燃气用埋地聚乙烯(PE)管件检测项目详解
一、物理性能检测
-
- 目的:测定PE材料的密度,判断原材料纯度及是否掺入回收料。
- 方法:采用浸渍法或密度梯度柱法,依据GB/T 1033标准。
- 标准要求:高密度聚乙烯(HDPE)密度范围通常为0.940~0.965 g/cm³。
-
- 目的:评估材料熔融流动特性,反映加工性能的一致性。
- 方法:按GB/T 3682测试,在190℃、5kg载荷下测定熔体流速。
- 判定标准:与原材料标称值偏差不超过±20%。
二、力学性能检测
-
- 目的:验证管件在长期内压下的抗爆破能力。
- 方法:
- 短期试验(20℃/1h):加压至公称压力的4.8倍,无破裂或渗漏。
- 长期试验(80℃/165h):加压至环应力4.0 MPa,评估抗蠕变性能。
- 判定依据:GB/T 6111标准。
-
- 目的:表征材料的延展性,避免脆性断裂风险。
- 方法:按GB/T 8804制样,拉伸速率50 mm/min,测定断裂时伸长率。
- 标准要求:≥350%(适用于PE100级材料)。
-
- 目的:评估管道在低应力、长期载荷下的抗裂纹扩展能力。
- 试验方法:
- 切口管试验(NPT):测试至破坏时间需>500 h(PE100)。
- 锥体试验(PNT):切口深度和裂纹扩展速率需符合标准。
三、耐环境性能检测
-
- 目的:模拟长期光照环境对材料性能的影响。
- 方法:按GB/T 16422.3进行氙灯加速老化,累计辐照量达3.5 GJ/m²后测试力学性能保留率。
- 要求:拉伸强度与断裂伸长率下降不超过20%。
-
- 目的:验证管件在土壤中酸、碱、盐等介质中的稳定性。
- 方法:将试样浸泡于模拟腐蚀液(如pH=2~12溶液),观察90天后质量变化及表面状态。
- 判定:质量变化率≤0.5%,无气泡、龟裂现象。
-
- 方法:采用楔形试样或全缺口蠕变试验(FNCT),在表面活性剂(如Igepal)环境中加压测试。
