耐高压检测:核心检测项目与方法解析
一、核心检测项目
1. 耐压强度测试(Dielectric Strength Test)
- 目的:验证被测物在高电压下是否发生击穿或闪络。
- 方法: 施加高于正常工作电压的测试电压(如额定电压的2倍+1000V),持续1分钟,观察是否出现击穿、漏电流超标或局部放电现象。
- 应用场景: 电力变压器、电缆、绝缘子、电容器等电气设备。
2. 绝缘电阻测试(Insulation Resistance Test)
- 目的:评估绝缘材料阻止电流泄漏的能力。
- 方法: 使用兆欧表(500V/1000V直流电压)测量导体与绝缘层之间的电阻,电阻值需符合行业标准(如≥100MΩ)。
- 关键参数: 温度、湿度对绝缘电阻影响显著,需在标准环境(如23±2℃、50%RH)下测试。
3. 泄漏电流测试(Leakage Current Test)
- 目的:检测设备在高压下因绝缘缺陷导致的微小电流泄漏。
- 方法: 施加额定工作电压,通过高精度电流表测量泄漏电流值,判断是否超出安全阈值(如≤0.5mA)。
- 典型应用: 家用电器、医疗设备的电气安全认证。
4. 局部放电检测(Partial Discharge, PD Test)
- 目的:识别绝缘材料内部微小放电现象,预防潜在故障。
- 方法: 使用高频电流传感器或超声波探测器,捕捉局部放电产生的电磁波或声波信号。
- 分析指标: 放电量(pC)、放电频率及分布位置。
5. 机械强度与形变测试
- 目的:评估高压环境下材料或结构的抗形变能力。
- 方法:
- 静态压力测试:持续施加高压(如液压测试),观察是否破裂或永久变形。
- 循环压力测试:模拟压力波动(如10,000次循环),检测疲劳寿命。
- 适用对象: 高压管道、密封件、压力容器。
6. 环境适应性测试
- 目的:验证高压设备在极端环境(高温、低温、潮湿)下的性能稳定性。
- 测试项目:
- 高温高压联合测试(如85℃/95%RH环境下加压至1.5倍额定电压)。
