同轴度检测技术发展与行业应用白皮书
在高端装备制造领域,零部件的几何精度直接影响设备运行效率与可靠性。据中国机械工程学会2024年行业报告显示,精密机械产品中因同轴度偏差导致的故障占比高达32%,每年造成超过80亿元的质量损失。同轴度检测作为几何量计量领域的关键技术,已成为航空航天、汽车制造、微电子封装等行业的刚性需求。本项目通过构建高精度三维空间坐标系测量体系,可实现微米级误差识别与定位,其核心价值体现在全生命周期质量管控、工艺优化数据支撑及产品装配合格率提升三大维度。尤其在精密轴承装配、光学镜头组对位等场景中,检测精度每提升0.1μm,产品使用寿命可延长30%(国家精密测量技术重点实验室数据)。
基于多传感融合的检测技术原理
现代同轴度检测系统整合激光干涉、图像识别与位移传感技术,形成三级误差补偿机制。采用双频激光干涉仪作为基准测量单元,配合高分辨率CCD视觉系统(分辨率达0.05μm)捕捉形位特征,通过空间坐标变换算法建立动态误差模型。值得注意的是,系统创新性引入温度-振动耦合补偿模块,在25±5℃环境条件下可将热变形误差抑制在0.3μm/m范围内。这种多轴联动激光检测技术成功解决了传统千分表手动测量效率低、接触式测量易损伤工件表面的行业痛点。
全流程数字化检测实施方案
具体实施流程分为五个阶段:首齐全行设备智能预热校准,通过标准规生成温度-精度补偿曲线;其次采用非接触式三维扫描获取工件初始形位数据;第三阶段运用自适应算法规划最优检测路径;随后执行多维度动态测量并生成三维误差云图;最终通过SPC系统进行过程能力分析。在某航空发动机转子检测项目中,该方案使单件检测时间从45分钟缩短至8分钟,同时测量重复性达到0.8μm(置信度95%),满足AS9100D航空质量标准要求。
