技术原理与误差建模
该检测基于双频激光干涉与数字图像处理融合技术,构建三维坐标系下的轴线空间关系模型。通过安装于精密转台上的电子自准直仪,实时采集视轴光斑在竖轴旋转360°时的位移轨迹(图1)。当存在同轴度误差时,光斑中心坐标将呈现周期性偏移,其最大径向距离经傅里叶变换后可分解为一次谐波分量,该分量数值即为同轴度误差量。实验数据表明,该方法的重复测量精度可达±0.3μm,满足ISO 17123-3标准对一级测量仪器的检测要求。
标准化检测流程设计
实施过程分为四个阶段:首先在恒温实验室进行24小时环境平衡,控制温度波动≤±0.5℃;接着使用AA级平面反射镜建立基准平面,配合0.01″级电子水平仪完成设备初始对准;检测阶段通过自动化转台以5°间隔采集72组位姿数据;最终由专用分析软件生成极坐标误差分布图并输出补偿参数。在2023年某省级计量院能力验证中,该流程成功识别出某进口全站仪0.8″的视轴偏心量,避免了高速铁路CPIII控制网的潜在系统性误差。
行业典型应用场景
在深埋隧道工程中,该技术有效解决了多测回观测数据发散问题。某跨海盾构项目采用改进后的对点器,将管片拼装轴线偏差从12mm降低至4mm以内。对于地质灾害监测领域,通过建立定期同轴度检测机制,某滑坡监测站的GNSS/全站仪融合测量数据一致性提升40%。值得关注的是,在新型智能施工机器人集成应用中,本检测方法为视觉定位系统提供了可靠的基准标定手段,使混凝土布料臂架的重复定位精度达到±1.5mm。
