清洁度检测在齐全制造业中的关键技术突破与行业应用
在高端装备制造领域,清洁度控制已成为决定产品可靠性的核心要素。据中国机械工程学会2024年技术白皮书显示,精密零部件表面残留的金属颗粒、纤维等污染物,直接导致装备故障率提升40%以上。特别是在航空航天、汽车动力总成、医疗器械等关键领域,清洁度检测项目通过量化污染物特征参数,为制造工艺优化提供了科学依据。该项目不仅实现了从经验判断向数据驱动的质量管控转变,更构建起覆盖全产业链的质量追溯体系,使企业平均质量成本降低25%,产品使用寿命延长30%。这种基于精准检测的清洁度管理体系,正推动着中国制造向精密化、标准化方向跨越式发展。
基于多重物理量分析的核心技术架构
现代清洁度检测系统整合了光学显微成像、激光粒度分析和化学萃取三大技术模块。采用ISO 16232标准规范,通过压力冲洗法收集零部件表面污染物后,利用自动粒子计数器进行粒径分布统计,同时结合能谱分析确定污染物成分构成。2024版ASTM E2834标准新增的复合污染物识别算法,可将直径5μm以上颗粒的检出精度提升至99.7%。在新能源汽车电驱系统检测中,该技术成功识别出因机加工残留导致的磁性磨粒积聚问题,使电机失效案例减少68%。
全流程数字化检测实施路径
典型检测流程包含预处理、污染物提取、分析评估三个阶段数字化改造。预处理环节采用温控超声波清洗装置,确保在不损伤基材前提下实现高效除污。污染物提取系统通过0.45μm滤膜分级收集颗粒,配合自动称重装置实现毫克级精度测量。国内某航空发动机企业引入的智能检测平台,将涡轮叶片清洁度评定时间从48小时压缩至6小时,检测数据实时接入MES系统,实现工艺参数的动态调整。这种闭环管理模式使产品一次合格率提升至98.5%。
