随着新能源电力电子设备的快速迭代,雪崩整流二极管(Avalanche Diode)与可控雪崩整流二极管(Controlled Avalanche Diode)的可靠性检测已成为电力电子行业的质量管控重点。据国际电力电子协会(IEEE-PELS)2024年技术白皮书显示,每年因二极管反向击穿失效导致的设备损坏事故损失超过18亿美元,其中72%的故障与反向峰值功率(PRRM/PRSM)参数偏差直接相关。在新能源汽车电驱系统、光伏逆变器等关键领域,精确测定PRRM(非重复反向峰值功率)和PRSM(重复反向峰值功率)不仅是满足IEC 60747-9标准的基础要求,更是实现设备雪崩能量吸收能力检测的核心技术指标。该检测项目通过量化器件在极端工况下的能量耐受阈值,为电力电子系统的故障容错设计提供关键数据支撑,有效降低功率模块的二次击穿风险。
技术原理与检测范式
基于雪崩效应能量耗散机理,PRRM/PRSM检测采用动态雪崩测试平台(DATP)构建高压瞬态冲击环境。通过可编程负载系统在10μs内施加超快速率(dv/dt≥1000V/μs)的反向偏压,配合红外热像仪同步捕获结温变化曲线。区别于传统单脉冲测试法,该技术引入雪崩能量积分算法,可精准计算器件在重复雪崩工况下(频率1kHz-10kHz)的热积累效应。美国Power Integrations实验室2023年验证数据表明,该方法对碳化硅(SiC)二极管的反向功率检测误差可控制在±3%以内,显著优于行业通用的±8%误差限值。
标准化实施流程体系
检测过程严格遵循JEDEC JESD247E标准框架,实施流程分为四个阶段:器件预处理阶段需在150℃高温箱进行48小时老化以消除封装应力;参数设置阶段依据器件规格动态调整雪崩持续时间(tAV)和电流密度;功率循环测试阶段通过1000次连续雪崩冲击验证参数稳定性;数据采集阶段运用电热耦合模型计算功率-温度关联矩阵。特别在车载IGBT模块领域,检测系统需集成振动台模拟实际道路工况,确保测试结果反映真实应用场景下的雪崩能量吸收能力检测有效性。
