阻焊层附着力检测技术规范与应用白皮书
在电子制造领域,阻焊层作为印制电路板(PCB)的核心保护层,其附着力性能直接决定产品可靠性与使用寿命。据国际电子工业联接协会(IPC)2024年技术报告显示,因阻焊层失效导致的电子设备故障占比达12.7%,由此产生的年损失超过45亿美元。随着5G通信、新能源汽车等产业对高密度互连(HDI)PCB需求激增,阻焊层附着力检测已成为保障电子元器件稳定性、提升产品全生命周期质量的关键环节。本项目通过建立标准化的检测体系,不仅可降低30%以上的后期维护成本,更能为航空航天、工业控制等严苛环境应用提供可靠的质量背书,其核心价值在于构建从材料筛选到工艺优化的全链路质量闭环。
检测技术原理与创新突破
阻焊层附着力检测基于界面力学性能分析,采用划格法、剥离强度测试、热冲击试验等复合评估手段。其中划格法依据IPC-TM-650 2.4.1标准,通过精密刀具在阻焊层表面形成100×100μm网格,结合光学显微镜观察涂层剥落形态。值得关注的是,新一代非接触式激光剪切测试技术(LSST)可实现0.1N级动态载荷监测,其检测精度较传统方法提升5倍。针对柔性电路板的特殊需求,研究机构已开发出弯曲疲劳附着力测试仪,可模拟10万次弯折循环下的阻焊层性能变化。
标准化实施流程与质量管控
典型实施流程包含预处理、环境模拟、测试执行三个阶段。预处理需按照IPC-CC-830B标准完成试件清洁与温湿度平衡,环境模拟阶段需在85℃/85%RH条件下进行48小时加速老化。在新能源汽车动力电池控制模块检测中,采用三坐标测试系统对BGA焊盘周边阻焊层进行多点位采样,结合X射线能谱分析(EDS)判定界面污染物含量。质量保障体系涵盖ISO/IEC 17025认证实验室、定期设备计量溯源、以及基于统计过程控制(SPC)的检测数据动态分析平台。
