一、失效判据检测的核心意义
- 针对性:与产品实际工况和使用场景高度匹配;
- 可量化:通过实验数据或仿真模型建立明确的判定阈值;
- 覆盖性:涵盖关键失效模式,如疲劳、腐蚀、磨损、过载等。
二、检测项目的分类与实施方法
1. 机械性能检测
- 检测内容:拉伸强度、硬度、冲击韧性、疲劳寿命等;
- 方法:
- 使用万能试验机进行拉伸/压缩测试(依据ASTM E8/E21标准);
- 疲劳试验(高频循环加载,记录裂纹萌生与扩展数据);
- 硬度测试(布氏、洛氏、维氏硬度法)。
2. 材料微观结构分析
- 检测内容:晶粒尺寸、相组成、夹杂物分布、裂纹形貌等;
- 方法:
- 金相显微镜观察(ASTM E3标准);
- 扫描电镜(SEM)与能谱分析(EDS);
- X射线衍射(XRD)测定残余应力。
3. 环境适应性检测
- 检测内容:耐腐蚀性、高温氧化、低温脆化等;
- 方法:
- 盐雾试验(ASTM B117标准);
- 恒温恒湿加速老化试验;
- 热震试验(快速温度变化模拟)。
4. 功能性失效检测
- 检测内容:电子元件电性能退化、密封性失效、传动系统效率下降等;
- 方法:
- 电路参数测试(如漏电流、阻抗);
- 氦质谱检漏法检测密封性;
- 振动台模拟工况下的性能衰减。
5. 寿命与可靠性试验
- 检测内容:MTBF(平均无故障时间)、磨损寿命、加速寿命预测;
- 方法:
- 加速寿命试验(ALT)通过高应力条件外推实际寿命;
- 威布尔分布模型分析失效数据;
- 蒙特卡洛仿真预测系统可靠性。
三、检测项目的行业应用案例
-
