金属及非金属制品检测:核心项目与技术解析
一、金属制品检测项目
1. 成分分析
- 目的:确定金属材料的元素组成及占比。
- 主要方法:
- 光谱分析(OES、ICP-OES):快速检测合金元素含量。
- 化学滴定法:测定特定元素(如碳、硫)的精确含量。
- X射线荧光光谱(XRF):无损检测表面成分。
- 典型标准:ISO 14707(光谱分析)、GB/T 223(化学分析法)。
2. 力学性能检测
- 拉伸试验:测定抗拉强度、屈服强度、延伸率(依据GB/T 228.1或ASTM E8)。
- 硬度测试:布氏硬度(HB)、洛氏硬度(HRC)、维氏硬度(HV)。
- 冲击韧性:评估材料抗冲击能力(如夏比冲击试验,参考ASTM E23)。
- 疲劳测试:模拟循环载荷下材料的寿命(如ISO 1099)。
3. 缺陷检测
- 无损检测(NDT):
- 超声波检测(UT):探测内部裂纹、气孔。
- 射线检测(RT):X射线或γ射线透视内部结构。
- 磁粉检测(MT):表面及近表面裂纹检测(铁磁性材料)。
- 渗透检测(PT):非金属表面开口缺陷识别。
- 金相分析:观察微观组织(晶粒度、夹杂物等)。
4. 耐腐蚀性测试
- 盐雾试验:模拟海洋大气腐蚀(GB/T 10125)。
- 电化学测试:极化曲线、阻抗谱分析。
- 应力腐蚀试验:评估材料在腐蚀介质中的抗开裂性能。
二、非金属制品检测项目
1. 材料鉴定
- 成分分析:
- 红外光谱(FTIR):识别高分子材料基体。
- 热重分析(TGA):测定材料热稳定性及添加剂含量。
- 气相色谱-质谱联用(GC-MS):分析有机物成分。
2. 物理性能测试
- 密度与孔隙率:阿基米德法或气体置换法。
- 热性能:
- 热变形温度(HDT,ISO 75)。
- 导热系数(ASTM C177)。
- 电性能:介电强度、体积电阻率(IEC 60243)。
