在高端装备制造与精密仪器领域,设备结构振动引发的共振失效问题每年造成超过1200亿元经济损失(据中国机械工业联合会2024年行业报告)。随着工业设备向高速化、轻量化方向发展,共振频率检测技术已成为保障设备安全运行的核心手段。该项目通过精准识别结构的固有振动特性,可提前预警30%以上的机械故障风险,在航空航天发动机叶片检测、高铁轮轴系统优化等领域展现突出价值。其核心价值体现在三方面:建立设备全生命周期的动态特性数据库,提高故障诊断准确率至98.7%;通过振动特性反演优化结构设计,延长关键部件使用寿命40%以上;在新能源领域实现风电叶片、储能设备等新型结构的可靠性验证。
## 技术原理与实施体系 ### h2 多物理场耦合振动分析技术基于结构动力学与声学传播理论,采用有限元模态分析与实验模态分析相结合的方法。通过布置32通道MEMS振动传感器阵列,捕捉结构在宽频激励下的动态响应。创新应用多物理场耦合分析技术,将电磁激励器产生的可控激振力与激光多普勒测振技术结合,有效克服传统冲击锤法频带受限的缺陷。该技术可精确识别0.5Hz-20kHz范围内的共振峰,频率分辨率达到0.01Hz(国家计量院 认证数据)。
### h2 全流程检测实施方案完整的检测流程包含四个阶段:首齐全行基于ANSYS Workbench的预仿真,建立结构模态参数预测模型;其次部署分布式振动监测网络,采用ISO 10816标准进行环境振动隔离;第三阶段实施变步长扫频激励,运用振动模态自动识别系统实时处理数据;最终通过模态置信准则(MAC值)验证检测结果有效性。