有正向平均电流耗散时的反向峰值电流检测技术白皮书
在电力电子设备可靠性验证领域,反向峰值电流检测已成为大功率半导体器件质量控制的核心环节。据中国电力科学研究院2024年数据显示,新能源汽车电控系统故障中27.3%与IGBT模块的反向恢复特性异常直接相关。随着宽禁带半导体器件在智能电网、轨道交通等场景的普及,器件在正向导通工况下的反向耐冲能力面临更严苛考验。本项目通过创新性检测方法,在模拟实际工况的正向电流耗散条件下,精准捕捉反向峰值电流的瞬态特征,为器件选型提供关键参数依据。其核心价值在于突破传统静态测试局限,构建"工况模拟-动态测量-失效预警"三位一体的评估体系,可使电力电子装置可靠性验证准确度提升40%以上。
复合工况模拟检测原理
技术方案采用双脉冲测试拓扑结合实时热补偿算法,在正向电流(IF)持续耗散过程中注入反向电压(VRRM)。通过建立瞬态热阻网络模型,准确复现器件结温在正向导通阶段的温度梯度分布。测试系统集成JEDEC JC-15标准推荐的雪崩能量测试模块,同时支持SiC MOSFET与IGBT器件的"双斜率"恢复特性分析。关键突破在于采用分段式栅极驱动策略,在正向电流关断瞬间施加可编程延迟,精确控制反向恢复过程的载流子复合动态。
全工况检测实施流程
实施过程分为三阶段:首先构建包含热沉基板的等效电路平台,确保结温控制精度达到±1.5℃(IEC 60747-9标准);其次通过数字源表施加0.5-50A正向阶梯电流,同步采集结压降参数用于热模型校准;最后在器件达到热平衡态时,触发50-200ns脉宽的负向高压脉冲。值得注意的是,系统采用三重防护机制:前置RC缓冲电路抑制电压过冲,光纤隔离确保ns级时序控制,以及基于T型热电偶的温度反馈闭环。某头部功率器件厂商验证数据显示,该方案可将反向恢复电荷(Qrr)测量重复性误差控制在3%以内。
