锁紧装置机械操作检测项目详解
一、功能性检测
-
- 检测内容:验证锁紧装置在正常工况下的锁定和解锁动作是否顺畅。
- 方法:使用液压或电动测试台模拟实际负载,记录操作所需力矩及位移。
- 标准:依据ISO 12100或行业规范(如汽车行业ISO 26262)。
-
- 检测内容:测量锁紧装置在锁定状态下能承受的最大静态力和动态冲击力。
- 工具:万能材料试验机、动态力传感器。
- 判定标准:锁定力需高于设计要求值的1.5倍(参考GB/T 3811)。
-
- 检测内容:检查解锁后装置是否能自动复位至初始位置。
- 失效模式:卡滞、偏移或复位不完全需判定为不合格。
二、耐久性及寿命测试
-
- 检测内容:模拟装置在设定周期内的重复锁定/解锁操作。
- 参数:记录失效前的循环次数、磨损程度(如接触面形变)。
- 设备:高频疲劳试验机,设定频率通常为10-30次/分钟。
-
- 环境模拟:高温(70℃以上)、低温(-40℃)、湿度(RH 95%)等极端条件。
- 评估指标:材料膨胀/收缩率变化、润滑剂性能衰减。
三、安全性评估
-
- 测试内容:施加超出设计载荷的压力,验证锁紧装置是否触发安全保护(如自锁或警报)。
- 典型场景:起重机吊钩防脱落装置需在超载时自动锁死。
-
- 模拟场景:人为施加错误操作(如反向旋转、强行解锁)。
- 要求:装置应避免因误操作导致结构损坏或功能失效。
四、环境适应性检测
-