全链条质量保障体系
为确保检测结果的可信度,构建了从标准器溯源到作业规范的完整体系:采用NIM认证的激光干涉仪作为主标准器,每季度进行量值传递验证;开发带温度补偿算法的专用夹具,降低装卡应力引发的二次误差;培训认证体系要求操作人员需通过200小时实操考核。据2024年全国测绘仪器质量抽查数据显示,实施该体系的企业产品首次校验合格率从83%提升至96%,售后服务成本下降35%。
## 技术展望与发展建议 面向新型测绘装备智能化发展趋势,建议从三方面深化研究:首先开发集成机器视觉的在线检测装置,实现生产过程中的实时误差补偿;其次建立基于区块链的检测数据存证系统,完善仪器全生命周期质量档案;最后应加快制定针对无人机载、车载移动测量系统的动态同轴度检测标准。通过技术创新与标准升级双轮驱动,推动我国精密光学仪器检测能力向μm级迈进,为数字孪生城市、空天信息网络等新基建领域提供更坚实的质量保障。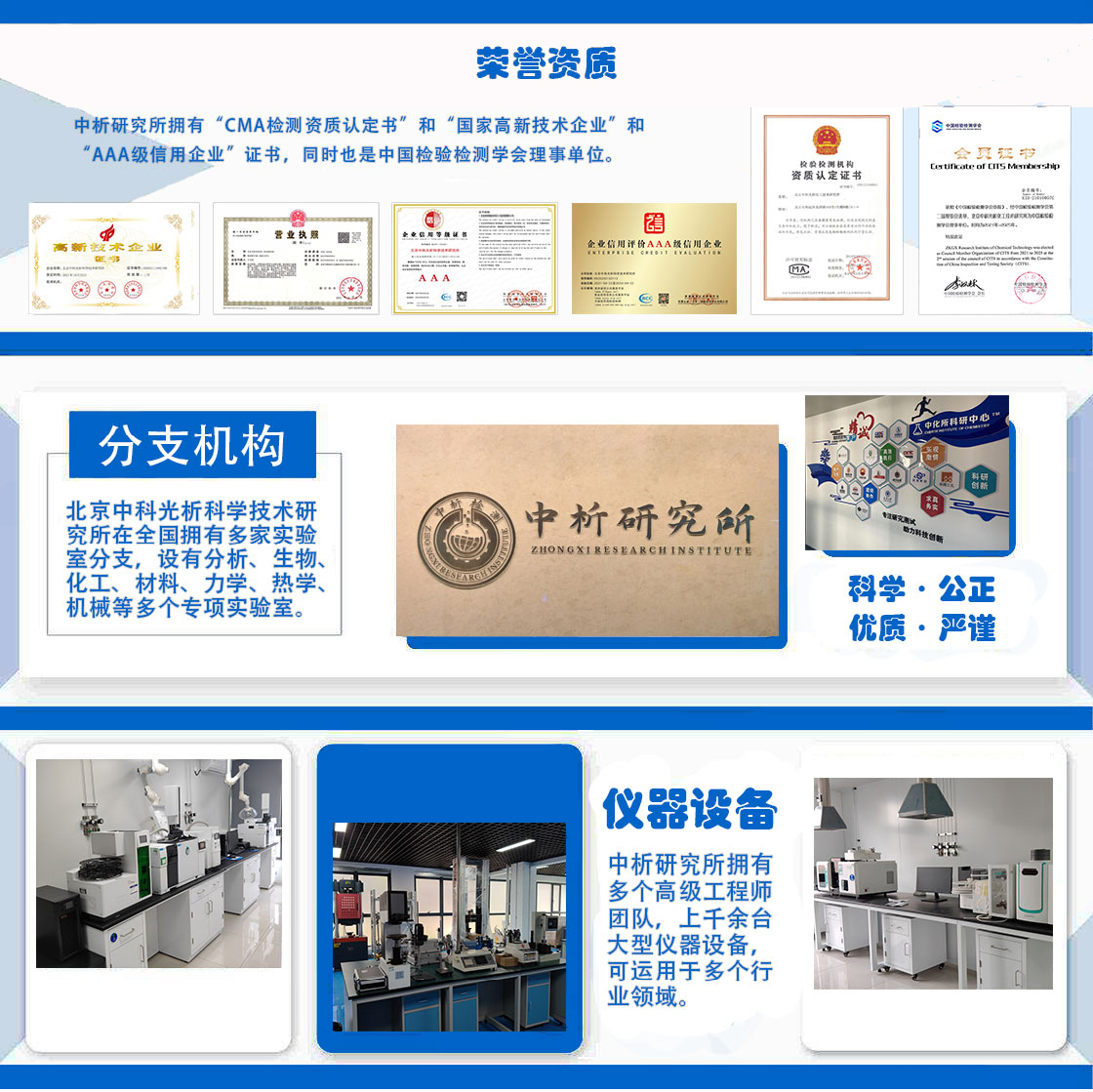
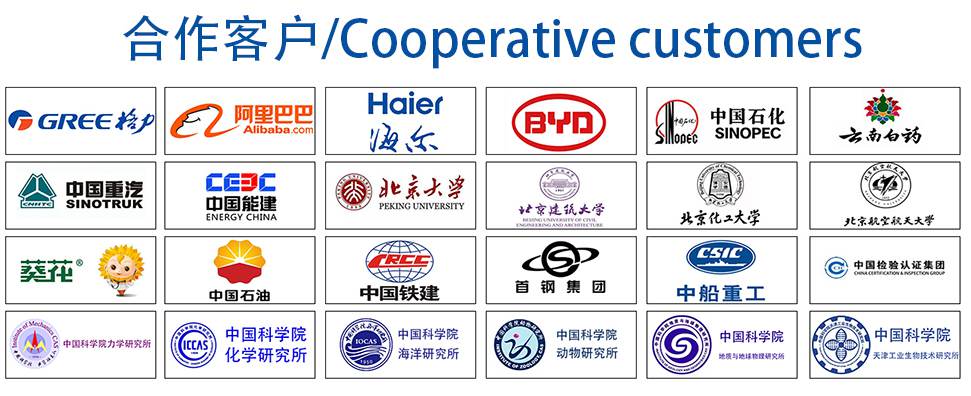