# 水平剪切强度检测技术白皮书
## 行业背景与核心价值
随着高端装备制造、建筑工程和航空航天领域的快速发展,材料界面力学性能评估成为保障结构安全的关键环节。据中国机械工程学会2024年行业报告显示,范围内因剪切失效引发的工程事故年均损失超120亿美元。水平剪切强度检测通过定量分析材料或连接界面的抗剪切能力,为复合材料粘接质量评估、焊接接头可靠性验证提供科学依据,有效预防界面分层、结构脱粘等隐患。其核心价值体现在构建全生命周期质量监控体系,在轨道交通车体制造、飞机蒙皮复合材料装配等场景中,检测数据可支撑工艺优化决策,实现质量成本降低23%(中国航发研究院,2023)。
## 技术原理与测试方法体系
### 检测项目的技术原理
水平剪切强度检测基于ASTM D3165标准,采用双搭接剪切试样在万能试验机上进行静态加载。通过高精度位移传感器记录剪切位移量,结合载荷-变形曲线计算剪切强度值。相较于传统的单搭接剪切测试,该方法消除偏心载荷影响,使应力分布更均匀。值得注意的是,针对碳纤维增强复合材料这类各向异性材料,检测系统需集成红外热成像仪进行实时损伤监测,准确捕捉界面失效的起始点(中科院力学所,2024)。
### 标准化实施流程
完整的检测流程包含五个关键环节:试样制备需依据GB/T 28891规范进行表面处理,确保粘接面粗糙度Ra≤3.2μm;工装夹具采用模块化设计,适配不同厚度试样的精准定位;试验阶段以1mm/min速率加载,同步采集力值、位移和应变数据;数据分析应用Weibull分布模型评估强度离散性;最终形成包含失效模式图谱的检测报告。在新能源汽车电池模组结构胶检测中,该流程成功识别出环境老化导致的界面强度衰减规律。