- 检测重点:涡轮叶片的蠕变失效与热疲劳;
- 项目设计:高温持久试验(800°C以上,持续加载)结合SEM分析微裂纹扩展路径。
-
- 检测重点:锂离子电池的热失控与容量衰减;
- 项目设计:充放电循环测试(GB/T 31486标准)结合红外热成像监控温度分布。
-
- 检测重点:焊缝的疲劳裂纹与腐蚀失效;
- 项目设计:超声波探伤(UT)检测内部缺陷,辅以电化学腐蚀速率测量。
四、检测流程与数据分析
- 流程标准化
- 定义失效模式→选择检测项目→制定实验方案→数据采集→阈值比对→输出。
- 关键数据分析技术
- 统计过程控制(SPC)分析数据波动;
- 有限元分析(FEA)验证实验与仿真的吻合度;
- 机器学习算法预测多因素耦合下的失效风险。
五、挑战与未来趋势
- 技术难点
- 多物理场耦合失效的检测(如热-力-化学交互作用);
- 微小缺陷(纳米级裂纹)的早期识别。
- 智能化发展方向
- 基于物联网(IoT)的实时健康监测系统;
- 数字孪生技术实现虚拟检测与物理实验的融合。
六、
上一篇:尺寸和重量检查检测下一篇:热冲击,温度循环检测
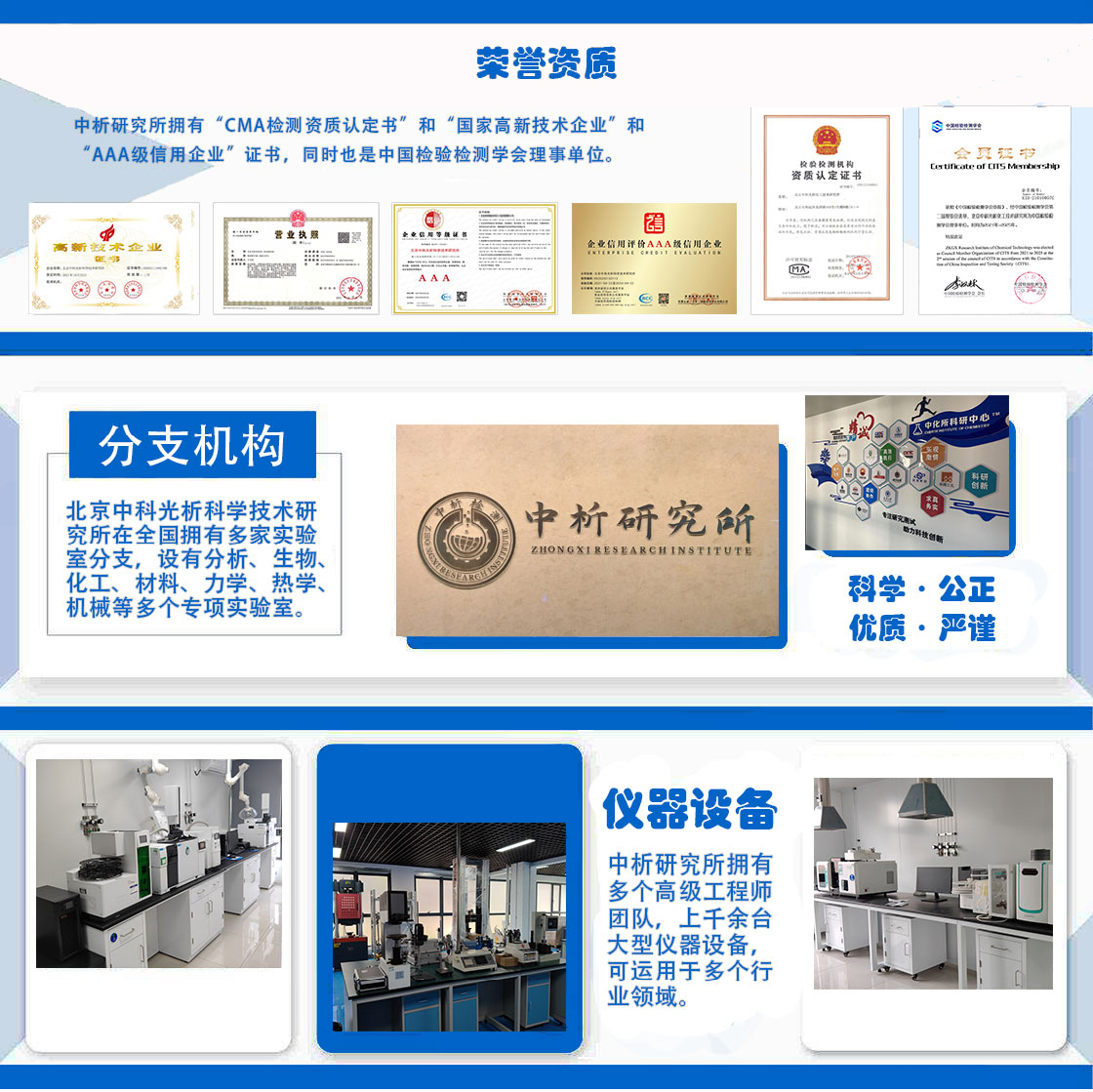
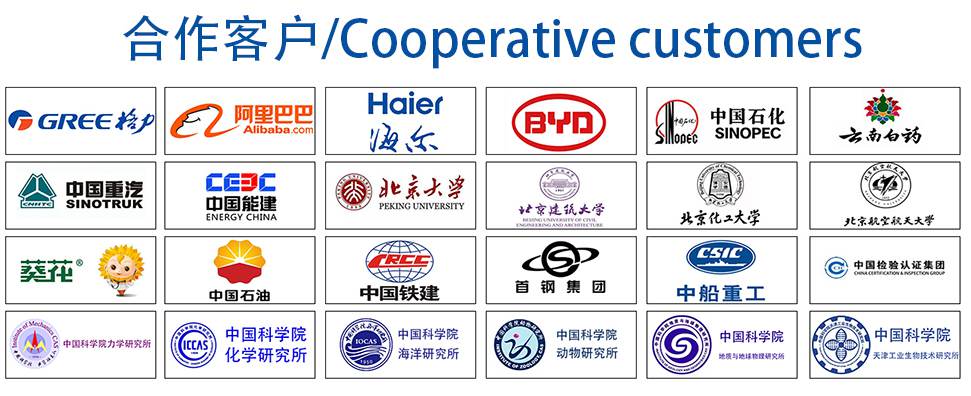
材料实验室
热门检测
271
228
202
211
210
215
225
218
228
229
215
214
218
216
210
205
221
207
220
214
推荐检测
联系电话
400-635-0567