一、材料基础性能检测
-
- 测试方法:热重分析(TGA)、差示扫描量热法(DSC)
- 目的:测定材料在高温下的分解温度、玻璃化转变温度(Tg)、熔融温度及热稳定性。
- 应用:高分子材料(如塑料、橡胶)的耐温极限评估。
-
- 测试方法:热机械分析仪(TMA)
- 目的:测量材料受热后的线性膨胀率,避免高温下因膨胀差异导致的结构失效。
- 应用:金属焊接件、陶瓷基复合材料的热匹配性验证。
二、力学性能检测
-
- 测试方法:高温万能试验机(配备加热炉)
- 目的:测定材料在高温下的抗拉强度、屈服强度、弹性模量等参数。
- 标准参考:ASTM E21(金属)、ISO 527(塑料)。
-
- 测试方法:恒温恒载蠕变试验机
- 目的:评估材料在高温长期载荷下的变形累积和应力衰减特性。
- 应用:燃气轮机叶片、高温管道的耐久性设计。
三、化学与环境耐受性检测
-
- 测试方法:高温氧化增重实验、盐雾试验(模拟高温腐蚀)
- 目的:分析材料表面氧化层形成速率及耐腐蚀能力。
- 案例:航空发动机涂层、化工反应釜内衬材料筛选。
-
- 测试方法:气相色谱-质谱联用(GC-MS)
- 目的:检测高温下材料释放的气体成分,避免污染或毒性风险。
- 应用:汽车内饰材料、电子封装材料的安全性评估。
四、物理与功能特性检测
-
- 测试方法:激光闪射法(LFA)、热线法
- 目的:评估材料导热性能,优化散热设计。
