带导线设备耐锡焊热与可焊性试验方法及检测项目详解
一、试验目的
二、耐锡焊热试验
1. 试验流程
- 预处理:试样在25±5℃/50%RH环境下放置24小时。
- 浸焊条件:
- 焊料槽温度:260±5℃(无铅焊料)或235±5℃(有铅焊料)
- 浸入时间:5±0.5秒(参考IEC 60068-2-20标准)
- 浸渍深度:导线端部至本体距离的75%以上。
- 冷却:自然冷却至室温,避免震动。
2. 检测项目
-
- 检测内容:本体开裂、封装变形、导线氧化变色。
- 判定标准:无肉眼可见损伤,允许轻微变色(如发黄)。
-
- 参数:绝缘电阻(≥100MΩ)、耐压强度(按器件规格1.5倍测试)。
- 方法:试验前后对比,变化率≤10%。
-
- 夹具法:对导线施加轴向拉力(如1N/mm²),持续10秒无脱落。
- 弯曲试验:导线弯折90°三次,焊点无开裂。
三、可焊性试验
1. 润湿性测试
-
- 设备:可焊性测试仪(如SAT-5100)。
- 过程:记录试样浸入焊料时润湿力随时间变化曲线。
- 关键参数:润湿时间(≤1秒)、最大润湿力(≥理论值的80%)。
-
- 方法:在铜板上滴定量焊料,放置试样后加热至230℃。
- 判定:焊料扩展面积≥80%为合格(JIS Z 3197标准)。
2. 焊点质量评估
-
- 理想焊点:表面光滑、呈凹面状,无针孔、虚焊。
- 缺陷判定:焊料覆盖不足(<75%)、明显空洞或裂纹。
-
- 金相切片:观察界面IMC(金属间化合物)厚度(1-5μm为优)。
