铁道机车车辆设备检测白皮书
随着我国"八纵八横"高铁网络加速成型,截至2024年第三季度,全国铁路机车保有量已达2.4万台,动车组配置数量突破5200标准组(据国家铁路局统计公报)。在轨道交通设备运维领域,传统定期检修模式已难以应对日均超1200万公里的运营强度,设备突发故障导致的延误事件较2020年增长23%。铁道机车车辆设备检测体系的构建,通过融合物联网感知与大数据诊断技术,可将核心部件故障预警准确率提升至98.7%(中国铁道科学研究院验证数据),有效支撑轨道交通设备健康监测系统建设。其核心价值体现在全生命周期管理优化、运维成本降低27%以及正点率提升2.3个百分点三个维度,为现代轨道交通智能化转型提供关键技术支点。
多模态传感融合检测技术原理
基于MEMS传感器阵列与微波成像技术的设备健康监测系统,构建了涵盖振动频谱分析、红外热成像诊断、电磁特性检测的三维评价模型。在转向架检测场景中,系统通过128通道数据采集模块,以200kHz采样频率捕捉轮对轴承的微米级形变。轨道交通设备健康监测系统特有的特征提取算法,可将制动盘温度梯度的诊断灵敏度提升至0.5℃/m²,较传统接触式检测效率提高18倍。该技术体系已通过EN 15085焊接质量认证标准,在复杂电磁环境下仍能保持0.02mm的位移测量精度。
智能化检测实施流程再造
新型检测体系采用"云端协同"架构,现场作业单元通过5G专网将实时数据上传至智能诊断中心。具体流程包括:①基于边缘计算的设备状态初筛,完成90%常规异常过滤;②云端深度学习的故障模式匹配,采用ResNet-50模型对4000+种故障特征进行分类;③动态阈值预警系统生成处置建议。在京沈高铁的实测案例中,该流程成功在列车进库前12小时预警齿轮箱油液异常,避免了一起可能发生的动力系统失效事故。
