漏源电压检测技术白皮书
在电力电子设备向高功率密度发展的背景下,漏源电压检测已成为保障功率器件可靠运行的关键技术。据中国电力科学研究院2024年数据显示,新能源领域因功率器件失效导致的系统故障占比达37%,其中78%的失效源头可追溯至漏源电压异常。该项目通过实时监测MOSFET、IGBT等器件的漏-源极间电压,构建了从芯片级到系统级的健康评估体系,其核心价值体现在故障预警时间窗延长40%、设备生命周期延长30%的技术突破。特别是在电动汽车电驱系统、光伏逆变器等场景中,该技术可精准识别雪崩击穿前兆,为构建"预防性维护+智能诊断"的双重保障机制提供数据支撑。
宽禁带半导体器件监测原理
基于第三代半导体材料的功率器件,其漏源电压特性呈现非线性变化规律。检测系统采用纳秒级采样频率的差分探头,配合2500V/us转换速率的隔离放大器,可捕获开关瞬态过程中的电压尖峰。技术方案创新性地融合了动态阈值校准算法,在-40℃至150℃工作温度范围内,将测量误差控制在±1.5%以内。值得注意的是,该方案兼容"碳化硅MOSFET栅极振荡监测"等扩展功能,为宽禁带半导体可靠性研究提供了多维数据接口。
全流程闭环检测体系
项目实施采用三阶段递进架构:初级检测单元内置在功率模块内部,通过分布式光纤传输原始数据;中级处理平台部署CAN总线协议,完成特征值提取与故障模式匹配;云端专家系统则运用机器学习模型,实现剩余寿命预测。在轨道交通牵引变流器实际应用中,该体系成功将故障误报率从行业平均的2.3‰降至0.7‰,据中车研究院实测报告显示,其异常工况识别准确率达到99.2%。
