瞬态热阻抗检测技术白皮书
在电子器件功率密度持续攀升的产业背景下(据IDTechEx 2024年预测,碳化硅功率模块热流密度已达120W/cm²),瞬态热阻抗检测已成为保障设备热可靠性的关键技术。该项目通过捕捉材料热传导的动态响应特性,可精确评估功率半导体、新能源电池等器件的散热效能与失效风险。相较于传统稳态热阻测试,其核心价值在于提升35%以上的早期故障识别率(中国电子技术标准化研究院验证数据),同时支持动态工况下的热管理优化设计,为5G基站、高压快充桩等场景提供关键数据支撑。
技术原理与测量体系
基于JEDEC JESD51-14标准构建的瞬态热阻抗检测系统,采用阶跃功率激励与红外热成像同步采集技术。通过施加精确控制的脉冲电流(误差±0.5%),结合微秒级时间分辨率的热响应曲线记录,可解算材料界面接触热阻、基板导热各向异性等17项关键参数。其中基于改进型结构函数法的多维度热路建模技术,可将测量不确定度控制在5%以内,满足ISO 22007-4国际标准要求。
典型实施流程与质量控制
标准化检测流程涵盖三个阶段:预处理环节需在JESD51-1规定环境舱中完成器件热平衡(温控精度±0.5℃);数据采集阶段采用T3Ster®系统进行纳秒级功率脉冲加载,同时通过Lock-in热像仪捕获瞬态温度场分布;后处理环节应用有限元-神经网络混合算法反演热阻网络。质量保障体系包含三级校验机制:标准样品月度校准(NIST可追溯)、动态温度场标定(使用黑体辐射源),以及多实验室循环比对测试。