- 标准:PE100级材料FNCT试验时间应>1000 h。
四、尺寸与外观检测
-
- 检测项:
- 壁厚偏差:±5%(GB 15558.2)。
- 管件内/外径椭圆度:≤2%。
- 工具:数显游标卡尺、壁厚测厚仪、三维测量仪。
- 检测项:
-
- 要求:
- 表面光滑,无气泡、杂质、裂纹、凹陷等缺陷。
- 电熔管件的电阻丝排列均匀,无裸露或错位。
- 要求:
五、化学成分及添加剂分析
-
- 项目:碳黑含量(2.0~2.5%)、抗氧化剂(如Irganox 1010)含量。
- 方法:热重分析(TGA)、红外光谱(FTIR)比对。
-
- 判定:显微镜观察炭黑颗粒分布,不允许存在团聚或条纹。
六、长期性能评估
- 长期静液压试验(LTHS)
- 目的:预测管件50年使用寿命的可靠性。
- 条件:80℃下环应力4.6 MPa,持续≥8760小时(PE100)。
- 判定:无破裂、无渗漏,且斜率法外推结果满足要求。
七、现场安装质量检测
-
- 项目:
- 焊接参数(电压、时间、冷却时间)合规性。
- 接头剖视检查:电阻丝无位移,熔合面无孔洞。
- 设备:超声波检测仪、X射线成像。
- 项目:
-
- 方法:采用示踪线、金属探测器或探地雷达(GPR)定位埋深;气密性试验(0.4 MPa保压24小时,压降≤1%)。
检测依据与标准
- 国内标准:GB 15558.1、GB/T 13663、CJJ 63-2018(城镇燃气管道施工规范)。
- 国际标准:ISO 4437、EN 1555。
结语
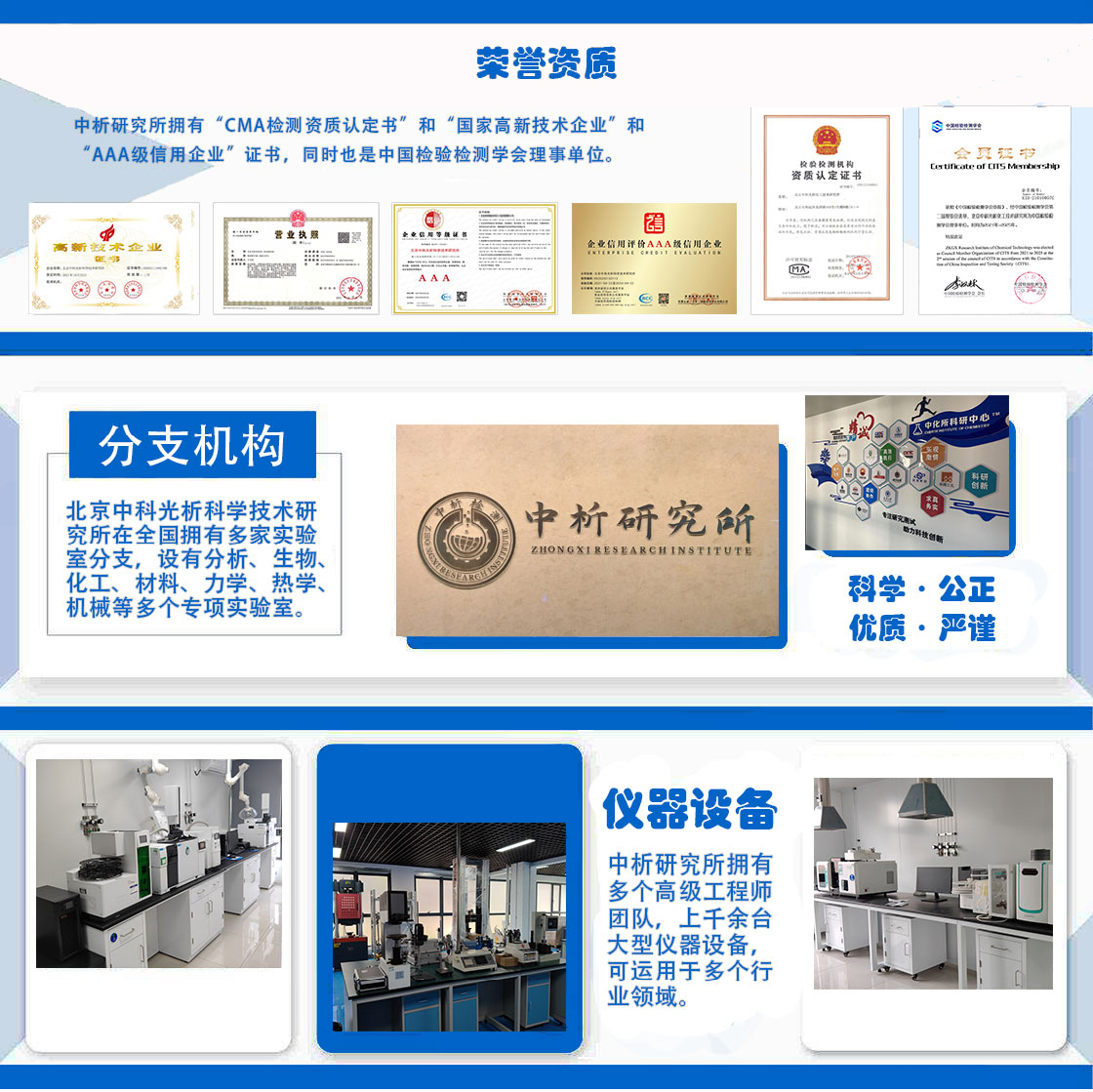
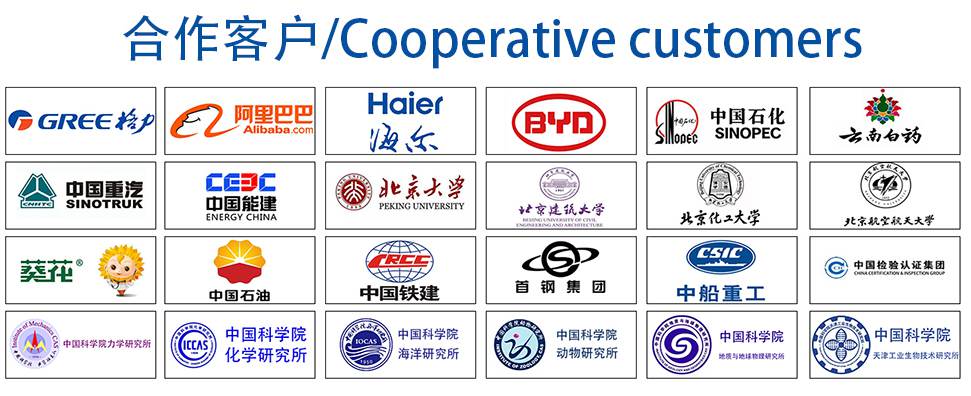
材料实验室
热门检测
251
211
187
201
194
200
206
199
205
212
200
195
192
198
193
189
204
195
204
199
推荐检测
联系电话
400-635-0567