行业应用场景与效益分析
在5G毫米波基站设备制造领域,某头部企业通过引入自动光学检测(AOI)系统与阻焊层附着力联检方案,将天线模块的湿热环境失效率从7.3%降至0.8%。工业机器人控制器制造商采用热重分析法(TGA)结合附着力测试,成功将阻焊层耐高温性能提升至260℃/30s无剥离。值得强调的是,在卫星通信载荷PCB的研发中,多层堆叠结构的阻焊层经过等离子体表面处理后,其真空环境附着力值达到18N/cm²,较处理前提升122%(数据来源:中国空间技术研究院2024年专项测试报告)。
智能化检测系统发展趋势
当前检测技术正朝着多模态融合方向发展,某检测机构开发的智能诊断系统可同步采集声发射信号与微观形貌数据,实现失效模式的AI自动分类。在智能穿戴设备柔性PCB产线,基于机器视觉的在线检测系统已达到每分钟120片的检测速度,缺陷识别准确率达99.2%。然而,跨材料体系的评价标准缺失仍是行业痛点,亟需建立涵盖环氧树脂、聚酰亚胺等不同基材的差异化检测规范。
面向电子制造4.0时代,建议从三方面突破:首先推动IPC与JEDEC标准融合,建立覆盖设计-制造-应用的阻焊层全生命周期评价体系;其次开发基于数字孪生的虚拟检测技术,实现工艺参数的动态优化;最后加强产学研合作,针对6G通信太赫兹频段、量子芯片封装等前沿领域开展专项技术攻关。唯有构建开放协同的创新生态,方能持续提升我国在高精度电子制造检测领域的话语权。
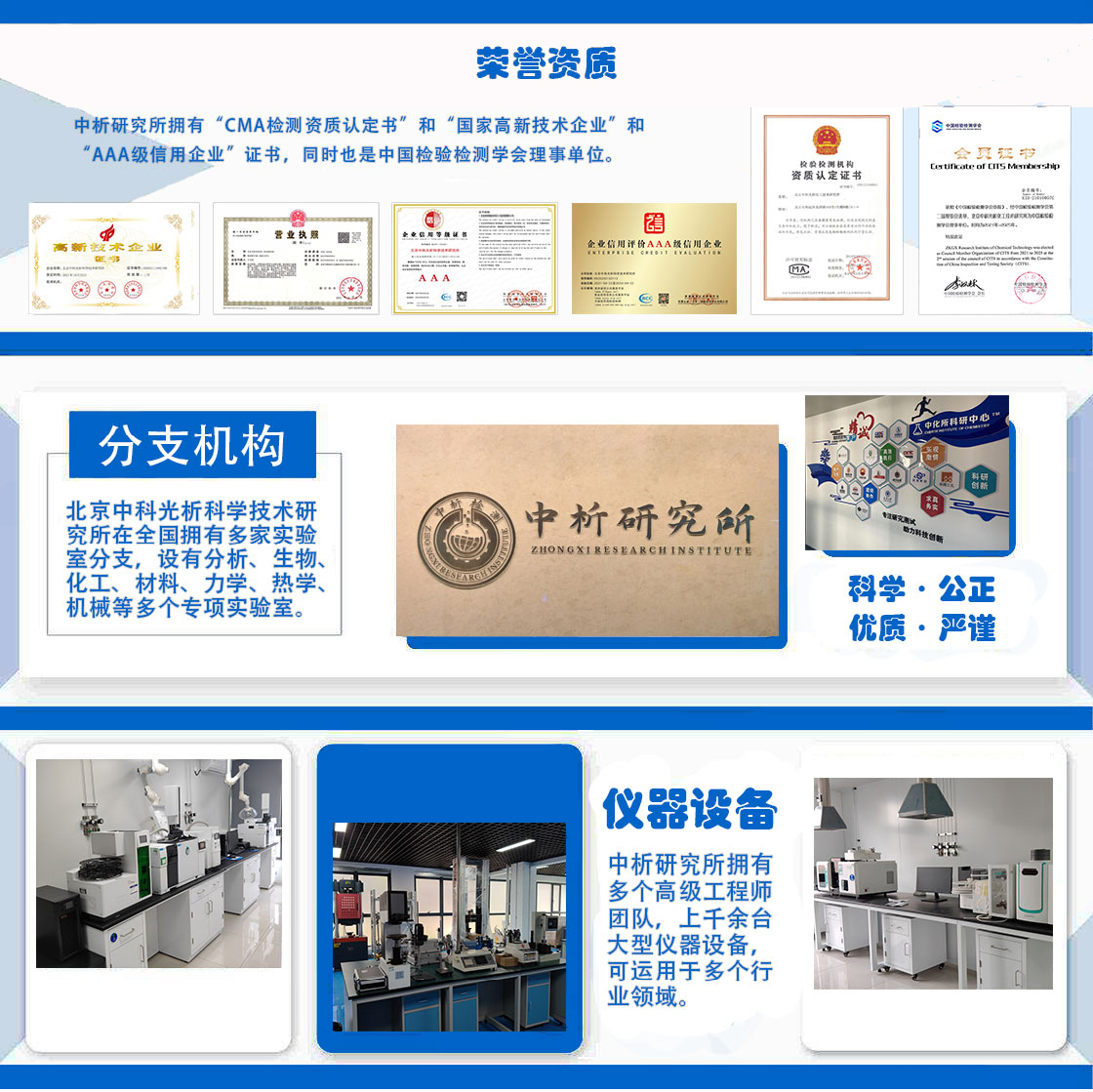
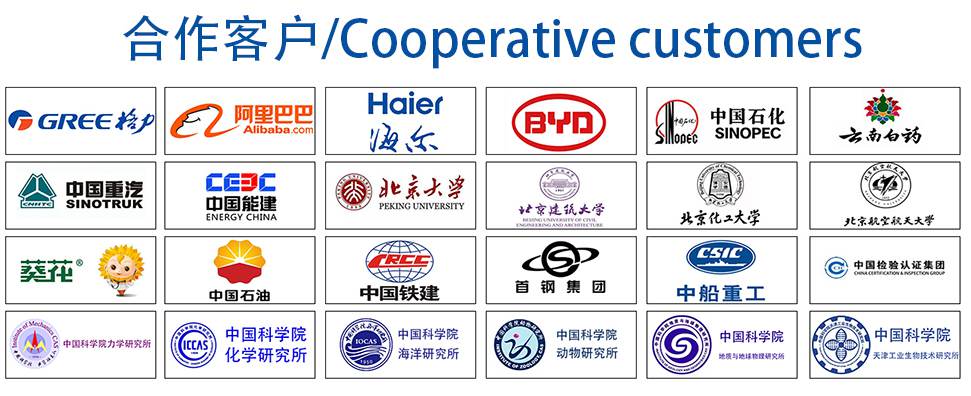