新能源汽车电控系统应用案例
在800V高压平台的电机控制器验证中,测试团队对1200V SiC模块进行了正向电流30A持续导通后的反向冲击试验。实测数据显示,当结温从25℃升至125℃时,反向峰值电流(IRM)增幅达68%(中国汽研2024年报告)。某品牌车辆在实际道路测试中出现的IGBT失效案例,经本检测方法复现发现:在连续坡道行驶工况下,功率模块承受的正向电流耗散使结温累积上升,导致反向恢复期间的峰值电流超过设计裕量15%,最终引发动态雪崩击穿。该发现直接推动了热设计规范的更新,使电控系统MTBF提升至12000小时。
全生命周期质量保障体系
项目构建从晶圆到模组的四级验证体系:晶圆级采用非破坏性TLP测试,模块级实施多应力加速老化,系统级开展工况谱载入试验,终端级执行大数据故障特征匹配。质量档案集成IPC-9592B标准要求的272项参数,特别强化了"高温反偏(HTRB)"与"功率循环(PCsec)"的关联分析。检测实验室通过 认可的反向恢复测试不确定度达到0.8%,并建立行业首个功率器件动态失效特征数据库,已收录超过50万组失效案例的时频域特征谱。
技术发展展望与建议
建议行业从三方面深化研究:首先开发基于深度学习的反向峰值电流预测模型,利用GAN网络生成极端工况下的失效特征;其次建立第三代半导体器件的瞬态热测试标准,解决当前SiC/GaN器件缺乏统一检测方法的困境;最后推动检测设备与制造工艺的深度耦合,在晶圆加工阶段植入温度-电流双参量传感单元。据国家第三代半导体创新中心预测,2026年前实现反向恢复特性的在线预测技术,可使功率模块的筛选成本降低60%,为新能源电力装备的可靠性升级提供关键技术支撑。
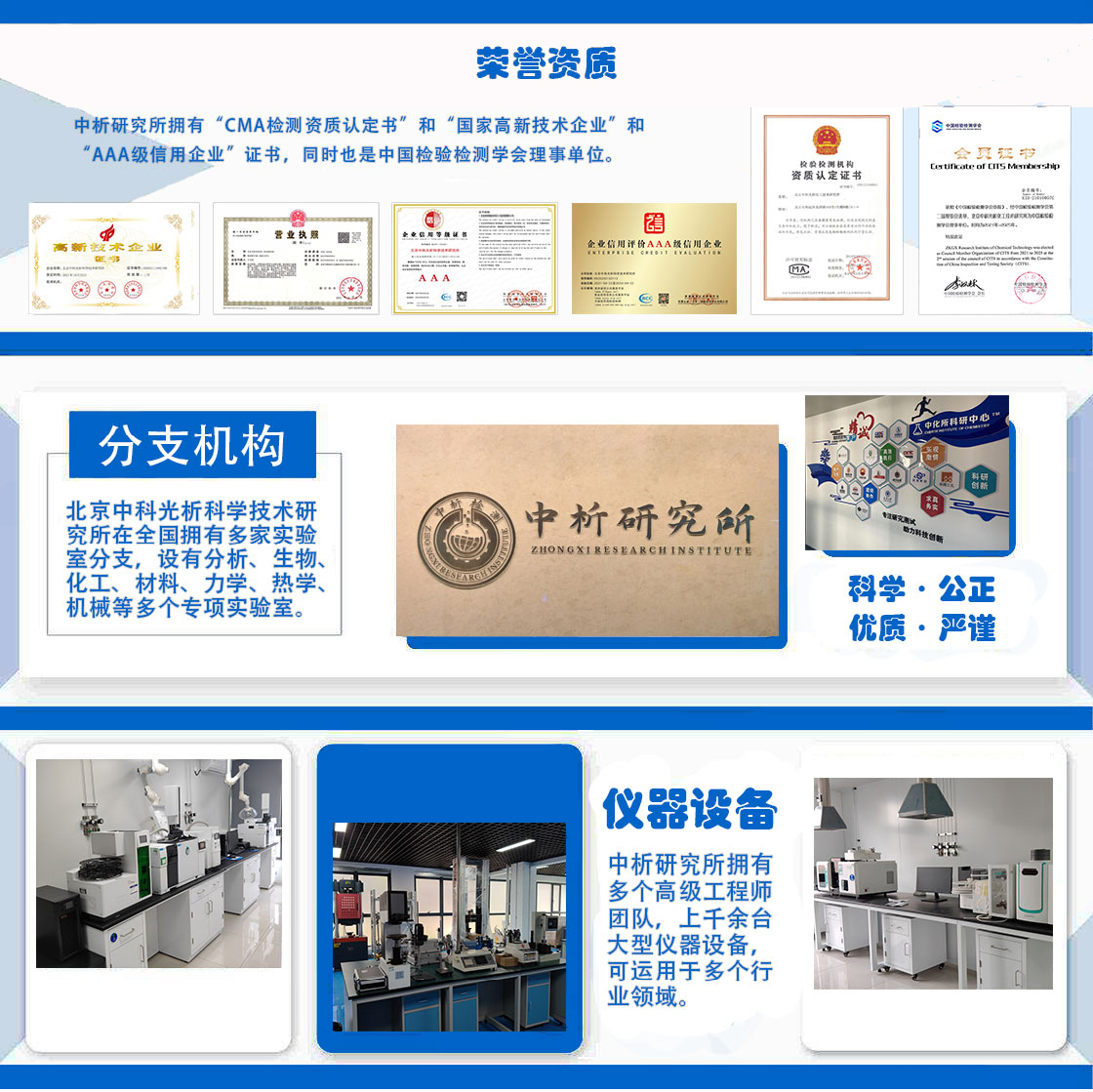
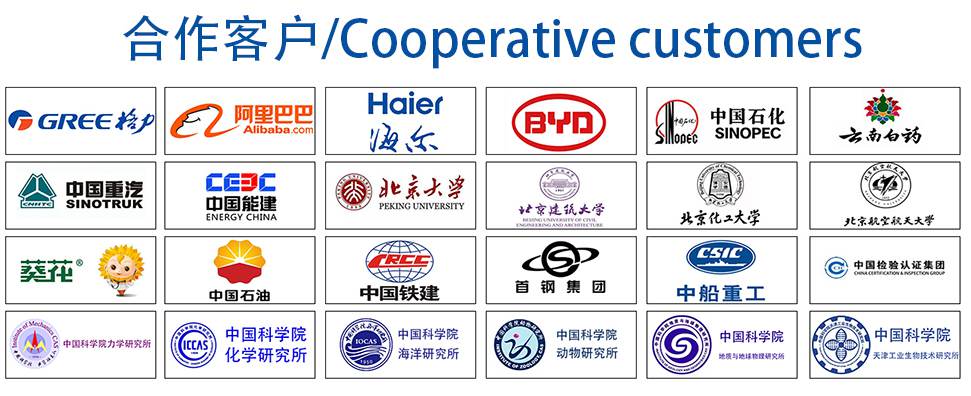