金属钛检测的核心项目与技术要点
一、化学成分分析
1. 钛(Ti)含量检测
- 目的:主成分含量直接影响材料性能,纯度要求通常≥99.6%(工业级)。
- 方法:电感耦合等离子体原子发射光谱(ICP-AES)、X射线荧光光谱(XRF)。
- 标准:GB/T 3620.1、ASTM E2371。
2. 杂质元素检测
- 关键元素:铁(Fe)、碳(C)、氮(N)、氧(O)、氢(H)、铝(Al)、钒(V)等。
- 氢脆风险:氢含量需严格控制在50 ppm以下(如ASTM B348)。
- 检测技术:气体分析(氧/氮/氢测定)、火花直读光谱法。
二、物理性能检测
1. 密度测定
- 方法:阿基米德排水法,纯钛理论密度约4.506 g/cm³。
- 标准:GB/T 1423。
2. 热学性能
- 热膨胀系数:评估高温环境下的尺寸稳定性(如20-100℃范围)。
- 热导率:激光闪射法测定,钛合金热导率通常为7-12 W/(m·K)。
- 标准:ASTM E1461(热扩散率)。
三、机械性能测试
1. 拉伸性能
- 关键指标:抗拉强度(≥345 MPa,纯钛)、屈服强度、延伸率。
- 测试标准:GB/T 228.1、ASTM E8/E8M。
2. 硬度测试
- 方法:洛氏硬度(HRB/HRC)、布氏硬度(HBW)。
- 典型值:纯钛退火态硬度约120 HBW,钛合金可达350 HBW(如TC4)。
3. 冲击韧性
- 应用场景:低温环境用钛材需检测夏比冲击试验(-196℃液氮环境)。
- 标准:ASTM E23。
四、微观结构分析
1. 金相组织检测
- 观察内容:α相、β相分布形态,晶粒尺寸均匀性。
- 腐蚀剂:Kroll试剂(3% HF + 6% HNO3 + 91% H2O)。
- 标准:GB/T 5168。
2. 晶粒度评级
- 方法:比对法或截点法,ASTM E112。
- 影响:细晶粒可提升材料强度和韧性(Hall-Petch效应)。
五、表面与缺陷检测
