外观检验与尺寸检查:核心检测项目与质量控制要点
一、外观检验:确保产品外观完整性
1. 检测项目
-
- 划痕/刮伤:肉眼可见的线性痕迹,常见于金属、玻璃、塑料表面。
- 裂纹:材料内部或表面的断裂,需借助放大镜或显微镜检测。
- 凹陷/凸起:由加工或运输导致的形变,影响装配与美观。
- 毛刺/飞边:常见于注塑或机加工件边缘的多余材料。
-
- 色差:使用色差仪(ΔE值)量化检测,符合Pantone或RAL标准。
- 涂层均匀性:检查电镀、喷涂是否覆盖完全,无剥落、气泡。
- 氧化/腐蚀:金属件在潮湿环境下的锈蚀痕迹。
-
- 印刷清晰度:文字、条码、商标是否模糊、错位。
- 标签贴合度:标签起翘、卷边或粘贴错误。
-
- 缝隙均匀性:如手机屏幕与边框间隙需符合设计公差(如±0.1mm)。
- 部件缺失或错位:螺丝未紧固、按键装配不平等。
-
- 封口密封性:防伪标签是否破损,包装盒有无压痕、污渍。
2. 检测方法与工具
- 目视检查:依赖标准光源箱(如D65光源)消除环境光干扰。
- 自动化光学检测(AOI):机器视觉系统捕捉微米级缺陷,适用于电子元件检测。
- 触摸检测:针对表面粗糙度(Ra值)要求,使用触针式粗糙度仪。
- 放大设备:20倍放大镜或工业显微镜检测微观裂纹。
3. 行业应用案例
- 汽车行业:依据VDA 6.3标准,车身外观需100%无可见橘皮纹(涂层缺陷)。
- 消费电子:手机屏幕需通过“暗室检测”避免亮斑、漏光。
二、尺寸检查:精度决定产品性能
1. 检测项目
-
- 长度/宽度/高度:基础几何尺寸,决定产品能否装配。
- 孔径与间距:如PCB板插孔位置公差需≤0.05mm。
- 同心度/圆度:轴类零件的径向跳动影响旋转精度。
-
- 平面度:检测平台表面是否平整,使用激光干涉仪。