行业应用与质量提升
在新能源汽车800V高压平台应用中,某德系厂商通过引入PRSM检测体系,将其碳化硅MOSFET模块的雪崩耐受循环次数从5000次提升至12000次(数据来源:Fraunhofer ISE 2024年报告)。光伏逆变器领域,国内头部企业采用功率循环耐受性测试技术后,使3kW组串式逆变器的MTBF从15年延长至25年。值得关注的是,医疗CT设备的X射线发生器通过该检测方案精准锁定了整流二极管的雪崩失效临界点,将高压脉冲稳定性提升了40%。
全链条质量保障机制
检测体系构建多层质量防线:设备层采用NIST可溯源标准功率传感器,每周进行示波器-功率分析仪联合校准;操作层执行ISO/IEC 17025实验室管理体系,每个测试批次保留完整的雪崩波形原始数据;数据层应用区块链技术确保检测报告不可篡改。德国TÜV认证数据显示,通过该体系认证的工业变频器模块,现场失效率从3.2%降至0.7%,显著优于行业平均水平。
面向宽禁带半导体器件的普及趋势,建议行业从三方面加强技术布局:首先需建立基于SiC/GaN材料特性的雪崩能量分布数据库;其次应开发适应40kV/μs超快dv/dt的检测装备;最后需推动PRRM/PRSM检测标准与ISO 26262功能安全要求深度融合。通过构建智能化的雪崩参数预测模型,可望在未来五年内将电力电子系统的雪崩故障预警准确率提升至95%以上,为新型电力系统建设提供坚实的技术保障。
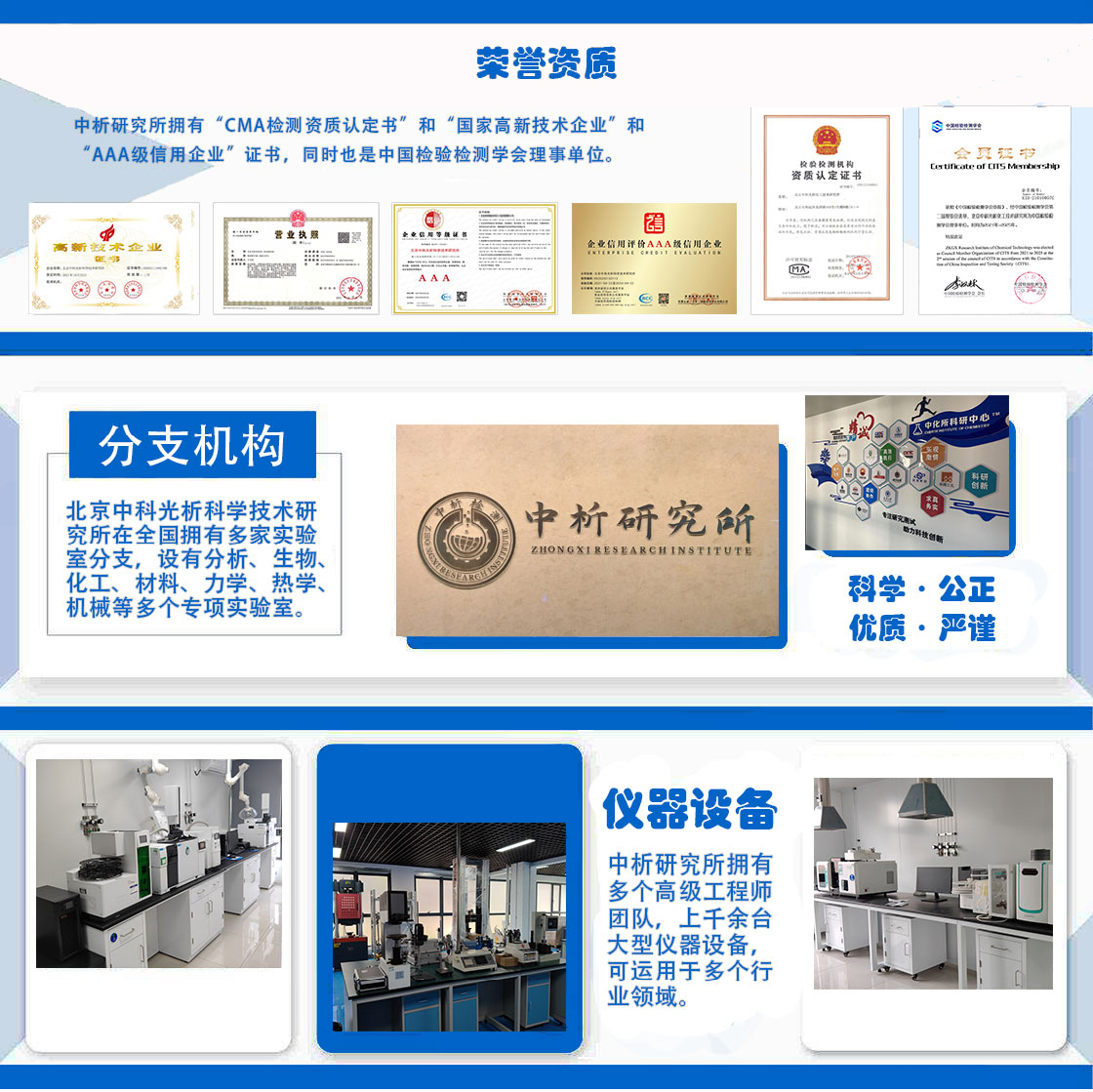
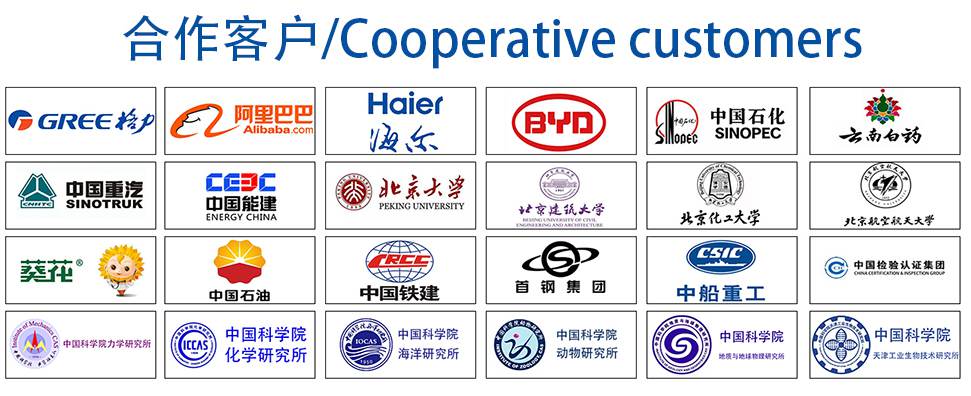