3. 力学与耐久性测试
- 拉伸/压缩强度:塑料、橡胶的载荷承受能力(GB/T 1040)。
- 弯曲强度:陶瓷、复合材料的抗弯性能(ISO 178)。
- 老化试验:
- 紫外老化(ASTM G154):模拟日光辐射。
- 湿热老化(GB/T 2423.3):评估湿热环境下的性能变化。
4. 安全性与环保检测
- 毒性检测:重金属(如铅、镉)、塑化剂(邻苯二甲酸酯)含量(符合RoHS、REACH法规)。
- 阻燃性能:垂直燃烧试验(UL94)、氧指数测试(ASTM D2863)。
- 环保指标:VOC释放量(GB 18583)、可降解性测试。
三、检测标准与规范
- 国际标准:ISO、ASTM、EN、IEC等。
- 国内标准:GB(国标)、HB(航空标准)、JG(建筑工业标准)。
- 行业特定标准:如汽车行业ISO/TS 16949、医疗器械ISO 13485。
四、检测技术发展趋势
- 智能化与自动化:AI图像识别缺陷、机器人自动采样。
- 无损检测技术升级:太赫兹成像、激光超声检测。
- 微观尺度分析:扫描电镜(SEM)与能谱联用(EDS)的精细化检测。
- 绿色检测方法:低毒试剂替代、能耗优化技术。
五、典型应用场景
- 制造业:汽车零部件强度验证、电子产品材料失效分析。
- 建筑工程:钢筋力学性能测试、混凝土非金属骨料耐久性评估。
- 消费品:玩具材料毒性筛查、食品包装迁移物检测。
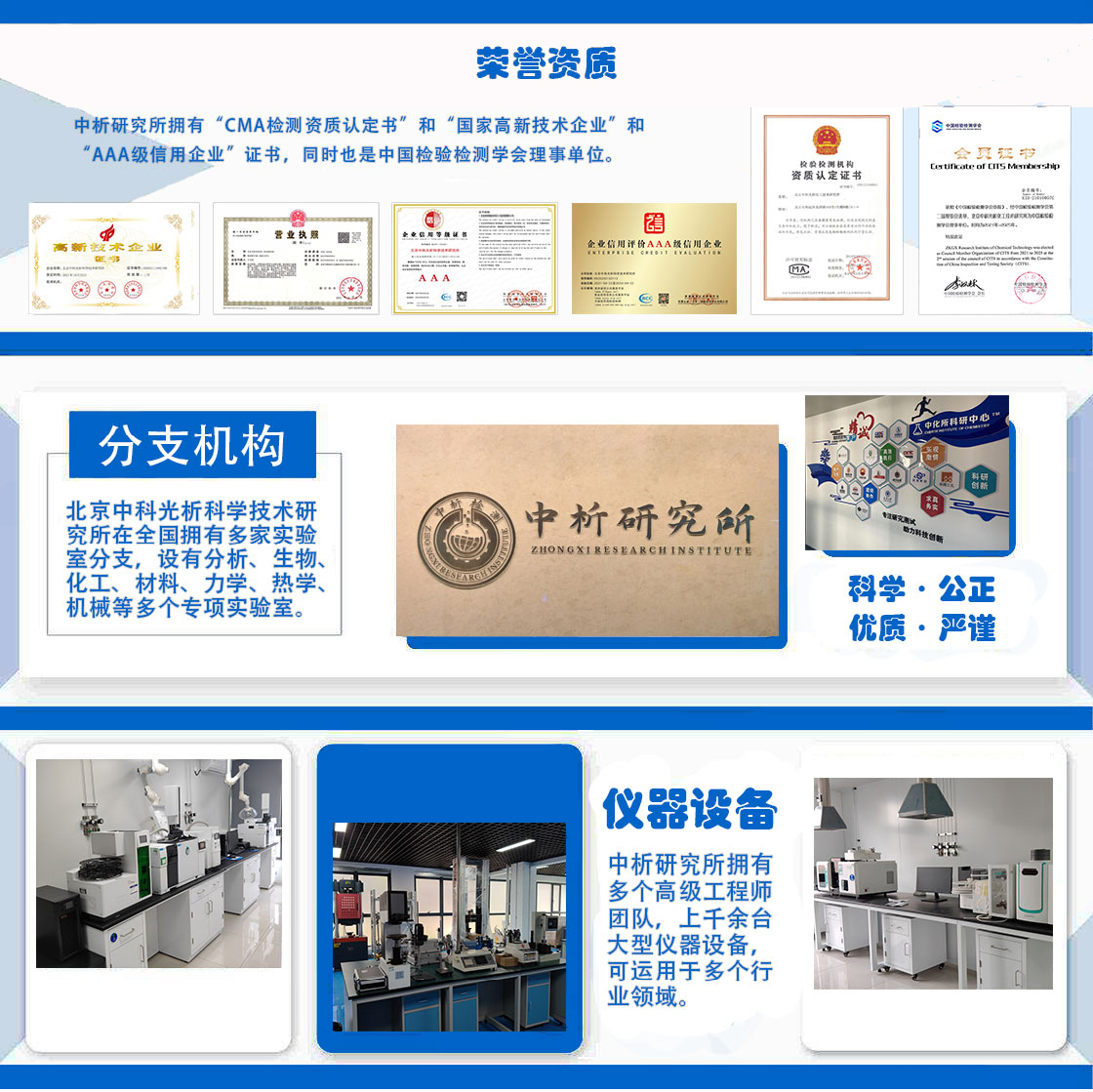
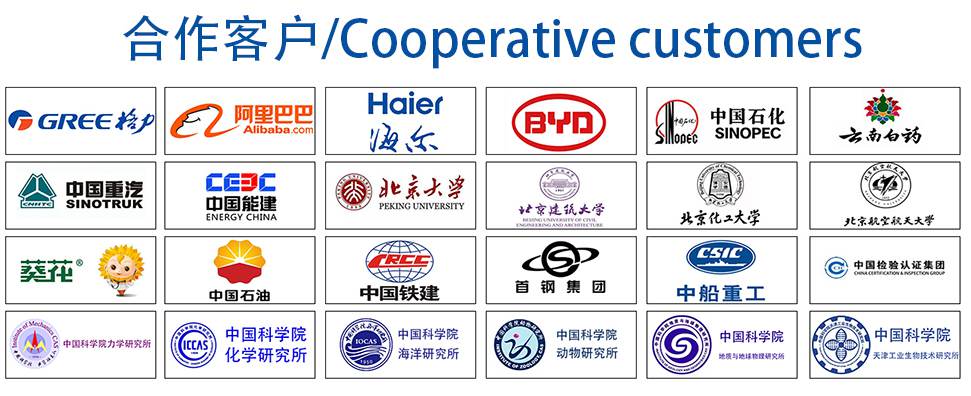
材料实验室
热门检测
276
233
208
217
215
221
230
223
234
233
220
219
222
219
214
210
227
212
224
218
推荐检测
联系电话
400-635-0567