- 低温耐压测试(如-40℃下验证材料脆化风险)。
7. 老化寿命评估
- 目的:预测材料在长期高压下的性能退化趋势。
- 方法: 通过加速老化试验(如湿热老化、电老化),推算实际使用寿命。
二、检测设备与标准
1. 常用设备
- 高压发生器:输出交流(AC)、直流(DC)或脉冲高压。
- 局部放电检测仪:如PD-checker、OLPD在线监测系统。
- 绝缘电阻测试仪:如Megger、Hioki系列。
- 压力试验机:液压或气压加压系统。
2. 主要参考标准
- 国际标准:
- IEC 60243(固体绝缘材料耐压试验)
- IEC 60601(医疗电气设备安全)
- ASTM D149(介电强度测试)
- 国内标准:
- GB/T 1695(硫化橡胶耐电压测定方法)
- GB 4706(家用电器安全规范)
三、检测意义与行业应用
- 电力行业:确保变压器、断路器等设备在电网冲击下安全运行。
- 汽车电子:验证电动车高压电池包、充电桩的绝缘性能。
- 航空航天:液压管路、密封舱体的耐压可靠性验证。
- 新能源领域:光伏逆变器、储能系统的耐高压认证。
四、常见问题与解决方案
问题 | 原因分析 | 解决方案 |
---|---|---|
绝缘击穿 | 材料缺陷或污染 | 更换高等级绝缘材料 |
泄漏电流超标 | 绝缘老化或设计缺陷 | 优化电路布局,加强绝缘 |
局部放电持续发生 | 内部气隙或杂质 | 真空浸渍处理或重新封装 |
机械形变量过大 | 结构强度不足 | 增加支撑结构或更换材料 |
结语
上一篇:外观检验和尺寸检查检测下一篇:锁紧装置机械操作检测
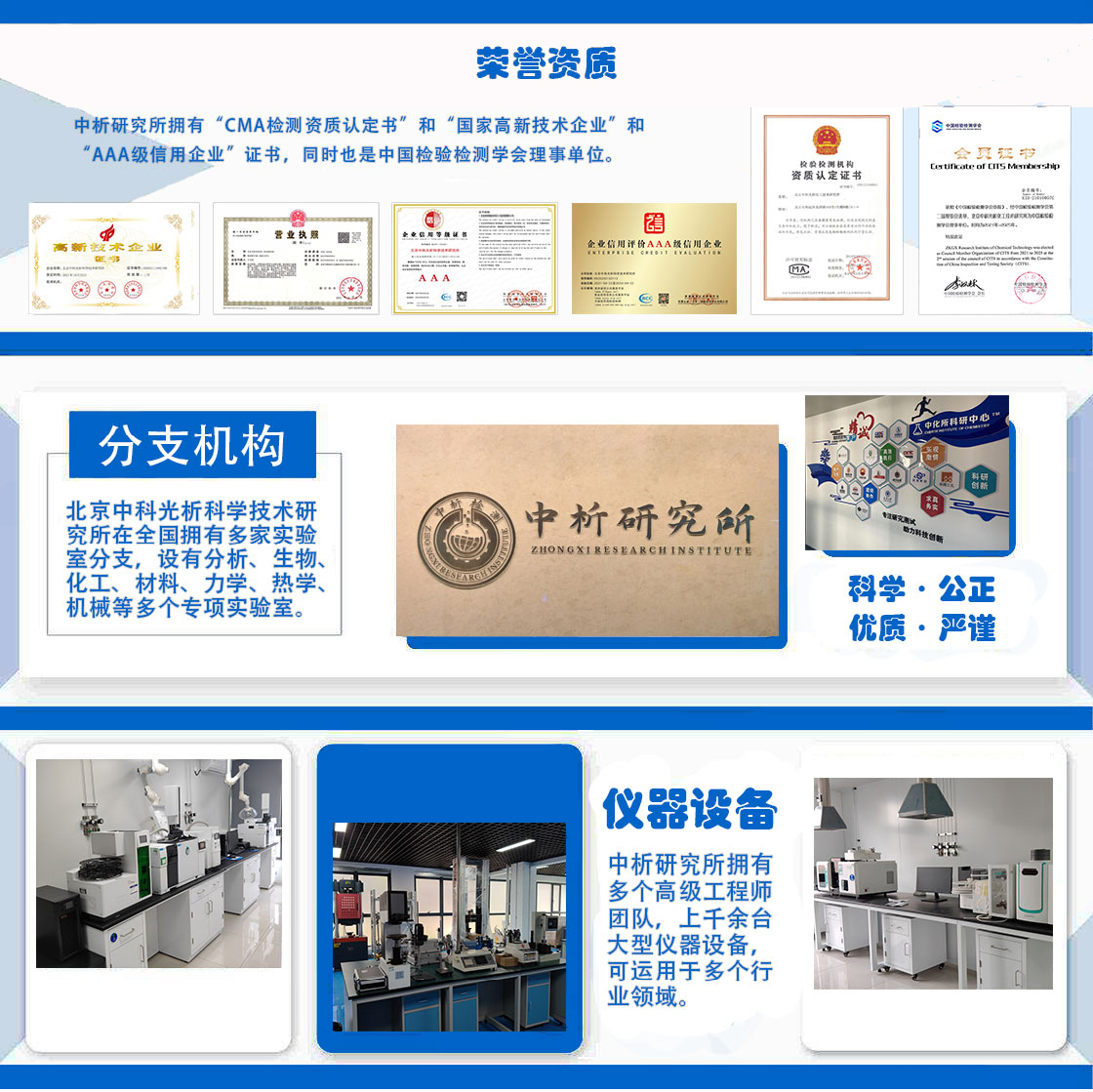
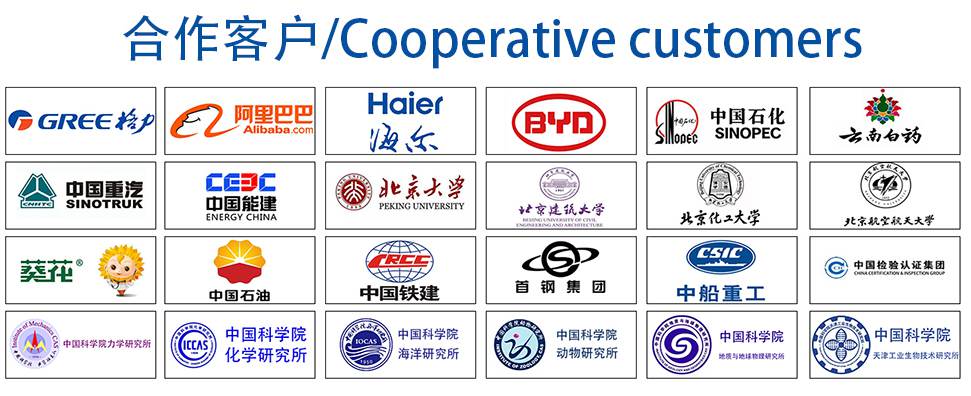
材料实验室
热门检测
254
215
190
203
197
204
210
201
207
217
203
199
203
203
197
195
210
199
209
202
推荐检测
联系电话
400-635-0567