频率响应检测:核心检测项目与技术解析
一、频率响应检测的核心意义
二、核心检测项目分类
1. 幅度响应检测(Amplitude Response)
- 目的:测量系统对不同频率输入信号的增益或衰减变化。
- 检测方法:
- 正弦扫描法:使用信号发生器输出扫频正弦波,记录被测系统输出信号的幅度变化,计算增益(dB)= 20log(Vout/Vin)。
- 快速傅里叶变换(FFT)法:输入宽频信号(如白噪声),通过FFT分析输入与输出频谱之比。
- 关键指标:
- 通带平坦度:通带内增益波动范围(如±0.5dB)。
- 截止频率:增益下降3dB对应的频率点(带宽)。
- 带外衰减:阻带内信号衰减程度(如>40dB/十倍频程)。
2. 相位响应检测(Phase Response)
- 目的:评估系统对各频率信号的时间延迟特性。
- 检测方法:
- 双通道示波器法:输入正弦波,通过示波器测量输入与输出波形的相位差。
- 网络分析仪法:直接读取矢量网络分析仪显示的相位-频率曲线。
- 关键指标:
- 群时延(Group Delay):相位对频率的导数(dφ/df),反映信号不同频率分量的传输时间一致性。
- 相位线性度:理想相位响应应为线性,非线性会导致信号失真。
3. 瞬态响应检测(Transient Response)
- 目的:测试系统对阶跃信号或脉冲信号的快速响应能力。
- 检测方法:
- 阶跃信号法:输入方波信号,观察输出信号的上升时间、过冲及振荡。
- 脉冲响应法:通过脉冲激励测量系统的冲击响应,转换至频域分析。
- 关键指标:
- 上升时间(Rise Time):输出从10%到90%幅值所需时间,与带宽成反比。
- 过冲(Overshoot):最大偏离稳态值的百分比(如<5%)。
4. 谐波失真检测(Total Harmonic Distortion, THD)
- 目的:评估系统非线性导致的谐波分量。
- 检测方法:
- 单频正弦波测试:输入纯正弦波,通过频谱仪测量输出信号中各次谐波(2nd、3rd…)的幅度。
- 计算公式:THD = √(Σ谐波功率)/基波功率 × 100%。
- 关键指标:
