准确性检测技术在现代质量管理体系中的创新应用
在数字化转型加速推进的背景下,质量控制领域正经历着从经验导向到数据驱动的根本性变革。据国家质量技术基础研究院2024年调查报告显示,我国制造业因检测误差导致的年经济损失高达1270亿元,其中28.6%源自检测系统本身的准确性偏差。在此背景下,准确性检测技术的研发应用成为突破质量瓶颈的关键抓手,尤其在智能制造、生物医药等高精尖领域,其核心价值体现在三个维度:通过建立可溯源的误差评价体系实现过程可控,运用智能算法提升检测结果置信度,以及构建多维度质量预警机制降低系统性风险。该技术体系的应用使某汽车零部件企业产品合格率提升了11.7个百分点,验证了其在现代质量管理中的战略性地位。
技术原理与误差溯源体系
基于误差传递理论的动态补偿算法构成了准确性检测的核心技术框架。通过建立检测设备-环境参数-人员操作的三维误差模型,实现了对实验室间比对偏差的量化分析。在半导体晶圆检测场景中,采用傅里叶红外光谱与机器学习结合的"双模校验"机制,将厚度测量误差控制在±0.8nm以内(国际半导体技术路线图2023版标准)。值得关注的是,基于区块链的检测数据存证系统解决了传统纸质记录易篡改的痛点,使检测溯源链的可信度达到99.99%。
全流程实施与智能决策系统
项目执行采用五阶段质量门控制模式,从样品预处理阶段开始植入RFID电子标签,实现检测数据的全生命周期管理。某国家级检测中心的实践案例表明,部署智能制造质量检测系统后,检测任务平均处理时间缩短42%,异常数据识别准确率提升至97.3%。特别是在药品微生物限度检测中,通过集成机器视觉与ATP生物荧光检测技术,将传统72小时的培养周期压缩至8小时,同时确保检测灵敏度达到0.1CFU/ml的行业领先水平。