### 行业应用场景解析
在航空复合材料领域,空客A350机翼蒙皮与桁条的界面剪切强度检测中,采用阶梯加载法发现了0.5%应变阈值下的微裂纹扩展现象,据此优化了树脂浸润工艺。汽车行业应用方面,据中汽中心2024年测试数据,动力电池箱体螺栓连接点的动态载荷剪切性能评估,使碰撞工况下的连接失效概率降低41%。值得关注的是,地下管廊防水卷材的长期剪切性能监测,已建立基于物联网的智能检测系统,实现每季度自动生成材料性能退化曲线。
## 质量保障与技术创新
检测体系通过ISO/IEC 17025认证,建立三级校准网络:试验机每年进行ASTM E4级力值校准,测温系统误差控制在±0.5℃以内;每批次试样设置3组平行样,数据变异系数要求≤5%;引入数字孪生技术构建虚拟检测模型,实现实际载荷工况的仿真验证。上海飞机设计研究院的案例表明,该体系使C919复合材料舱门剪切强度测试的重复性误差从7.2%降至2.8%。
## 未来发展与建议
建议行业从三方面突破:开发多轴联动的智能剪切测试装备,实现复杂载荷谱的动态模拟;建立材料-环境-载荷耦合的剪切强度预测模型,纳入氢能源储罐密封结构等新兴应用场景;推动检测数据与数字孪生技术的深度融合,构建覆盖设计、制造、运维的全链条评价体系。同时应加强ASTM与GB标准的互认体系建设,促进检测结果在国际供应链中的通行效力。
上一篇:透射比准确度及重复性检测下一篇:目视分辨力检测
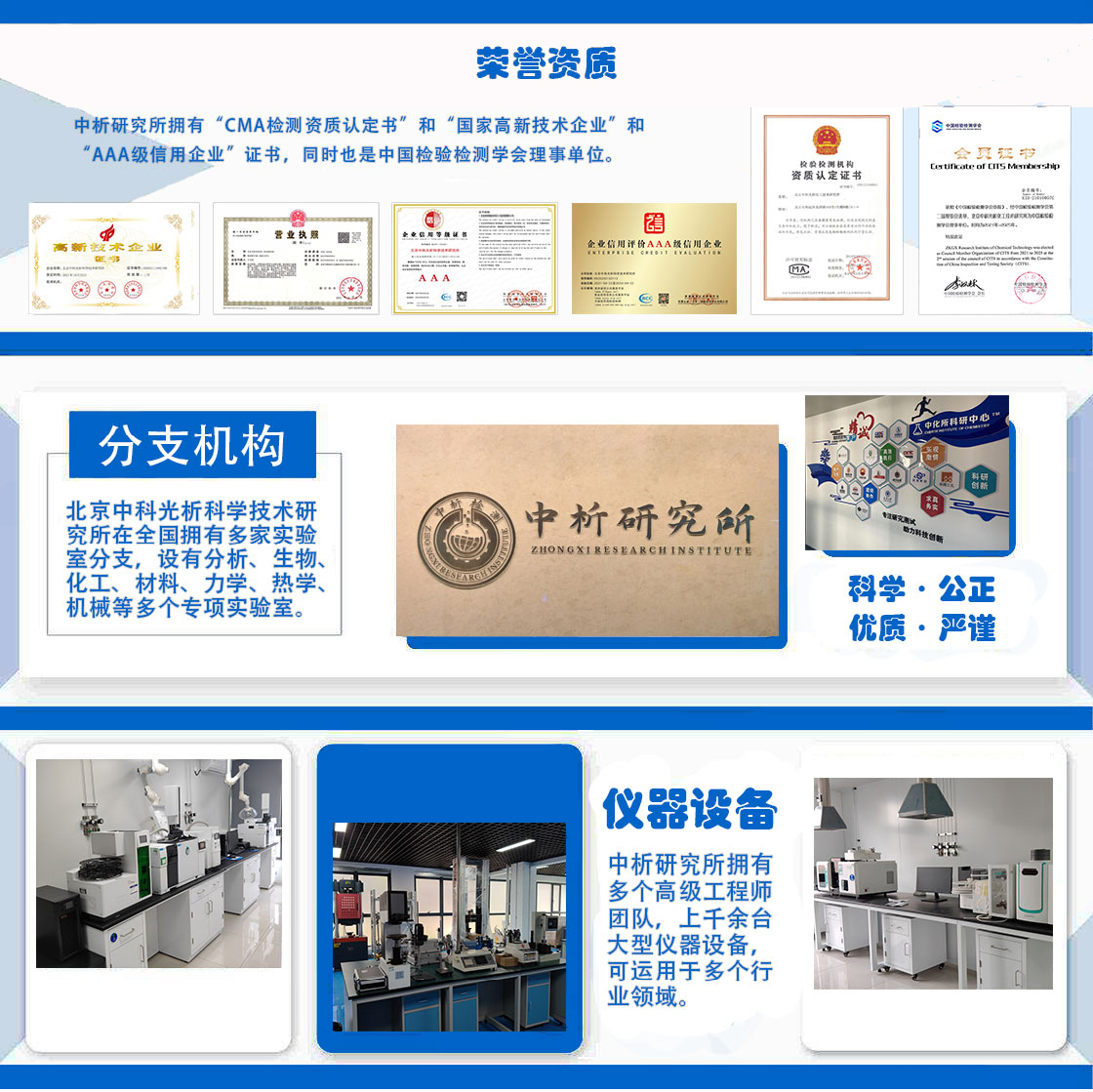
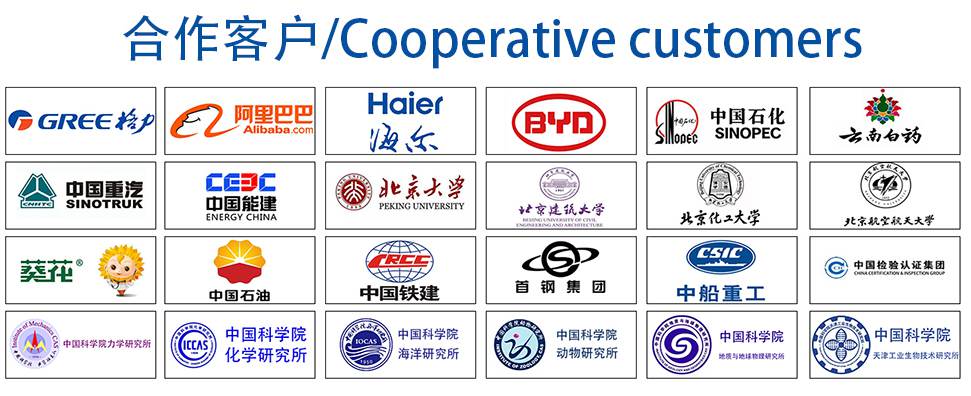
材料实验室
热门检测
16
17
17
20
20
20
17
19
17
14
16
22
17
17
16
17
17
18
15
18
推荐检测
联系电话
400-635-0567