- THD+N:总谐波失真加噪声(如音频设备要求THD+N < 0.1%)。
5. 互调失真检测(Intermodulation Distortion, IMD)
- 目的:检测系统对多频信号的非线性交叉调制。
- 检测方法:
- 双音法:输入两个不同频率(f1、f2)的正弦波,测量输出中互调产物(如2f1-f2、2f2-f1)的幅度。
- 标准测试信号:如CCIF标准的19kHz+20kHz双音信号。
- 关键指标:
- IMD值:互调分量与原始信号的幅度比(如<-60dB)。
6. 噪声响应检测(Noise Floor & SNR)
- 目的:评估系统固有噪声对信号的影响。
- 检测方法:
- 无信号输入法:输入端短路,测量输出端噪声功率谱密度。
- 信噪比(SNR):最大输出信号幅度与噪声幅度的比值(dB)。
- 关键指标:
- 等效输入噪声(EIN):折合到输入端的等效噪声电压(如-120d)。
三、检测设备与标准
-
- 频谱分析仪:用于频域分析(幅度、谐波)。
- 矢量网络分析仪(VNA):支持S参数测量(幅频、相频)。
- 动态信号分析仪:兼具FFT、阶跃响应分析功能。
- 高精度信号发生器:输出低失真扫频信号。
-
- 电磁屏蔽:避免外界干扰(如射频信号)。
- 温度控制:部分器件对温度敏感(如晶振)。
- 负载匹配:终端阻抗需符合被测系统要求(如50Ω或高阻)。
-
- 音频设备:IEC 60268-3(扬声器)、AES17(THD测试)。
- 通信系统:3GPP TS 36.521(射频模块频率响应)。
- 传感器:ISO 16063(振动传感器校准)。
四、典型应用案例分析
五、常见问题与解决方案
六、总结
上一篇:热冲击,温度循环检测下一篇:气候序列检测
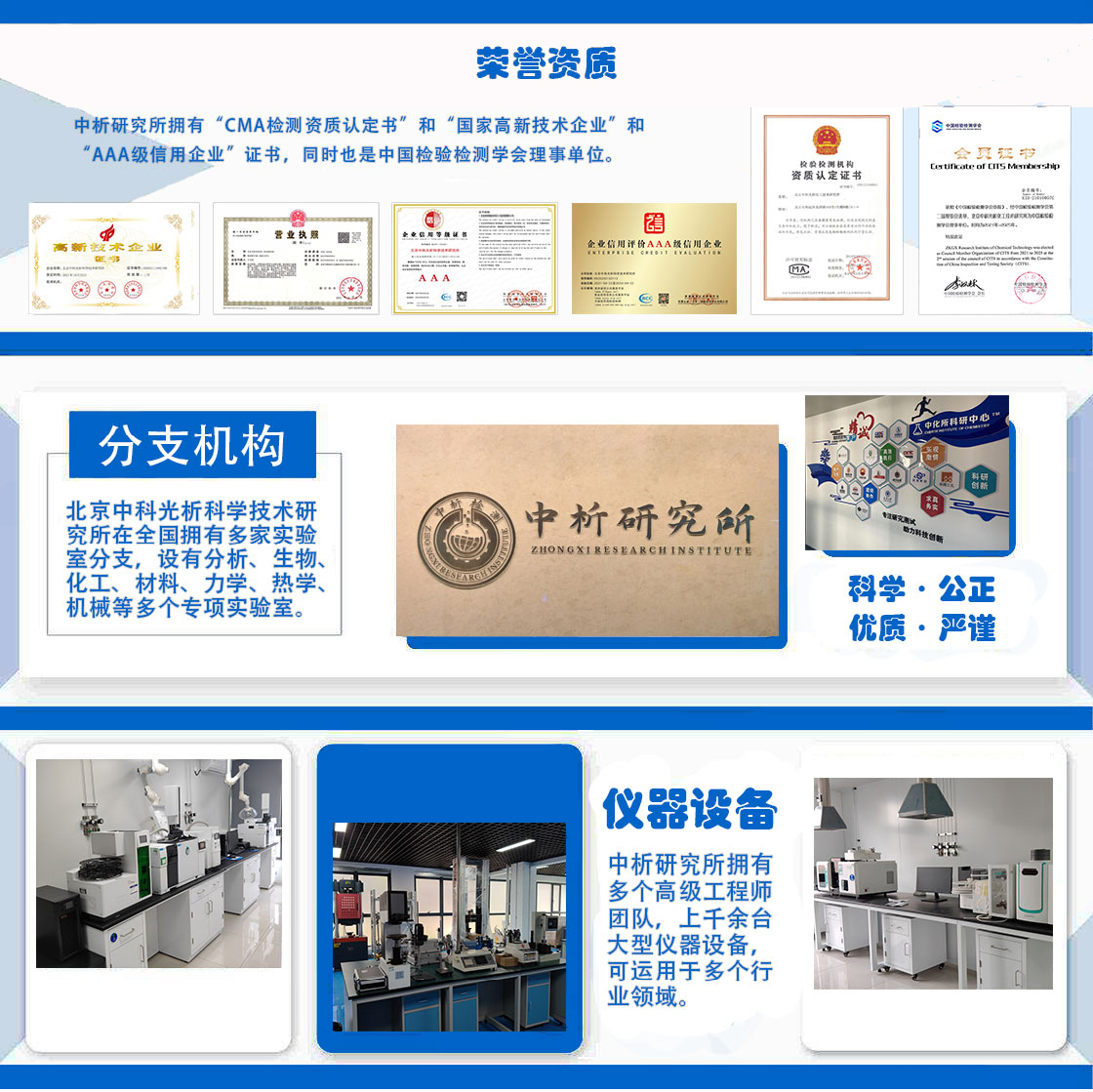
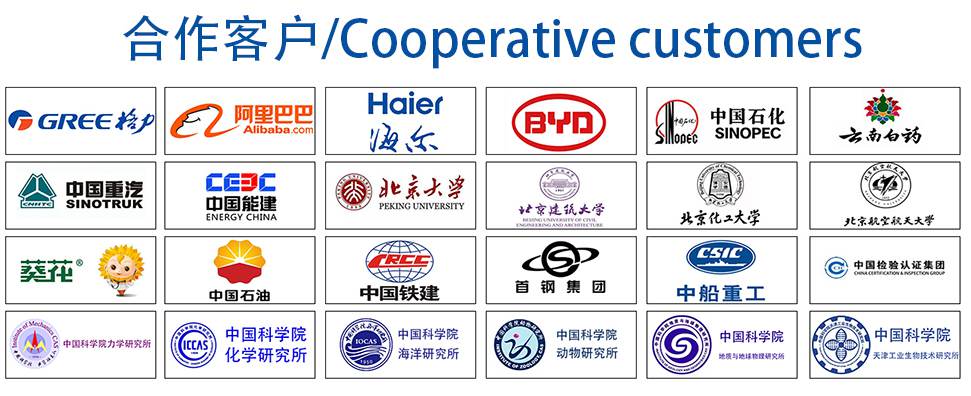
材料实验室
热门检测
271
228
202
211
210
215
225
218
228
229
215
214
218
216
210
205
221
207
220
214
推荐检测
联系电话
400-635-0567