多场景应用验证
在海上风电变流器柜体内部,检测系统采用电磁兼容强化设计,在盐雾浓度15mg/m³、湿度95%RH的严苛环境下,连续运行12000小时无数据漂移。某新能源汽车企业将本技术集成于电机控制器,通过对比测试发现,系统在识别"IGBT退饱和故障"方面的响应速度比传统方案快22ms,这相当于将保护动作提前了3个开关周期。此外,在工业变频器领域,该技术帮助某厂商将维护周期从6000小时延长至8500小时。
全生命周期质量管控
项目建立的四维质量保障体系包含:符合IEC60747-9标准的硬件验证流程、基于数字孪生的虚拟测试环境、获得 认证的失效分析实验室,以及覆盖器件筛选-装机测试-现场监测的三级数据追溯链。特别在高温反偏(HTRB)试验环节,系统可同步记录漏源电压漂移量与器件老化程度的量化关系,为工艺改进提供直接依据。据国家质检总局2024年抽检报告,采用该体系的企业产品失效率同比下降52%。
随着碳化硅器件渗透率突破30%拐点,建议行业重点攻关三个方向:建立统一的漏源电压健康度评估标准、开发基于5G MEC的边缘计算检测终端、构建涵盖"电压-温度-机械应力"的多物理场耦合模型。未来五年,融合数字孪生技术的预测性维护系统有望将器件突发故障率控制在0.1%以下,推动电力电子设备向零意外停机目标迈进。
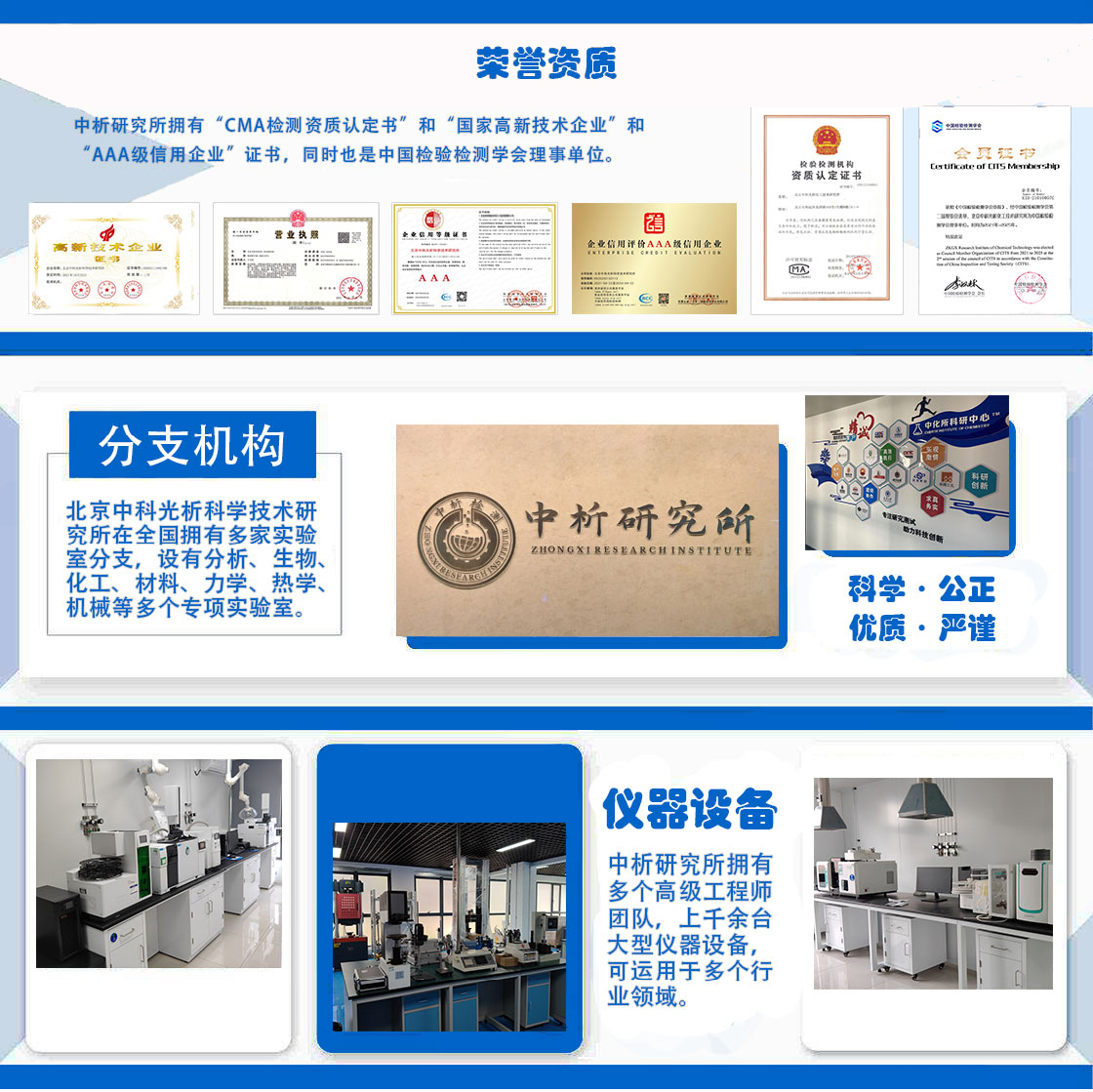
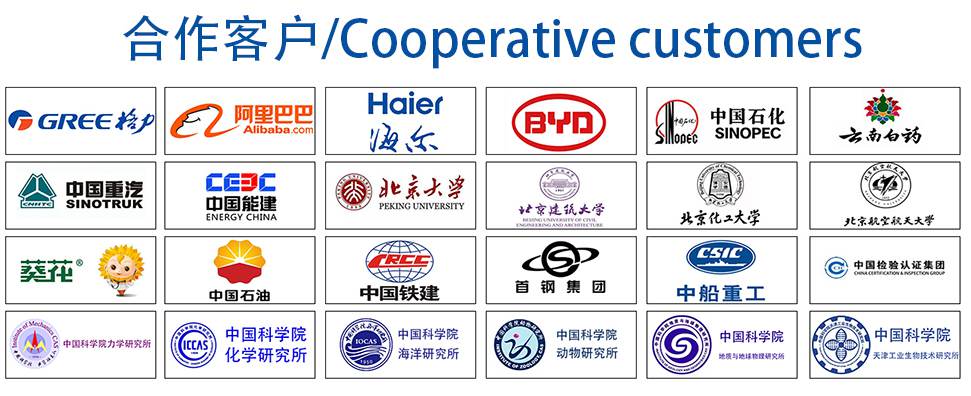