- 标准:依据IEC 60068-2-6(振动)及MIL-STD-810G(冲击)。
- 结果分析:检查紧固件松动、异响或变形。
-
- 盐雾测试:按ASTM B117标准进行48-96小时盐雾试验。
- 密封性评估:浸水或气压测试(防水等级IP67以上需通过1米水深30分钟测试)。
五、关键零部件专项检测
-
- 使用显微硬度计检查表面硬化层深度(HV≥500)。
- 金相分析确保材料无内部缺陷(如气孔、夹杂物)。
-
- 检测弹性系数、疲劳寿命及抗松弛能力(参考DIN 2095)。
六、合规性与认证检测
- CE认证(欧盟):需通过EMC测试(电磁兼容)及机械指令2006/42/EC。
- UL认证(美国):防火性能及电气安全性评估(适用于电子锁紧装置)。
七、检测报告要求
- 数据记录:需包含原始检测数据、曲线图及视频记录(如失效瞬间捕捉)。
- 不合格项处理:明确返工方案(如表面再处理)、报废标准及风险预警级别。
上一篇:耐高压检测下一篇:显色指数(CRI)检测
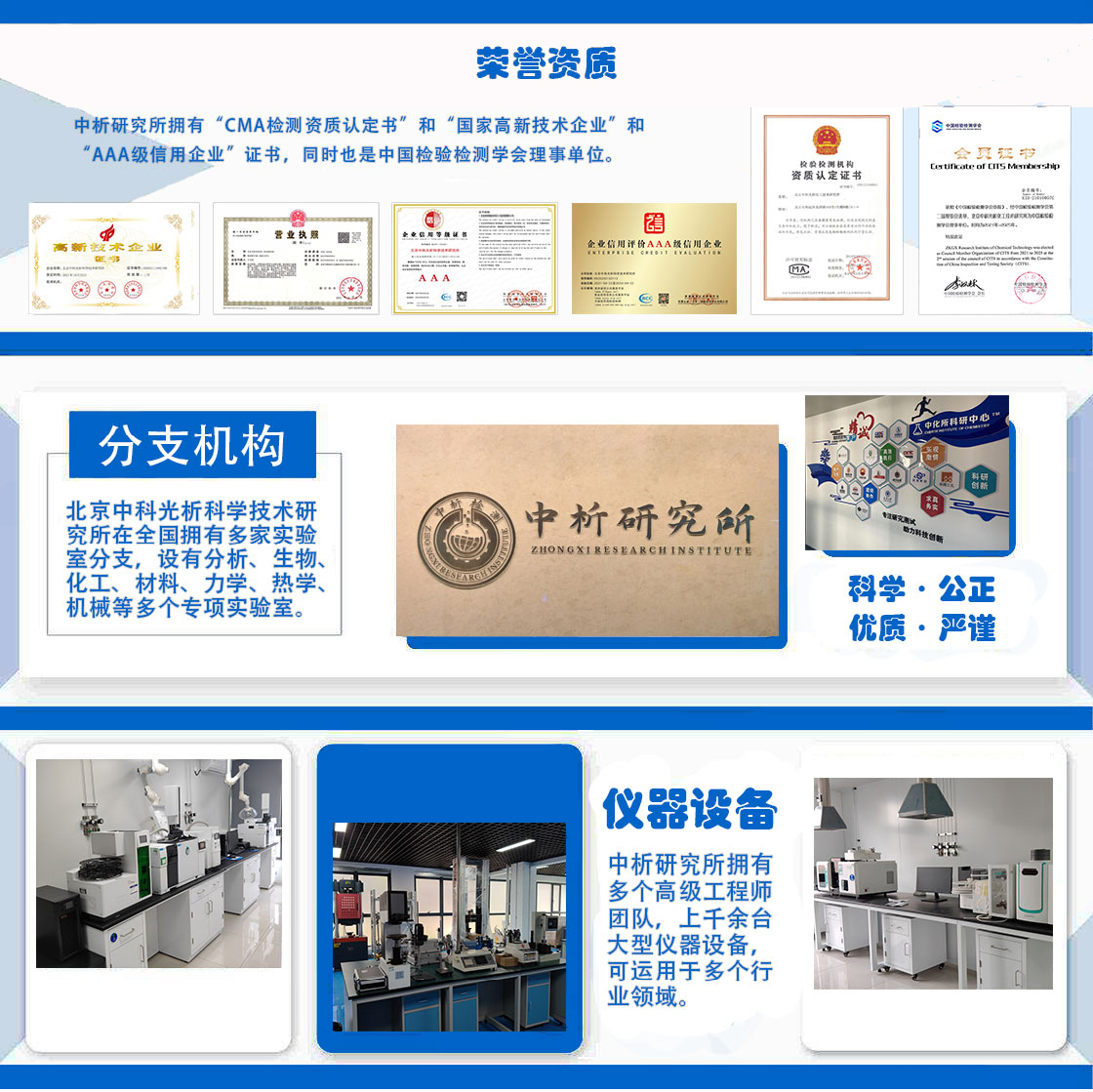
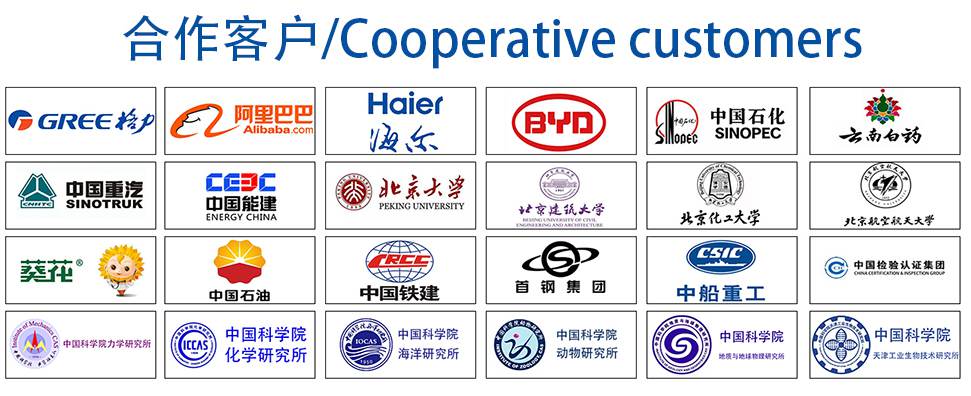
材料实验室
热门检测
254
215
190
203
197
204
210
202
207
217
204
199
204
203
198
195
210
199
209
202
推荐检测
联系电话
400-635-0567