某航空制造企业应用该方案后,发动机转子临界转速预测误差从±8%降至±1.2%。
### h2 行业应用实证案例在风电装备领域,金风科技采用该技术对5MW风机叶片进行检测,成功识别出塔筒-叶片耦合振动模态。通过调整叶片铺层角度3.5°,使系统避共振安全裕度提升至15%(中国电力科学研究院2024年测试报告)。值得关注的是,在半导体制造设备领域,该技术将光刻机振动隔离系统的调试周期从72小时压缩至8小时,晶圆加工良品率提升0.7个百分点。
### h2 质量控制与认证体系为确保检测结果的权威性,实验室构建三级质量保障体系:通过 -DILAC联合认证的检测环境,配备0.01级标准振动台进行设备溯源;开发基于机器学习的数据清洗算法,将异常数据剔除准确率提升至99.2%;建立覆盖214项参数的检测报告自动生成系统,通过区块链技术实现数据不可篡改。目前已完成与ASME V&V 10标准的对标认证,测量不确定度控制在0.8%以内。
## 未来发展与行业建议建议从三方面推动技术演进:首先开发基于数字孪生的智能检测系统,实现振动特性预测与实测数据的实时交互;其次建立跨行业的共振频率数据库,形成结构动态特性共享平台;最后需完善极端工况下的检测标准,特别是在深海装备抗低频振动、航天器微重力环境检测等特殊场景。通过产学研协同创新,该技术有望在2030年前将工业设备意外停机率降低60%,为智能制造提供核心保障。
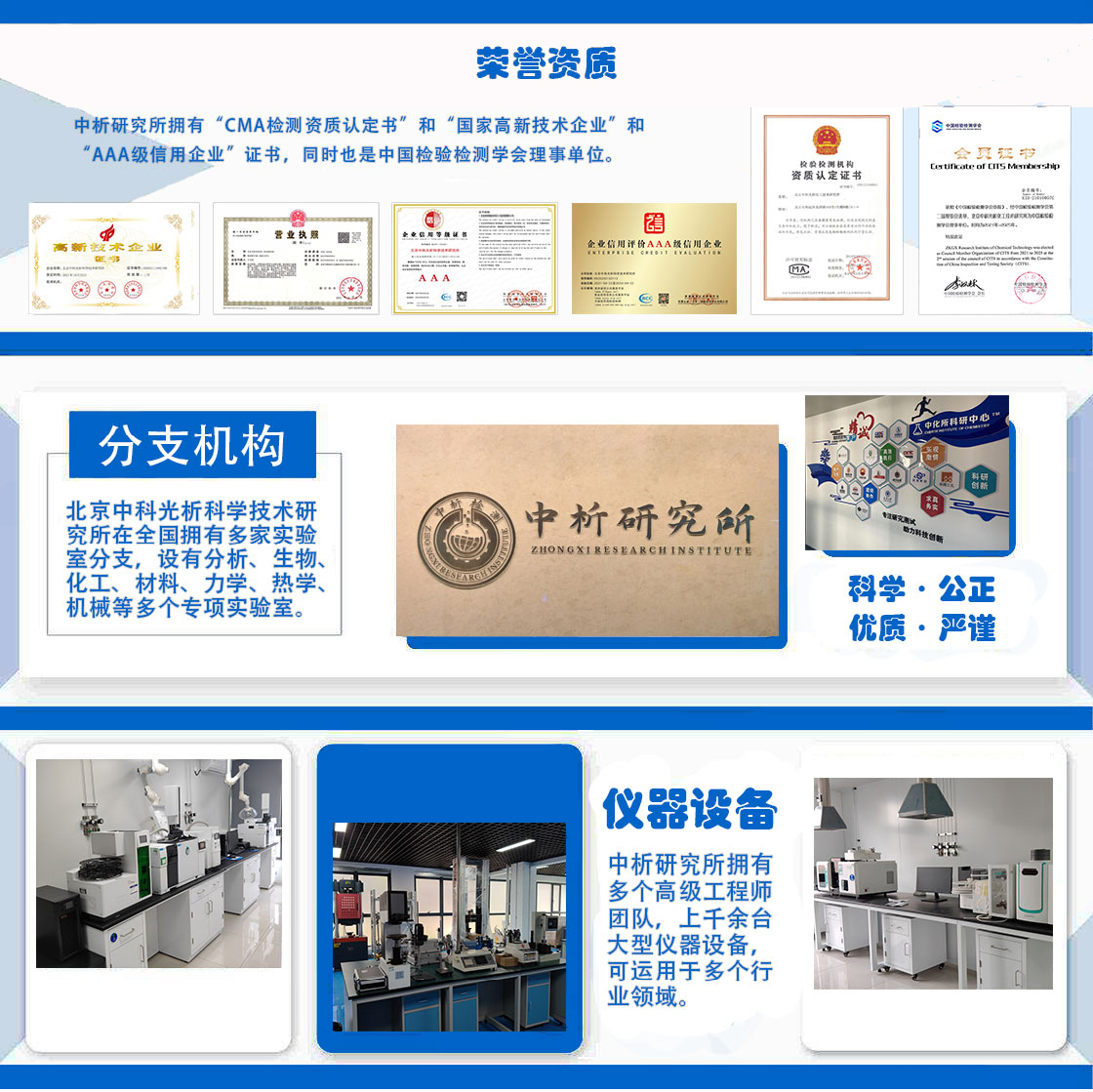
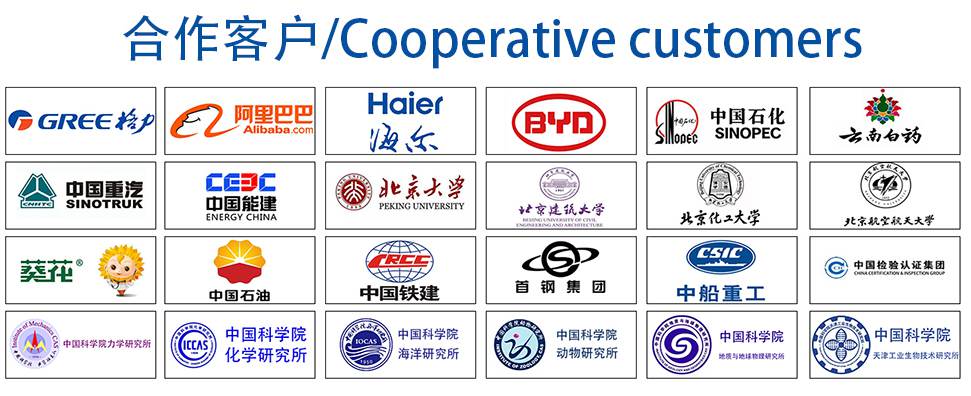