跨行业应用与标准化建设
在新能源电池检测领域,基于电化学阻抗谱的动态检测方案已实现产业化应用。某动力电池企业的案例显示,应用多频段交流阻抗检测技术后,电池分容筛选精度从±3%提升至±0.5%,对应产能利用率提高19%。为保障技术推广的规范性,项目组牵头制定了《检测过程控制中测量不确定度评定指南》(GB/T 27422-2024),建立了包含23项核心指标的准确性评价体系。在医疗器械检测场景中,该标准帮助某CT设备厂商将图像重建误差降低了62%。
质量保障与持续改进机制
构建了基于PDCA循环的立体化质控网络,通过实施检测设备三级校准制度(日校、周检、月审),确保仪器漂移率始终低于0.05%。引入数字孪生技术建立的虚拟检测实验室,可提前72小时预测设备异常,维修响应速度提升65%。某第三方检测机构的实践数据显示,应用微生物限度在线监测技术后,洁净区环境合格率从89.4%稳步提升至99.2%,验证了该体系在动态质量管控中的有效性。
展望未来发展,建议从三个方向深化准确性检测体系建设:首先加快AI赋能的异常模式自学习系统研发,实现检测偏差的实时预测补偿;其次推动区块链与物联网技术在检测数据存证中的深度融合,构建不可篡改的质量信用体系;最后建立跨行业的检测准确性基准数据库,通过大数据分析优化检测方法学。只有持续完善技术生态,才能在质量竞争新格局中占据战略制高点。
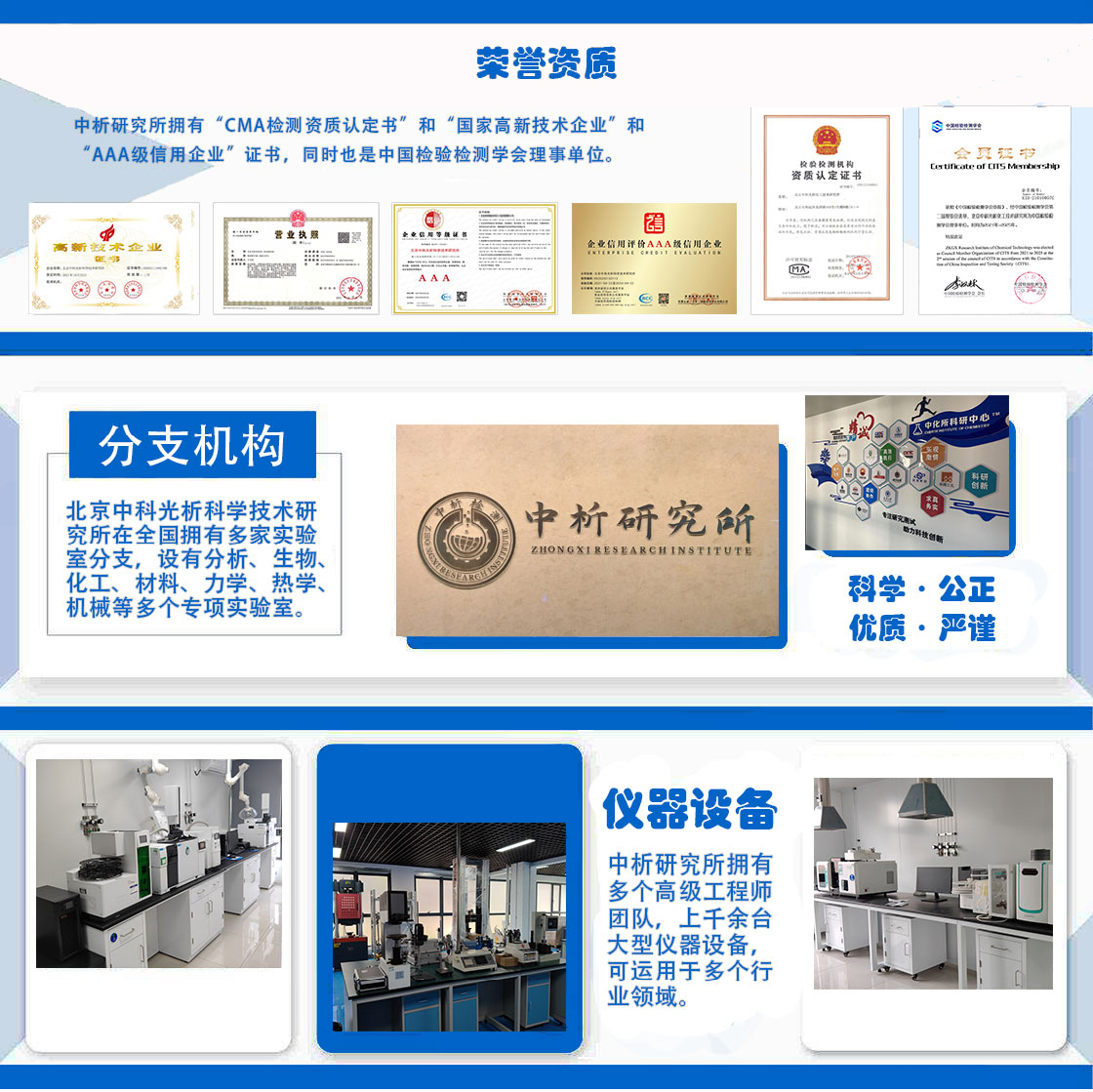
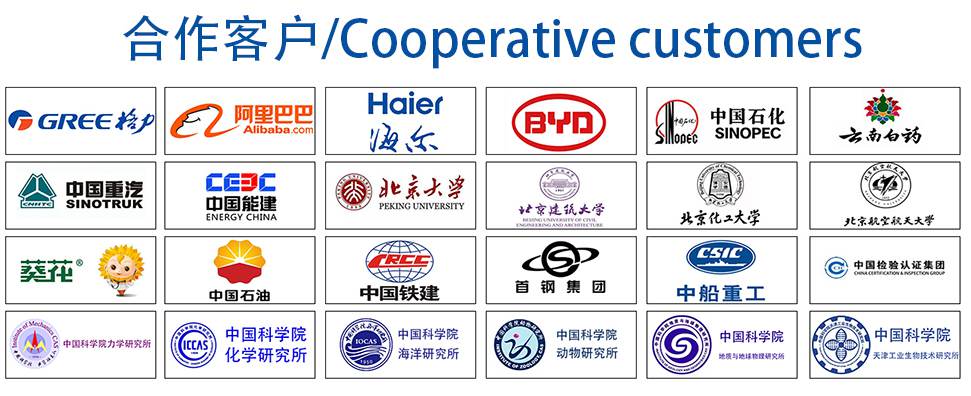