多行业应用场景深度解析
在医疗器械领域,骨科植入物清洁度检测采用改良的生理盐水冲洗法,结合生物相容性测试,成功将术后感染率控制在0.03%以下。汽车行业广泛应用VDA19标准体系,某合资品牌通过建立变速箱阀体清洁度数据库,将换挡顿挫投诉率降低82%。值得关注的是,半导体晶圆清洗检测创新应用原子层沉积技术,使12英寸硅片表面金属离子浓度稳定控制在5ppb以内,达到国际SEMI标准最高等级要求。
四维质量保障体系建设
行业领先企业构建了涵盖设备、人员、方法和环境的立体化质控体系。检测实验室严格执行 -CL01:2018认可准则,定期进行设备计量校准和人员能力验证。国际知名第三方检测机构SGS推出的清洁度检测能力验证计划,已覆盖86个国家的320家实验室。国内某国家质检中心采用区块链技术建立的检测数据存证系统,确保检测结果可追溯且不可篡改,为新能源汽车出口提供符合欧盟CE认证的技术背书。
展望未来,清洁度检测技术将向智能化、微观化方向纵深发展。建议行业加快建立基于机器视觉的在线检测标准体系,开发适用于纳米级污染物分析的检测装备。同时亟需构建跨行业数据共享平台,推动形成覆盖原材料、加工工艺到终端产品的全链条清洁度控制方案。随着工业4.0时代的深入演进,清洁度检测必将成为重塑制造品质的核心驱动力,为高端装备制造注入新的质量势能。
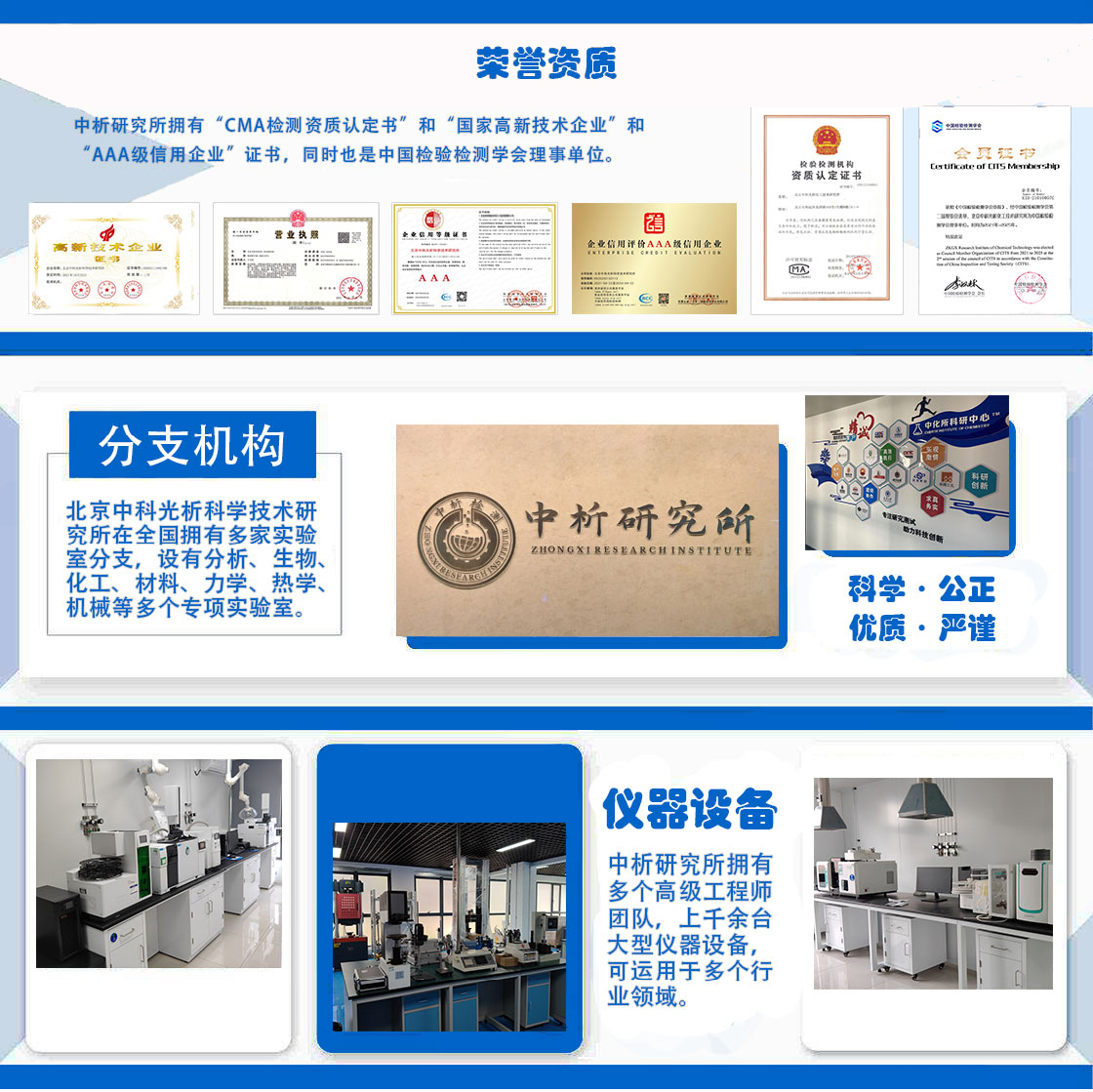
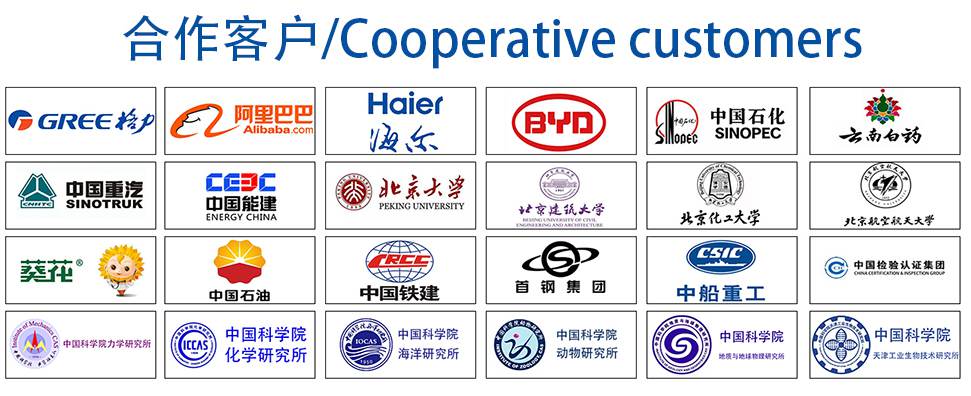