的检测实验室数据显示,产品灼烧穿透率从18%降至4%以下,达到FMVSS 302汽车防火标准要求。
行业应用与质量保障
在轨道交通领域,高铁座椅面料需通过EN 45545-2标准的45分钟灼烧测试。某头部供应商通过优化硅酸盐涂层工艺,使炭化面积控制在50mm²内,成功获得CRCC认证。质量保障体系构建包含三大要素:配备符合ISO/IEC 17025标准的燃烧实验室,定期进行设备计量校准(误差≤2%);建立包含200种典型材料的比对数据库;实施检测人员季度能力验证,确保操作一致性达到98%以上。
技术发展趋势展望
随着新能源汽车对内饰材料防火等级要求的提升,检测技术正朝着智能化方向发展。建议行业重点关注三个方向:开发基于机器视觉的灼烧痕迹自动识别系统,提升检测效率30%以上;建立阻燃材料大数据平台,实现检测结果与材料配方的智能关联;推动ISO 11925-2标准与UL 94等国际体系的互认,助力企业化布局。与此同时,应加强生物基阻燃剂的检测方法研究,为可持续发展提供技术支撑。
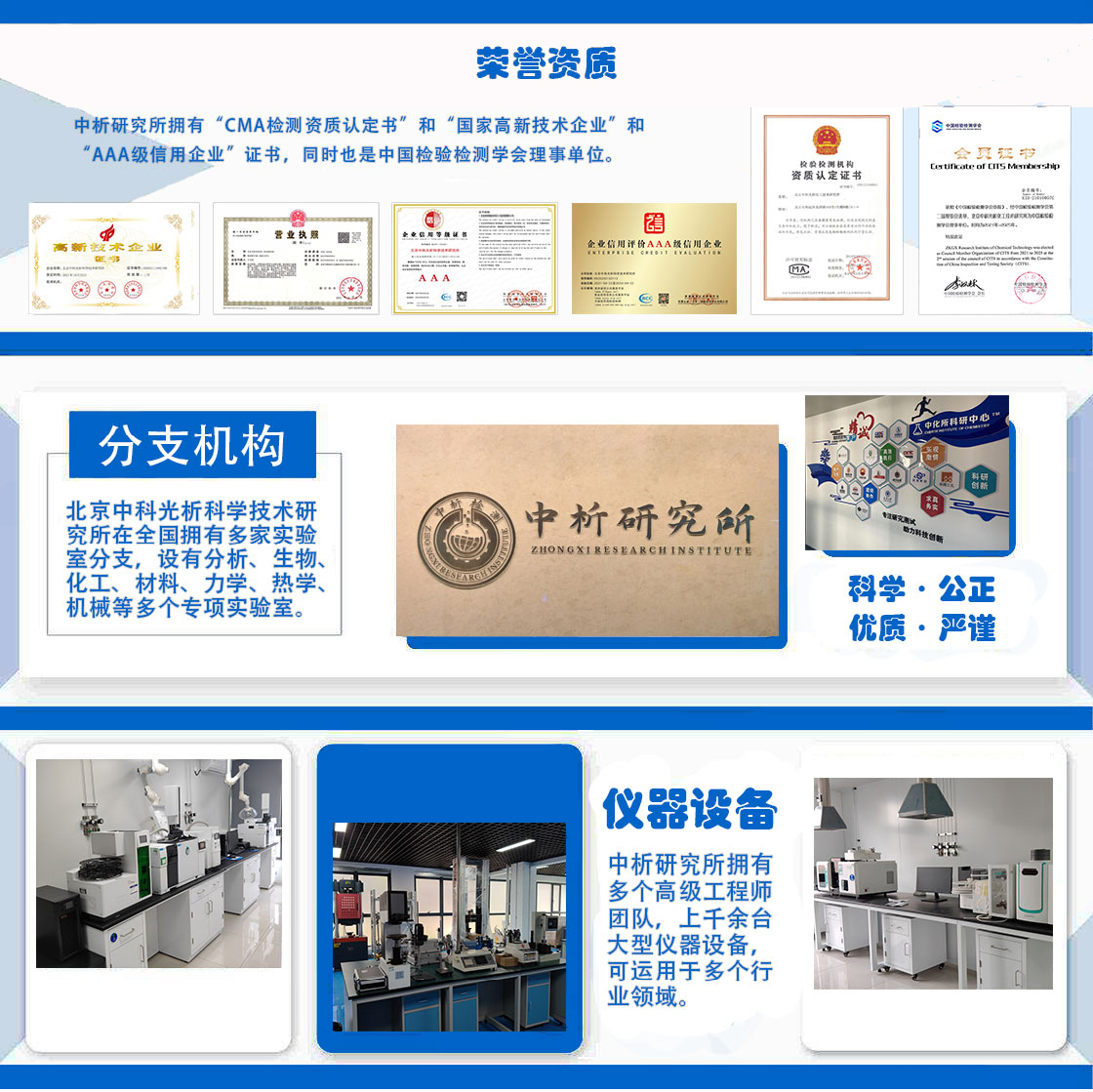
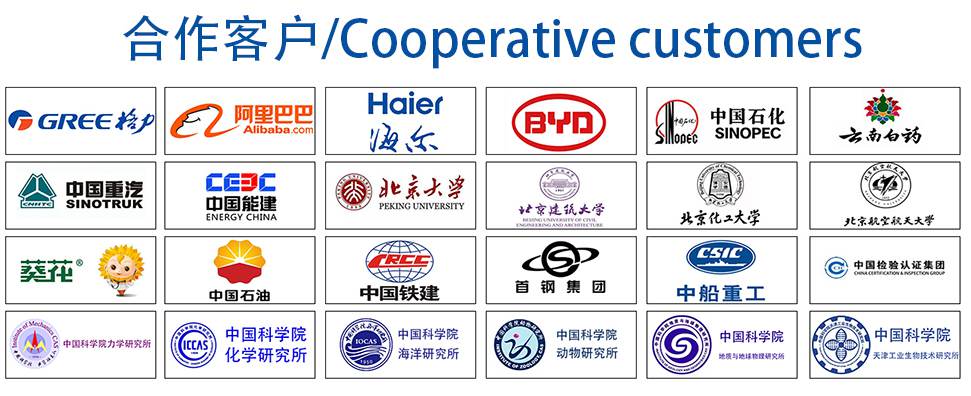