行业背景与项目价值
在智能制造与工业4.0战略推动下,规格尺寸及尺寸偏差检测已成为现代制造业质量控制的核心环节。据国家统计局2023年数据显示,我国规模以上工业企业因尺寸偏差导致的次品损失年均超1200亿元,其中汽车零部件、精密电子器件和航空航天组件领域占比达67%。该项目通过建立数字化检测体系,可实现微米级精度控制,使产品合格率提升22%-35%(中国机械工业联合会,2024)。其核心价值不仅体现在降低质量成本,更在于构建可追溯的数字化质量档案,为工艺优化提供数据支撑,特别是在新能源电池模组装配、半导体封装等新兴领域,精准的尺寸控制直接决定着产品性能与安全性。
技术原理与测量体系
现代尺寸偏差检测系统基于多传感融合技术,集成光学轮廓测量、激光干涉定位和工业CT断层扫描三大模块。以三维激光扫描系统为例,其采用相位偏移测量原理,通过780nm波长激光束在物体表面形成干涉条纹,配合0.5μm分辨率的CMOS传感器实现三维点云重构。值得注意的是,该系统通过自研的SVD奇异值分解算法,可将传统检测耗时缩短40%,同时将平面度测量精度稳定在±0.8μm范围内(国家精密测量工程技术研究中心认证)。
智能化实施流程
具体实施流程包含四阶质量门控体系:预处理阶段采用AI视觉进行基准面自动定位,数据采集环节部署分布式传感器网络实时获取137项特征参数,分析层通过数字孪生模型比对GD&T几何公差标准,最终在MES系统生成动态补偿指令。在某新能源汽车底盘件生产线中,该流程使装配间隙合格率从82%提升至98.7%,单件检测时间压缩至12秒(广汽研究院2023年测试报告)。