- 检测设备:SEM/EDS分析元素扩散情况。
3. 加速老化试验
- 蒸汽老化:试样在85℃/85%RH环境中放置8小时,模拟长期存储后氧化。
- 结果判断:老化后润湿性下降不超过初始值的20%。
四、特殊场景补充试验
-
- 执行3次浸焊循环,测试焊端结合力是否衰减。
- 应用场景:返修工艺验证。
-
- 设定焊料温度200℃(用于热敏感元件),检查润湿效果。
-
- 测试不同活性等级助焊剂(如ROL0/ROL1)对焊点可靠性的影响。
五、判定标准依据
- 国际标准:IEC 61190(电子组装材料要求)、IPC J-STD-002(元件可焊性)。
- 国内标准:GB/T 2423.28(耐焊热)、GB/T 2423.32(可焊性)。
六、常见失效模式及对策
- 不润湿:检查镀层氧化(建议增加镀层厚度≥3μm)。
- 焊点脆裂:优化冷却速率或改用韧性焊料(如Sn-Ag-Cu-Ti)。
上一篇:燃气用埋地聚乙烯(PE)管件检测下一篇:气候顺序检测
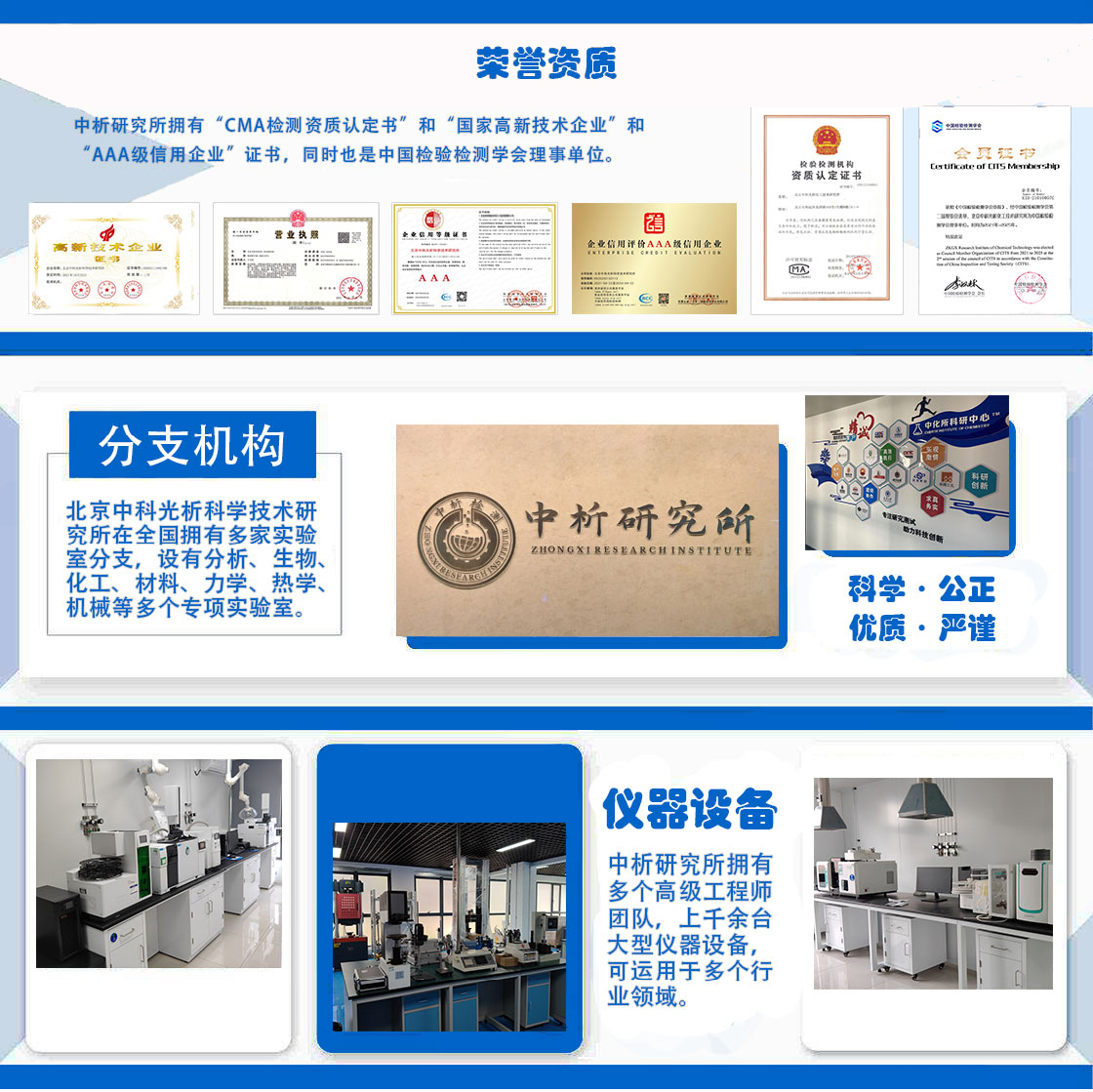
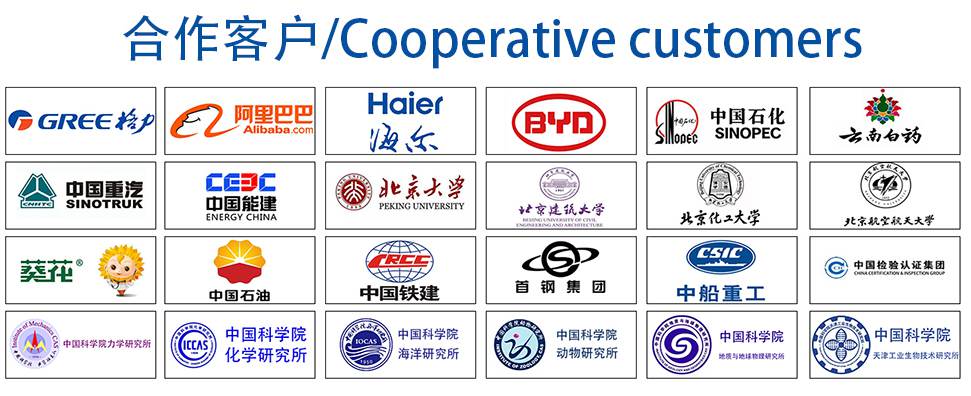
材料实验室
热门检测
251
211
187
201
193
199
206
198
204
211
200
195
192
198
193
189
203
195
204
199
推荐检测
联系电话
400-635-0567