热冲击与温度循环检测:核心检测项目详解
一、检测目的
-
- 快速温度转换:模拟产品在极短时间内经历极端高温到低温(或反向)的剧烈变化,检测材料膨胀/收缩导致的失效(如开裂、分层、焊接断裂)。
- 加速老化:通过高应力加速暴露潜在缺陷。
-
- 渐变温度变化:模拟自然环境中缓慢的温度波动,评估材料疲劳、连接器松动、密封失效等问题。
- 长期可靠性:验证产品在生命周期内的耐久性。
二、核心检测项目
1. 热冲击测试项目
项目 | 参数要求与说明 |
---|---|
温度范围 | - 高温区:通常设定为+125°C至+200°C(依产品规格调整)- 低温区:-40°C至-65°C |
转换时间 | ≤15秒(两温区间快速切换,确保温度冲击效果) |
驻留时间 | 高温/低温区停留时间:通常5~30分钟(确保样品温度完全稳定) |
循环次数 | 50~1000次(根据标准或客户要求,如MIL-STD-883G) |
样品数量 | 至少5件(确保统计有效性) |
- 材料兼容性:不同材料(金属、塑料、陶瓷)的膨胀系数差异是否导致结构失效。
- 焊点可靠性:BGA焊接、引脚连接处是否开裂。
- 封装完整性:芯片封装、密封件是否出现气密性下降。
2. 温度循环测试项目
项目 | 参数要求与说明 |
---|---|
温度范围 | - 高温:+85°C至+150°C- 低温:-40°C至-55°C |
升降速率 | 通常为5°C/min~15°C/min(模拟自然温度变化速率) |
高低温保持时间 | 每个极端温度停留30~60分钟(确保热传导均匀) |
循环次数 | 500~2000次(依据JEDEC JESD22-A104标准) |
温湿度控制 | 部分测试需结合湿度(如85°C/85%RH,用于潮敏器件) |