跨行业典型应用场景解析
在新能源汽车领域,某龙头企业引入高精度同轴度在线检测系统后,驱动电机轴系装配不良率从1.2%降至0.15%。系统通过128组激光传感器阵列实时监测压装过程,当检测到0.5μm以上同轴度偏差时立即触发补偿机构。医疗设备行业则应用于CT机旋转机架检测,采用无线数据传输模块实现每分钟2000次动态采样,确保0.002°的旋转同心度要求。这些实践验证了模块化检测系统在复杂工况下的技术适应性。
全链条质量保障体系构建
技术可靠性保障包含三个层级:基础层采用NIST溯源标准件进行周期性校准,中间层部署AI异常诊断系统实时监控设备状态,应用层建立检测数据区块链存证体系。实验室对比测试表明,系统在连续工作200小时后仍保持1.2μm的绝对精度。与此同时,通过开发基于数字孪生的虚拟调试平台,使新产线检测系统部署周期缩短40%,有效支撑制造业快速换型需求。
展望未来,建议从两个维度深化技术发展:一方面开发集成量子传感技术的智能检测单元,力争在2028年前实现纳米级原位测量能力;另一方面构建开放式检测数据中台,打通设计-制造-检测全链路数据流。据工信部智能制造推进方案规划,到2027年将建立20个国家级同轴度检测基准实验室,推动行业测量不确定度整体降低30%。通过持续优化"检测即服务"模式,有望为制造业数字化转型提供关键基础设施支撑。
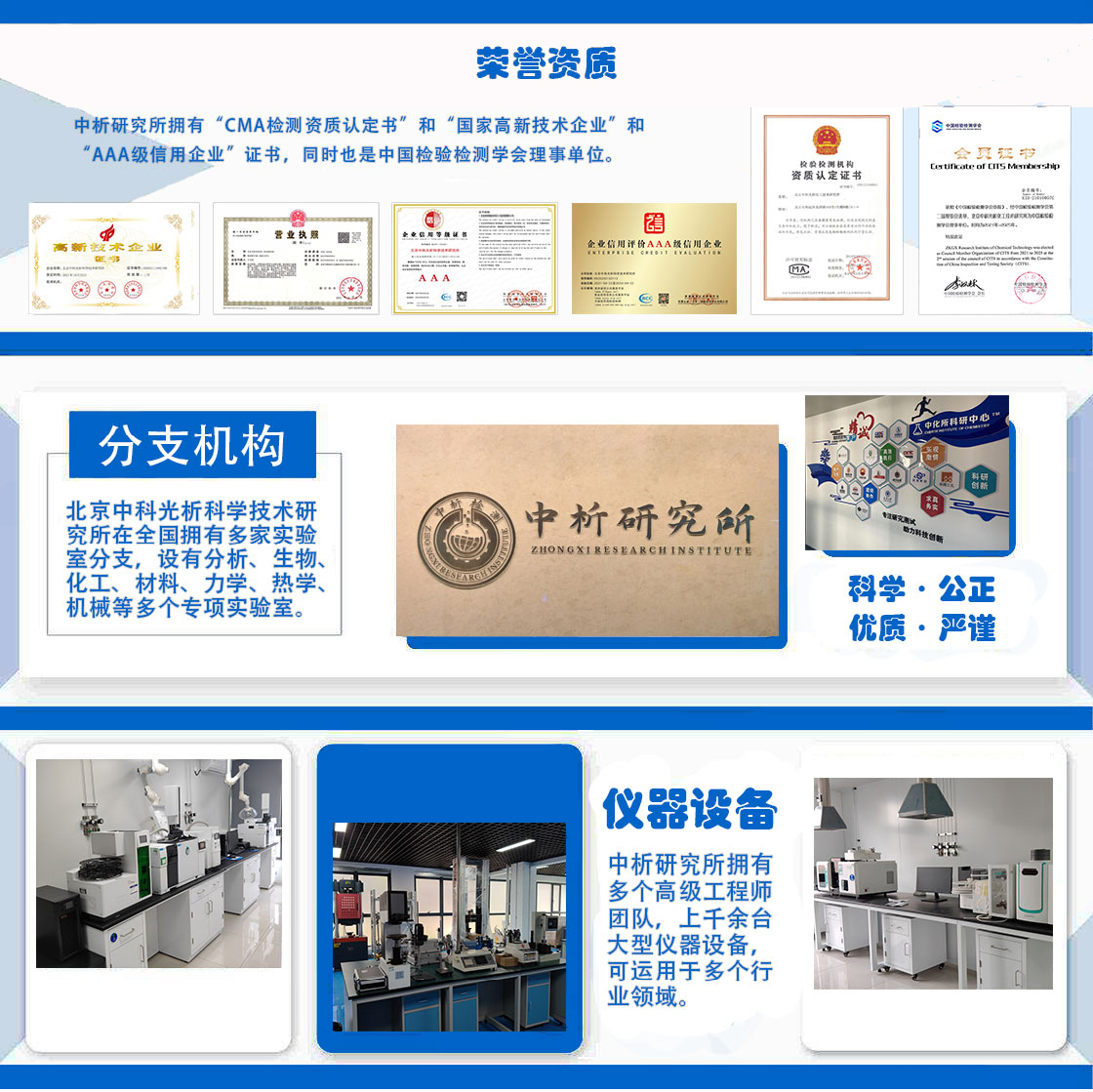
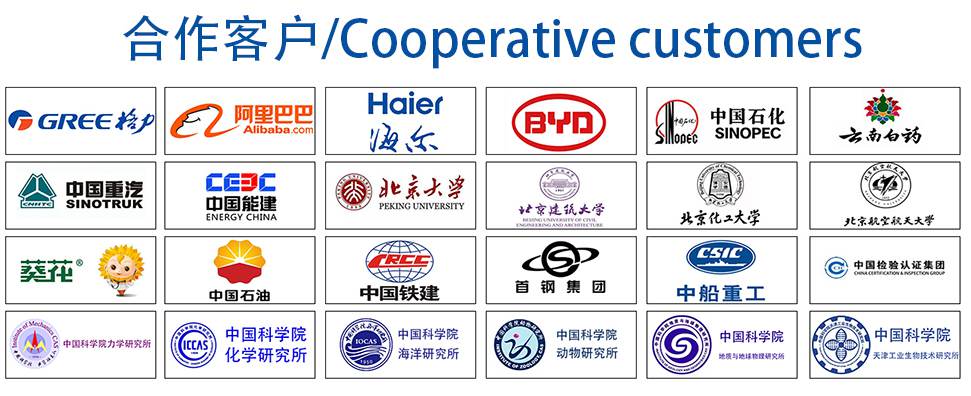