1. 无损检测(NDT)
- 超声波检测:探测内部裂纹、夹杂(灵敏度达Φ0.8 mm平底孔)。
- 渗透检测:表面开口缺陷检查,符合ASTM E165。
- X射线探伤:检测气孔、缩孔等体积型缺陷。
2. 表面粗糙度
- 医用钛材要求:Ra≤0.8 μm(减少生物膜附着风险)。
- 仪器:接触式轮廓仪或白光干涉仪。
六、耐腐蚀性能测试
1. 盐雾试验
- 条件:5% NaCl溶液,35℃连续喷雾,评估72小时后的腐蚀速率。
- 标准:GB/T 10125。
2. 电化学测试
- 方法:动电位极化曲线法,测定点蚀电位(Eb)和维钝电流密度。
- 酸性环境模拟:10% HCl或H2SO4溶液中的耐蚀性评估。
七、高温性能专项检测
1. 高温拉伸试验
- 温度范围:300-600℃(典型钛合金工作温度)。
- 指标:高温屈服强度、蠕变极限。
2. 持久强度试验
- 测试条件:恒定高温+负载,记录断裂时间(如500℃/200 MPa)。
八、生物相容性检测(医用钛)
1. 细胞毒性试验
- 方法:MTT法检测浸提液对L929细胞的抑制率(ISO 10993-5)。
2. 离子析出检测
- 关注元素:铝、钒等合金元素的析出量(ICP-MS分析)。
检测流程标准化要点
- 取样规范:避开边缘效应区,按GB/T 2975确定取样位置。
- 数据判读:结合多指标交叉验证(如高氧含量可能导致脆性增加)。
- 报告内容:需涵盖检测方法、设备型号、标准依据及不确定度分析。
上一篇:金属及非金属制品检测下一篇:铜箔电阻检测
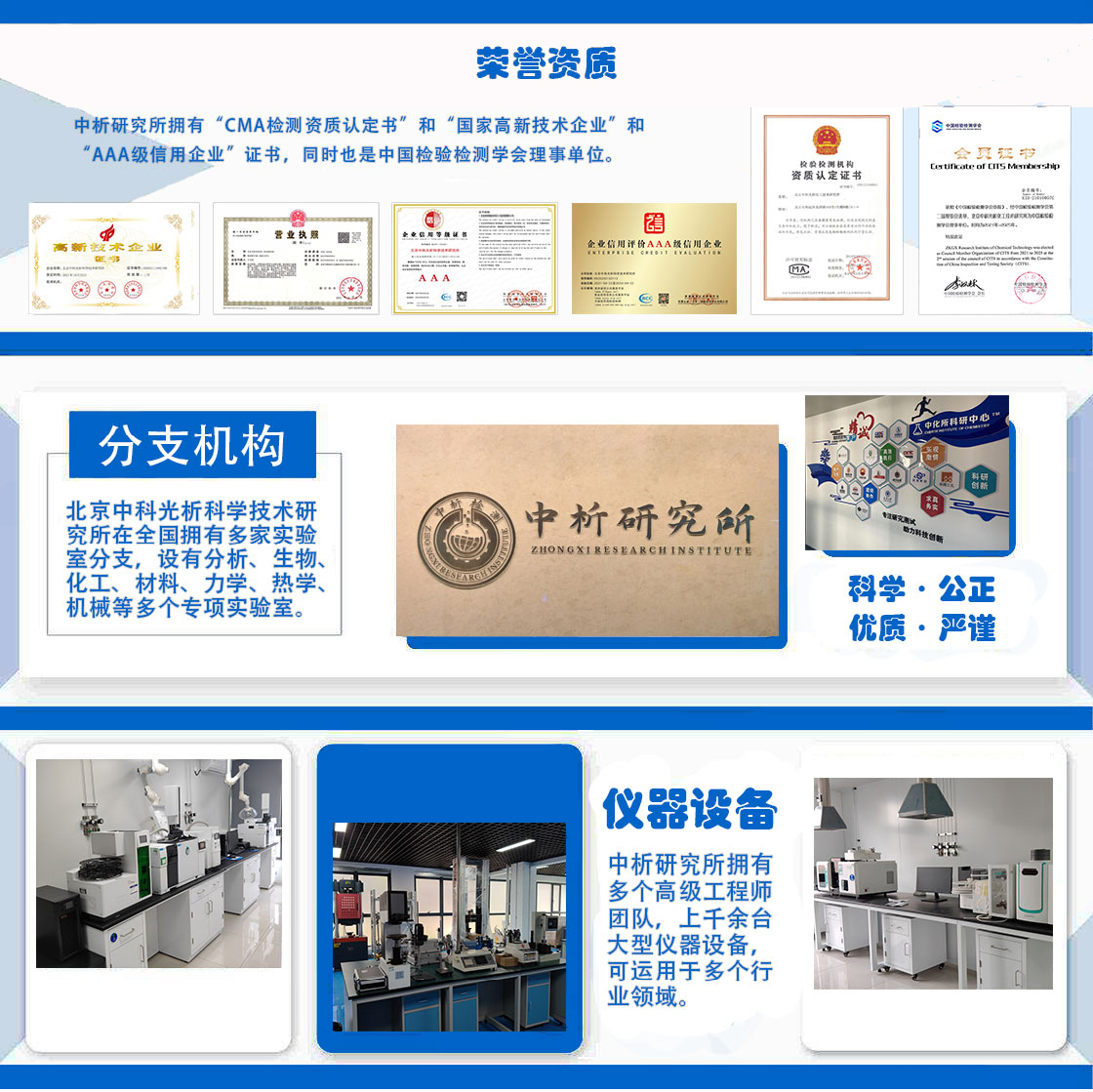
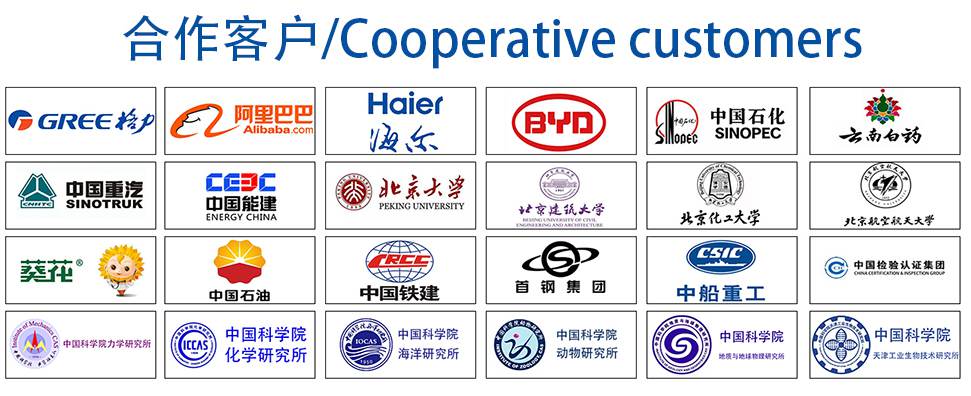
材料实验室
热门检测
276
233
208
217
215
220
230
223
233
233
220
219
222
219
213
210
227
212
224
218
推荐检测
联系电话
400-635-0567