- 疲劳失效:金属化层开裂、PCB铜箔剥离。
- 电气性能漂移:电阻、电容值变化是否超出阈值。
- 涂层/镀层脱落:表面防护层是否因热胀冷缩剥落。
三、通用检测流程
- 预处理:样品在标准温湿度环境中静置24小时以消除应力。
- 初始检测:记录外观、电气性能、机械强度等基线数据。
- 测试执行:
- 热冲击:使用双腔体试验箱实现快速温度切换。
- 温度循环:单腔体试验箱通过程序控温。
- 中间检测:每50~100次循环后暂停测试,进行功能性检查。
- 最终检测:完成全部循环后,复测关键参数并解剖分析失效模式。
四、失效分析与评估标准
-
- 断裂(焊点、引线)
- 分层(PCB、封装内部)
- 电气短路/断路
- 密封失效(漏气、渗液)
-
- 国际标准:IEC 60068-2-14(热冲击)、IEC 60068-2-1(温度循环)。
- 行业标准:汽车电子遵循AEC-Q100,军工产品参照MIL-STD-810。
- 客户定制:根据特定应用场景(如航天、深海设备)调整严苛度。
五、注意事项
- 样品安装:避免机械应力干扰,使用非导热夹具固定。
- 温度均匀性:试验箱内温度波动需≤±2°C。
- 数据记录:全程监控温度曲线,记录关键节点数据。
- 失效分析:对失效样品进行SEM/EDS分析,明确根本原因。
六、总结
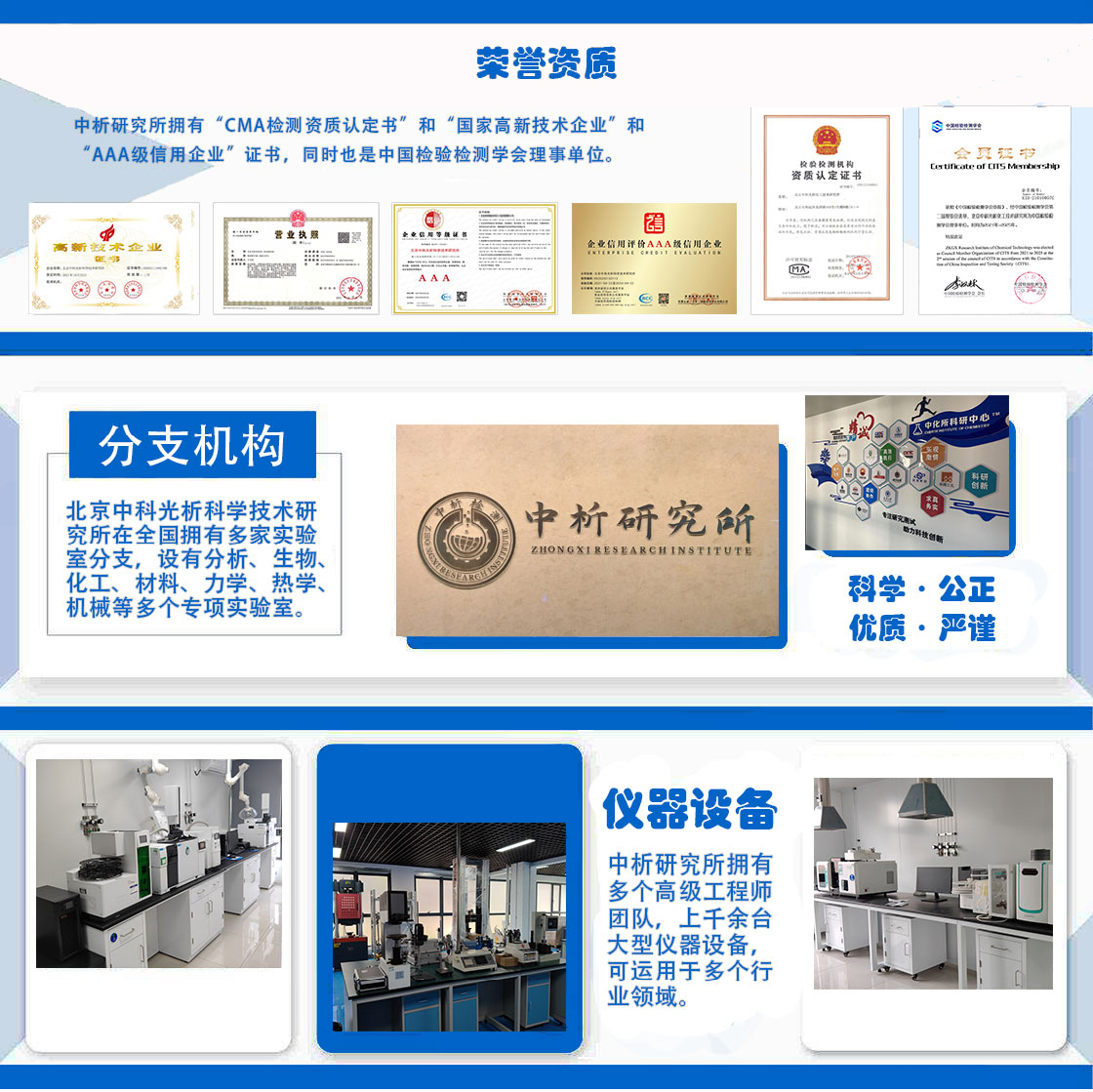
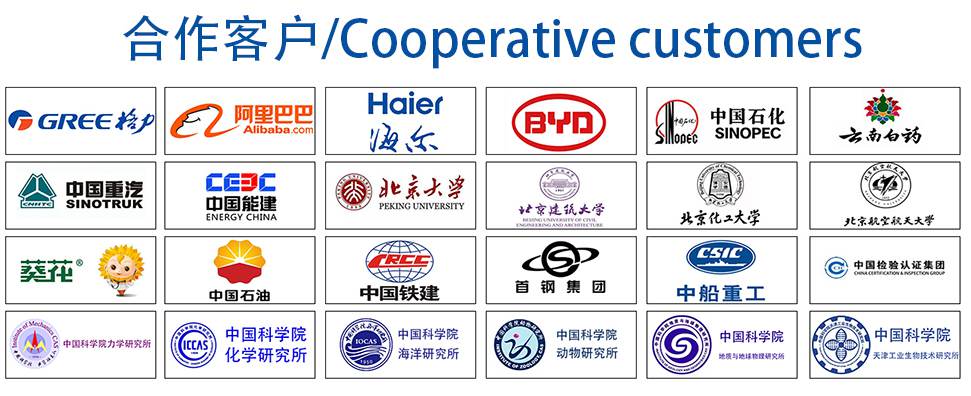
材料实验室
热门检测
271
228
202
211
210
215
225
218
228
229
215
214
219
216
210
205
222
207
220
214
推荐检测
联系电话
400-635-0567