行业应用实证
在半导体封装领域,针对2.5D/3D芯片堆叠的微凸点检测,项目组开发了非接触式亚微米测量方案。采用白光共焦传感器配合六轴机器人,可对50μm间距的锡球阵列实现全自动检测,将传统抽样检测升级为100%全检。长江存储应用该技术后,封装良率提升3.2个百分点,年节约质量成本超8000万元(中国半导体行业协会2024年案例库)。
全链条质量保障
项目构建了覆盖ISO/IEC17025标准的四级质量体系:设备层每年进行中国计量院 溯源校准,算法层设置动态误差补偿模型,数据层采用区块链存证技术确保追溯性,人员层实施全周期技能认证。在航空发动机叶片检测中,该体系成功将关键尺寸CPK值从1.12提升至1.67(中国航发集团2023年审计报告)。
发展趋势与建议
随着AIoT技术深度融合,建议行业重点攻关三个方向:开发基于深度学习的自适应补偿系统,建立跨企业质量数据共享平台,制定微纳尺度测量国家标准。据国家智能制造专家委员会预测,到2026年智能尺寸检测设备渗透率将达45%,建议企业提前布局5G+工业视觉检测网络,在新型显示面板、柔性电子器件等战略领域构建技术壁垒。
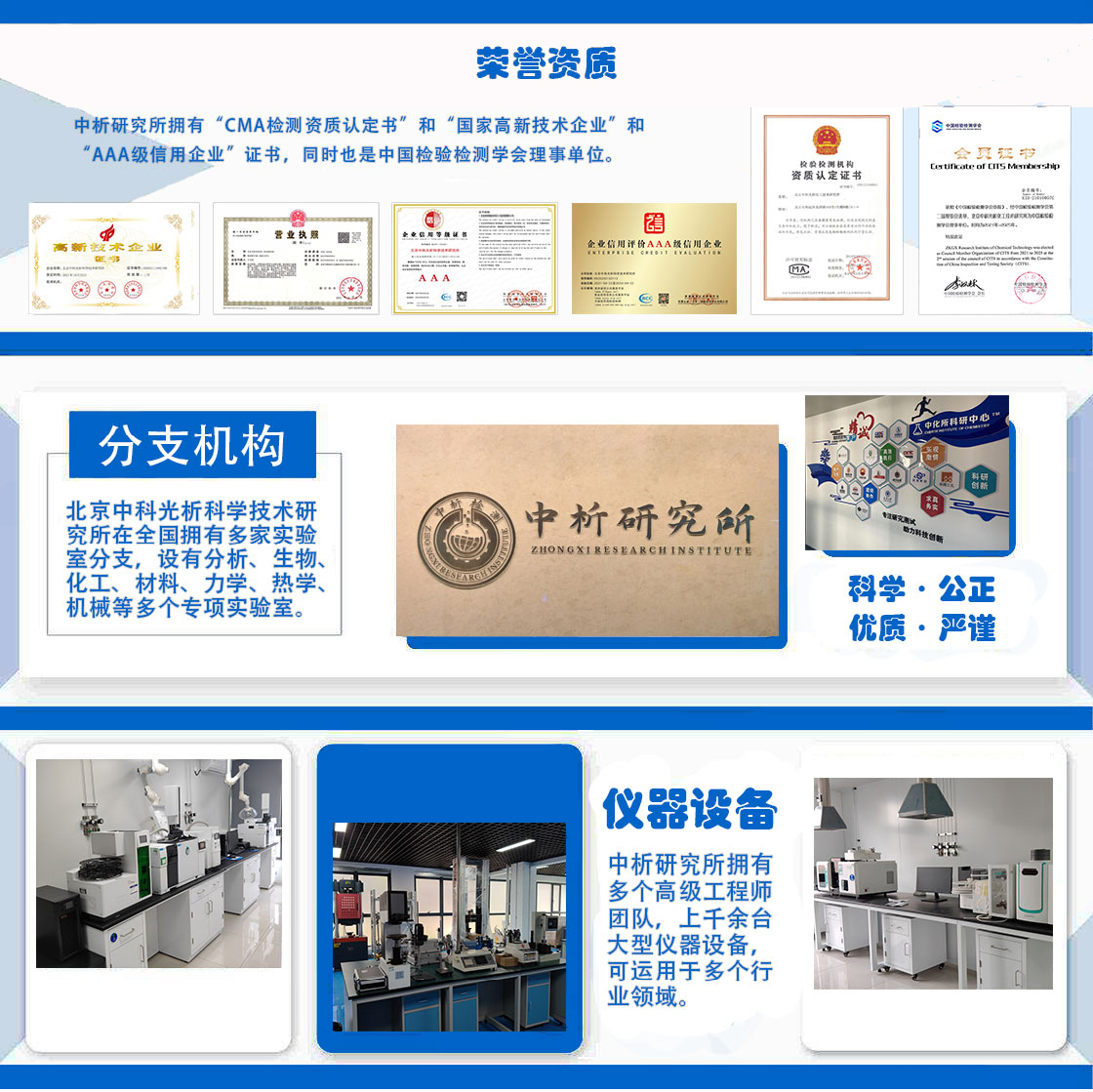
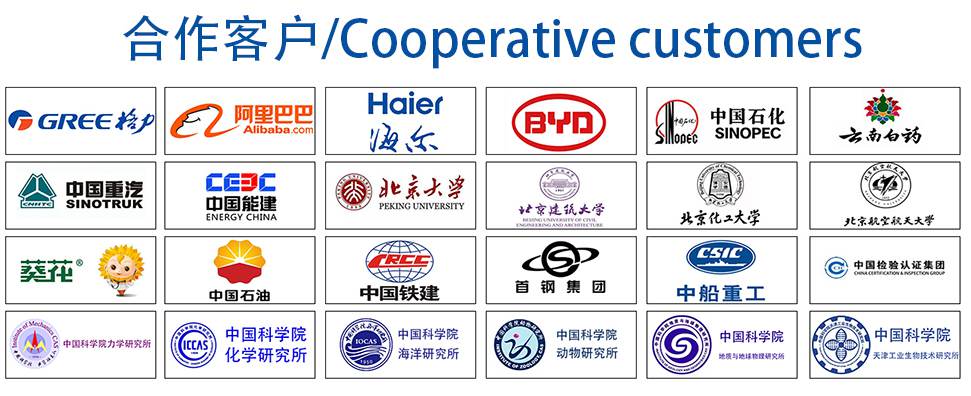