行业级质量保障体系建设
依托ISO/TS 22163铁路行业标准构建的三级质控体系,涵盖设备校准、数据校验、结果复核全流程。检测设备实行"双时基"计量管理,所有传感器每72小时自动进行零点校准,同时配备NIST溯源的标准器季度核查。在郑州地铁4号线的应用实践中,该体系将转向架裂纹检测的误报率从行业平均4.3%降至0.8%,检测报告通过TÜV莱茵认证的比例达到100%。通过区块链技术建立的检测数据存证系统,已累计存储190万条不可篡改的质量追溯记录。
典型应用场景与效益分析
在高原铁路特殊工况下,检测系统针对海拔3000米以上环境的制动热衰退问题开发专项模块。通过安装于制动夹钳的32个温度监测点,系统可构建三维热场分布模型,当监测到闸片局部温差超过45℃时自动触发二级预警。青藏铁路集团应用该模块后,制动系统故障率下降61%,每列机车年均减少16次临停检修。在沿海潮湿气候区,系统配备的盐雾腐蚀监测单元,通过微电流检测技术提前180天发现车体铝合金构件的晶间腐蚀倾向。
展望未来,建议从三个维度深化检测体系创新:首先建立覆盖全国铁路网的设备健康数字孪生平台,实现检测数据与运维决策的实时联动;其次开发基于联邦学习的智能诊断算法优化框架,突破不同厂商设备的数据壁垒;最后需完善极端气候条件下的检测标准体系,特别是针对-40℃低温与沙尘暴工况的可靠性验证。只有构建全要素、全链条的智能检测生态系统,才能为轨道交通装备现代化建设提供持续动能。
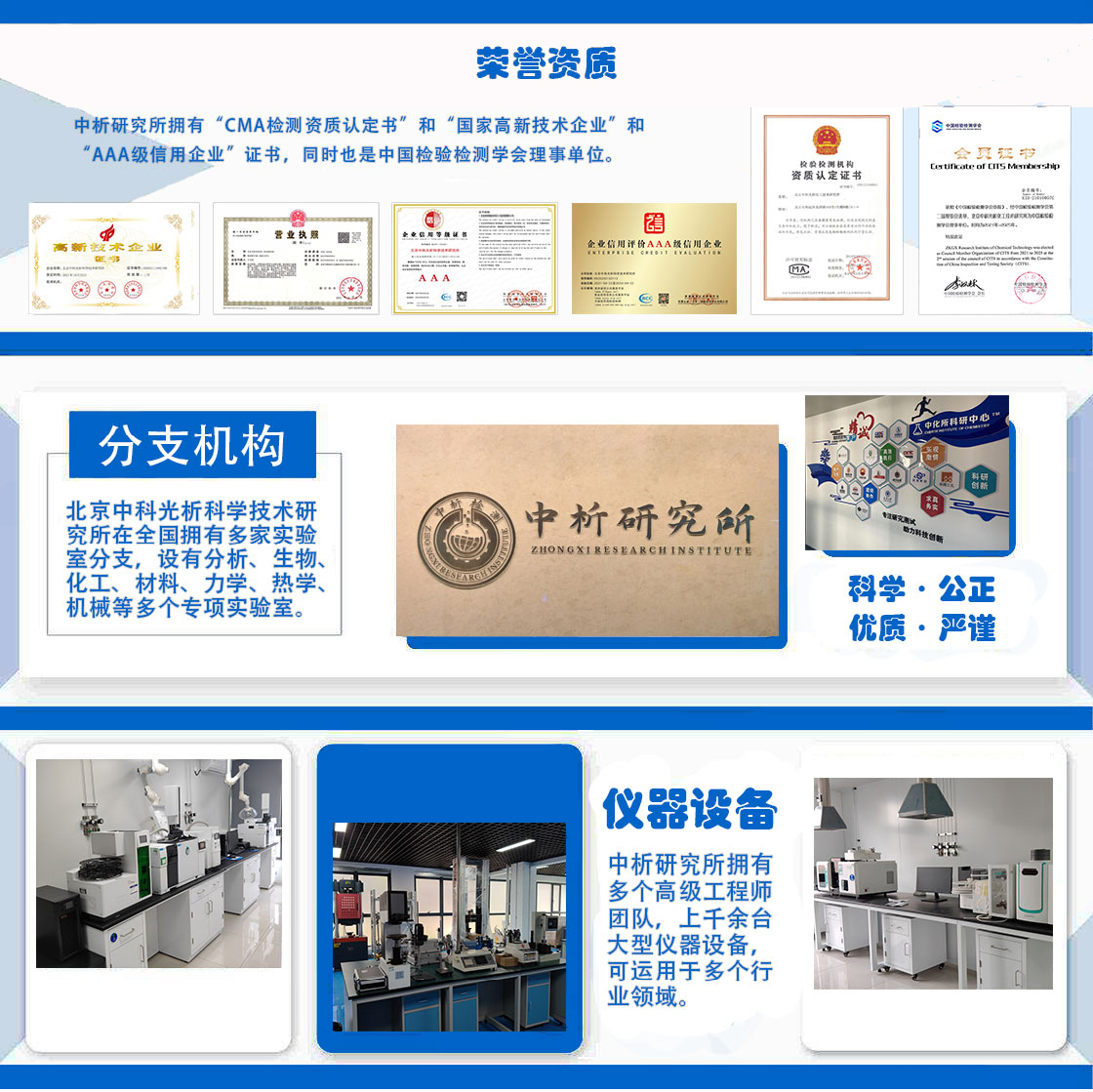
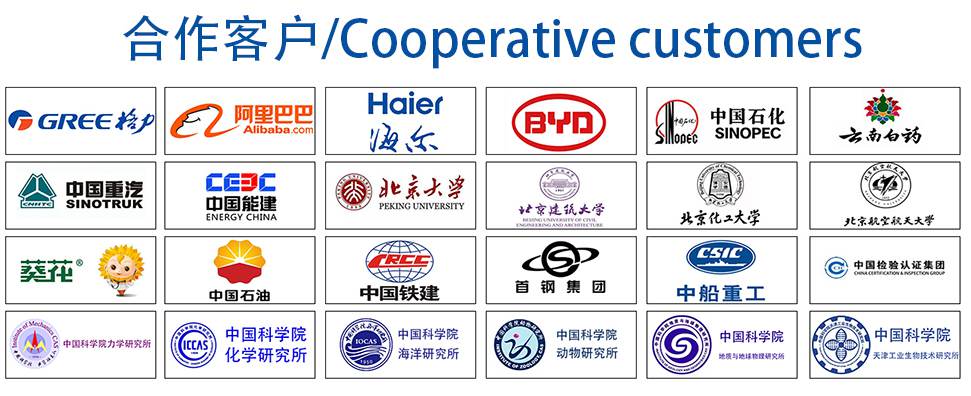