- 垂直度/平行度:如机床导轨的垂直偏差需≤0.02mm/m。
- 位置度:多孔位零件(如发动机缸体)的孔组相对位置。
-
- 间隙匹配:如轴承与轴的过盈配合需符合H7/s6标准。
- 螺纹精度:通止规检测螺纹通规(GO)和止规(NO-GO)。
2. 检测工具与技术
- 传统量具:游标卡尺(分辨率0.02mm)、千分尺(精度±0.001mm)。
- 坐标测量机(CMM):基于ISO 10360标准,实现三维复杂尺寸测量。
- 激光扫描:快速获取曲面点云数据,对比CAD模型偏差。
- 光学投影仪:适用于微小零件轮廓比对(如钟表齿轮)。
3. 关键控制点
- 环境温湿度:ISO 1级实验室要求恒温20±1℃,避免热膨胀误差。
- 测量力控制:接触式测量时需控制探头压力(如3N±1N)。
- 数据统计:运用SPC(统计过程控制)分析CPK值,确保制程稳定性。
三、综合质量控制策略
-
- 首件检验(FAI)+ 巡检 + 末件检验,覆盖生产全过程。
- 使用数字孪生技术模拟装配,提前发现尺寸干涉问题。
-
- 引入AI视觉分拣系统,实现缺陷分类与实时报警。
- 物联网(IoT)传感器监控设备精度,自动触发校准程序。
-
- 航空航天:AS9100标准要求尺寸检测报告可追溯至NIST标准件。
- 医疗器械:FDA 21 CFR Part 820规定关键尺寸需100%全检。
四、总结
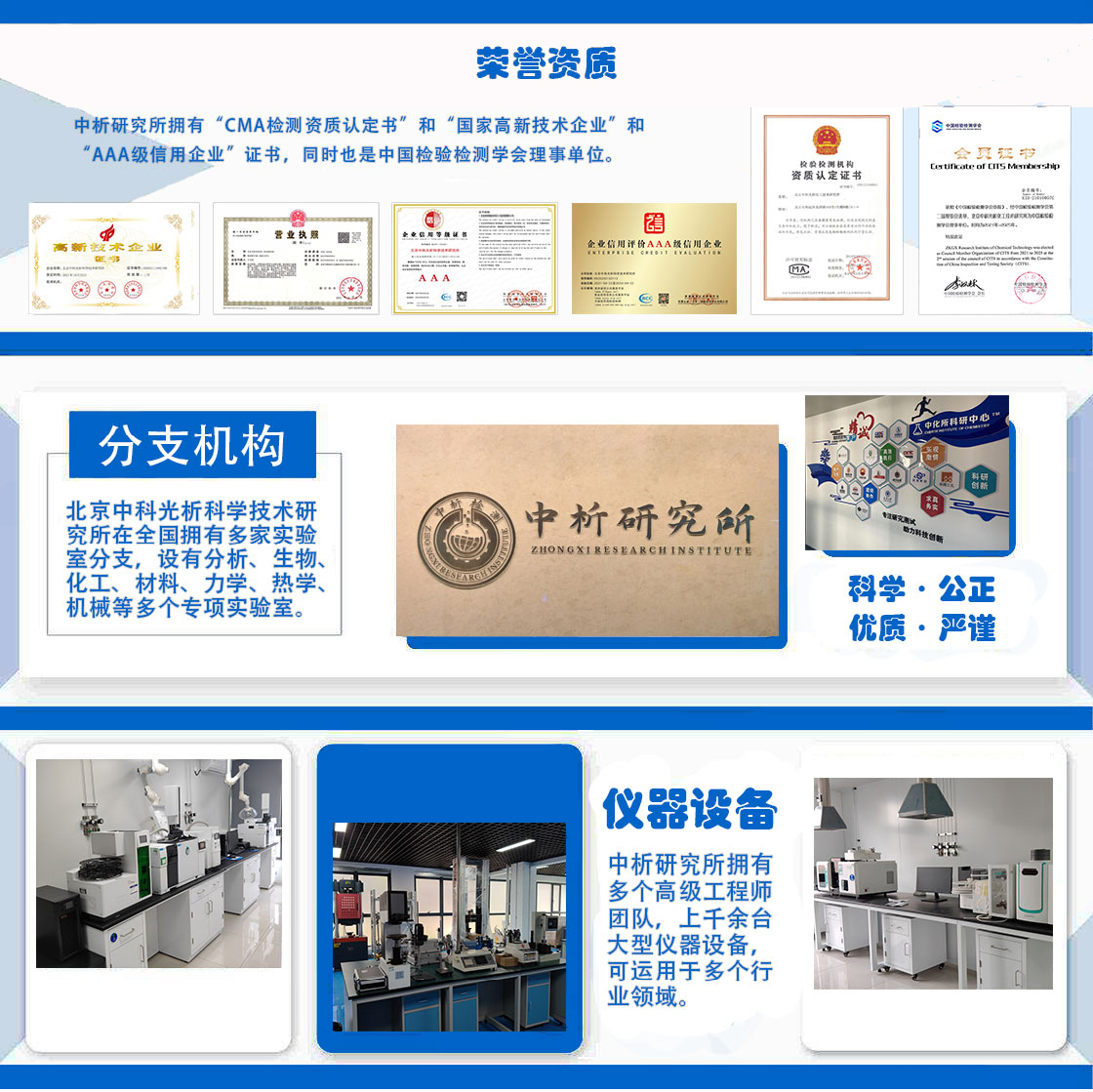
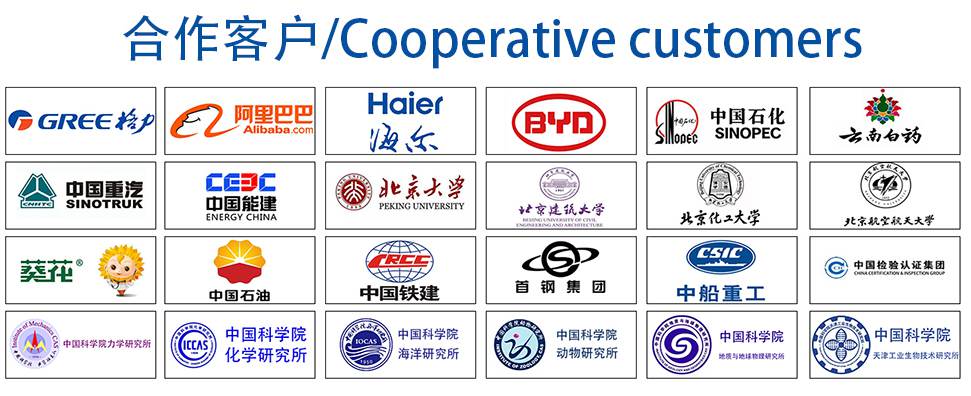
材料实验室
热门检测
254
215
190
203
197
204
210
202
207
217
203
199
203
203
197
195
210
199
209
202
推荐检测
联系电话
400-635-0567