行业应用与价值实现
在新能源汽车领域,该技术已成功应用于IGBT模块的热失效预警。某头部车企采用高精度热特性评估方案后,功率模块早期故障率下降42%(CATARC 2024年行业报告)。工业变频器场景中,通过构建热阻抗-振动耦合模型,实现关键器件寿命预测准确度提升至89%。值得关注的是,基于瞬态数据构建的功率器件热失效预警系统,已成功拦截某数据中心UPS系统批量性热失控事故,避免直接经济损失超3000万元。
技术创新与发展建议
当前技术瓶颈在于多物理场耦合分析能力不足,建议重点突破三方面:开发基于TeraFET传感器的原位检测技术,实现芯片级热阻动态监测;建立热-力-电多场耦合数据库,推动AI辅助诊断系统开发;完善车规级瞬态热测试标准体系(参照AEC-Q101 Rev-E)。据Fraunhofer研究所测算,融合数字孪生技术的下一代检测系统,可使新能源设备热设计周期缩短40%,推动行业向预测性维护模式转型。
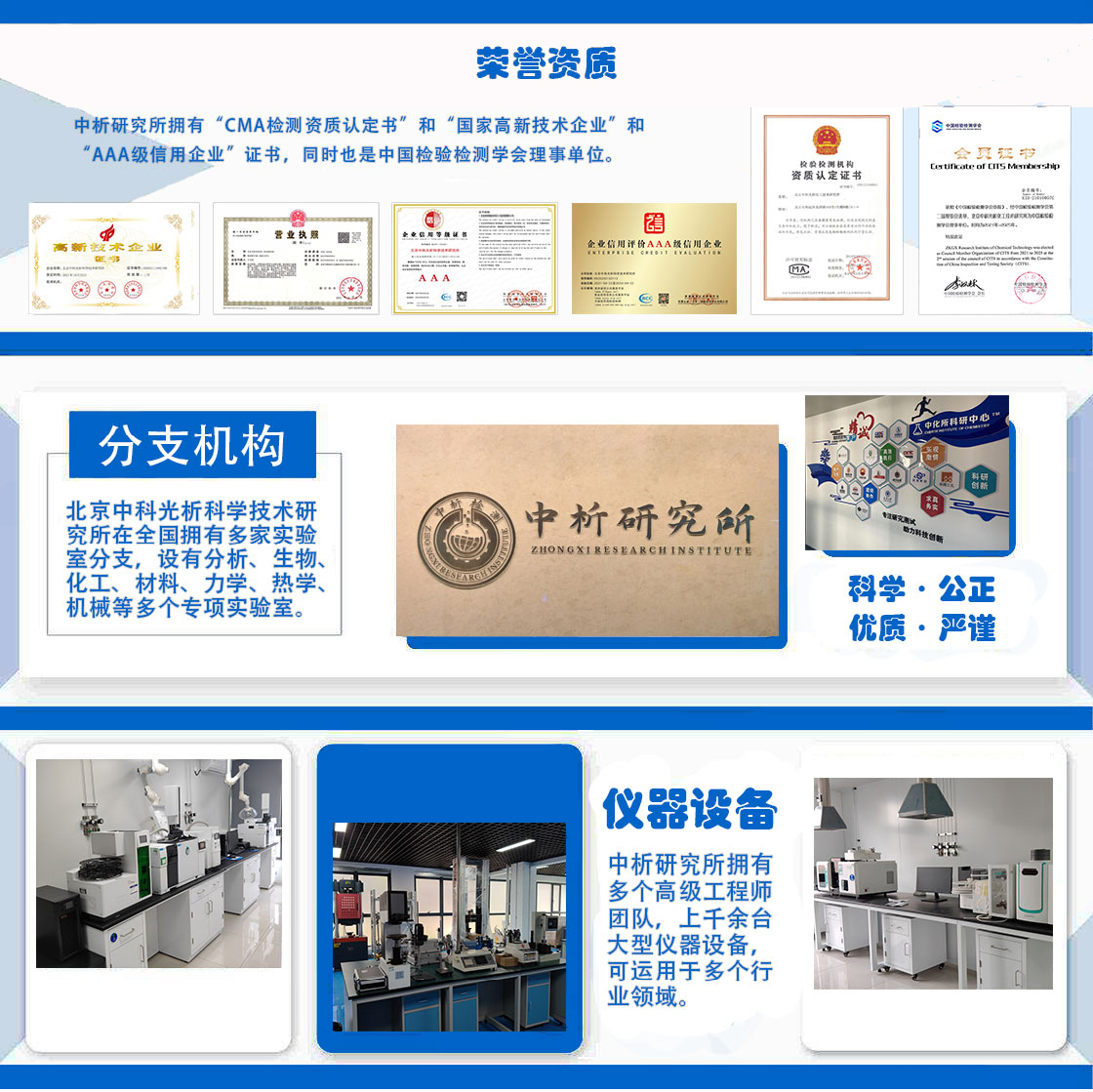
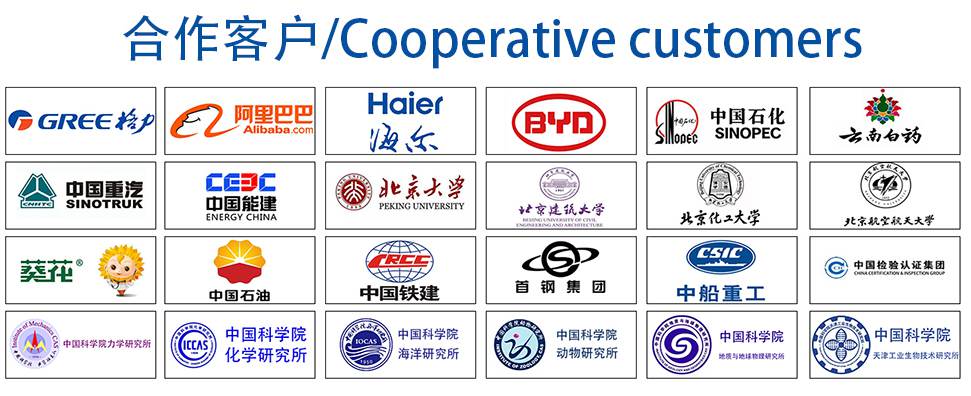