- 应用:半导体散热基板、隔热涂层开发。
-
- 测试项目:绝缘电阻、介电强度、介质损耗
- 设备:高温介电测试系统
- 应用:高压电缆、高温电子元件的可靠性验证。
五、特殊应用场景检测
-
- 方法:循环加载结合高温环境模拟
- 目的:模拟材料在交变温度与应力下的疲劳寿命。
- 案例:航空发动机叶片、核电阀门部件的寿命预测。
-
- 测试内容:高温下密封材料的泄漏率、压缩永久变形
- 设备:高温密封试验台
- 应用:石油管道密封圈、航天器舱门密封设计。
六、试验标准与设备选择
- 国际标准:ISO 6892(金属高温拉伸)、ASTM D638(塑料高温测试)、MIL-STD-810(军工设备环境试验)。
- 关键设备:
- 高温试验箱(温度范围可达1200℃以上)
- 红外热像仪(非接触式温度场监测)
- 高温应变测量系统(贴片式或光学应变计)
七、数据解读与失效分析
上一篇:包装跌落检测下一篇:金属及非金属制品检测
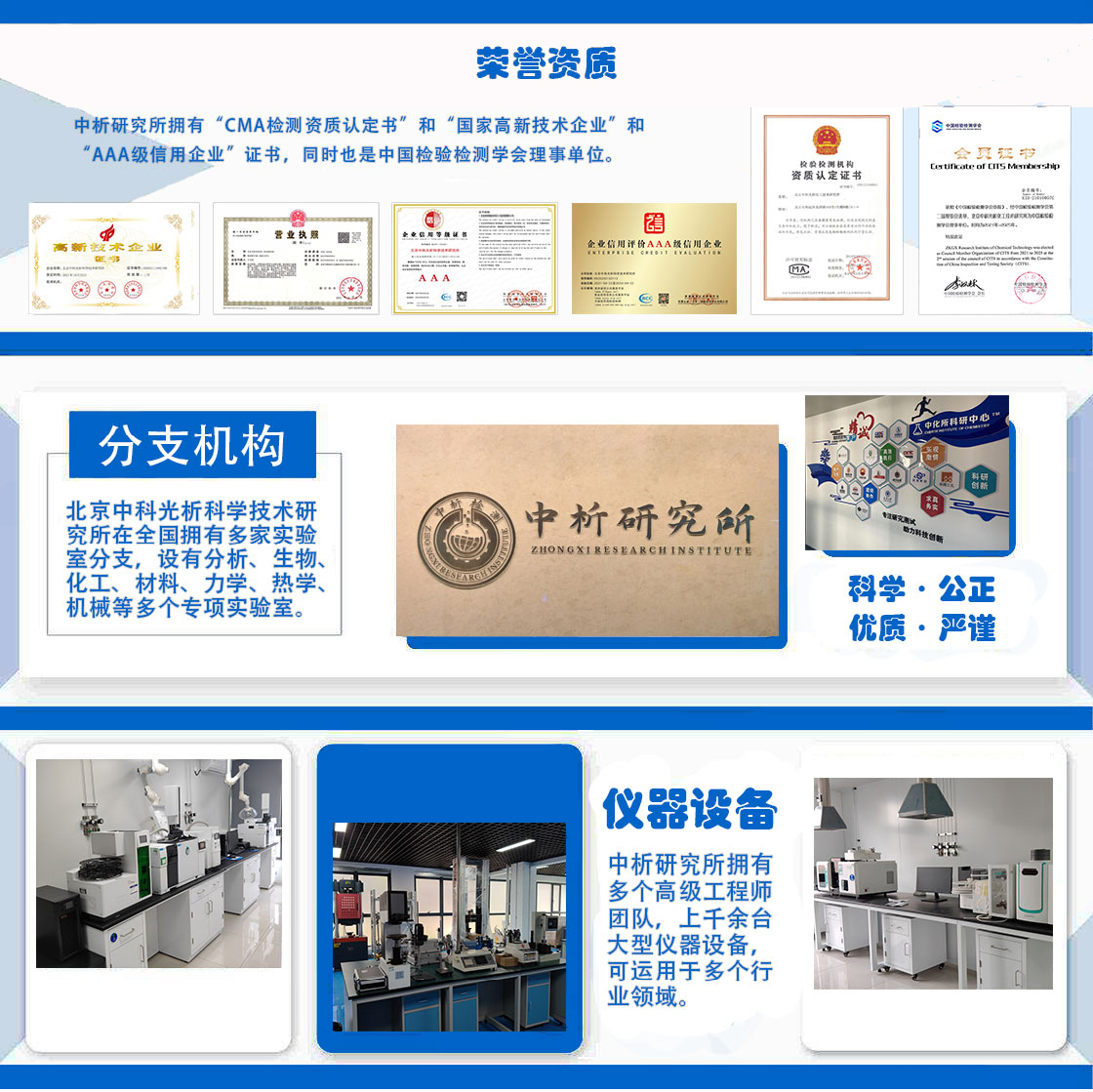
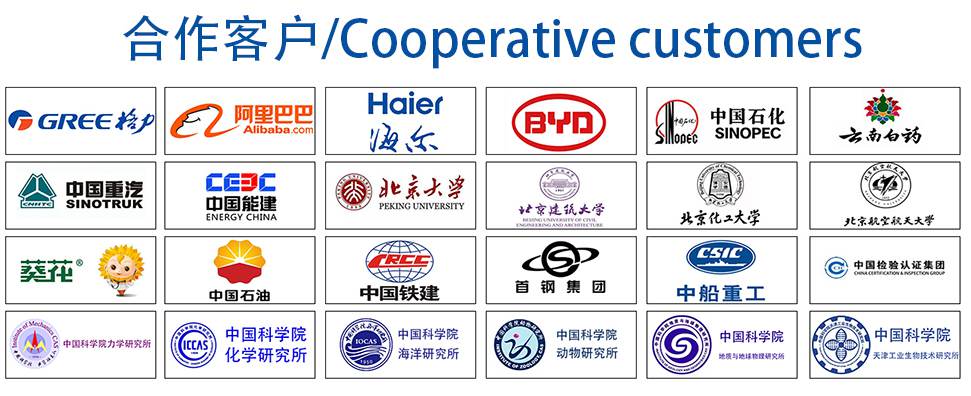
材料实验室
热门检测
276
233
208
217
215
221
230
223
234
233
220
220
223
219
214
210
227
212
224
218
推荐检测
联系电话
400-635-0567