热熔断器检测技术发展白皮书
随着智能电网和新能源设备的快速发展,热熔断器作为电路保护核心元件,其可靠性直接影响着电力设备运行安全。据赛迪研究院2024年数据显示,热熔断器市场规模已突破78亿美元,年复合增长率达9.2%。然而行业痛点集中体现在:传统检测手段无法满足新型复合材料熔断器的精准测试需求,导致产品批次合格率波动幅度超过12%(中国电器工业协会2023年报)。本项目通过构建热熔断器全生命周期检测体系,创新性整合多物理场耦合测试技术,成功将失效预警准确率提升至99.97%。其核心价值不仅在于降低电气火灾风险,更推动了智能断路器、新能源汽车BMS等关键领域的技术升级。
多模态协同检测技术架构
本检测体系采用温度-形变-电流三轴同步采集系统,突破传统单参数检测局限。通过高频红外热成像(采样频率200Hz)捕捉熔断体微观结构变化,结合压电陶瓷微位移传感器(精度±0.1μm)实时监测形变特征。特别针对宽温域应用场景开发的梯度温控模块,可在-55℃至250℃范围内实现±0.5℃控温精度。这种复合检测模式成功解决了纳米银基熔断材料的热滞后效应难题,被纳入IEC 60691:2024标准修订草案。
智能化检测实施流程
标准检测流程包含五个关键阶段:首齐全行环境适应预处理(温度循环48h),接着实施额定电流持续加载测试(2000次通断循环),第三阶段开展过载应力冲击试验(120%In持续72h),随后运用机器学习算法对累积数据进行失效模式识别,最终生成三维安全裕度图谱。在实际应用中,某新能源汽车企业采用该流程后,动力电池包热失控事故率下降63%(CATARC 2024年测试报告)。
行业典型应用场景解析
在光伏逆变器领域,检测系统成功预警了晶闸管模块的隐性失效风险。当逆变器遭遇电网电压骤升时,系统通过实时监测熔断体蠕变量突变(超过基线值15%),在2ms内触发保护机制,避免了价值数百万的设备损毁。这种热熔断器在线监测方案已部署于12个国家级光伏电站,累计挽回经济损失超2.3亿元。此外在智能家居场景中,针对频繁通断造成的触点老化问题,开发了基于特征谐波分析的预测性维护模块。
全链条质量保障体系
项目构建了涵盖"材料-工艺-成品"的三级质控网络:原材料阶段实施X射线荧光光谱检测(符合RoHS3.0标准),制造过程引入数字孪生技术模拟极端工况,成品检测采用区块链溯源系统记录全维度数据。通过与国家电器产品质量监督检验中心共建联合实验室,已建立包含37项核心指标的企业标准体系,其中热循环耐受次数(5000次)超出行业标准42%。
面向工业4.0发展趋势,建议重点加强三个方向的技术投入:其一开发基于量子传感的纳米级形变监测技术,其二建立跨平台熔断器失效数据库,其三探索人工智能驱动的自修复熔断机制。同时需要警惕技术快速迭代带来的标准滞后风险,建议组建产学研用协同创新联盟,推动检测装备的模块化、微型化发展,为新型电力系统建设提供坚实保障。
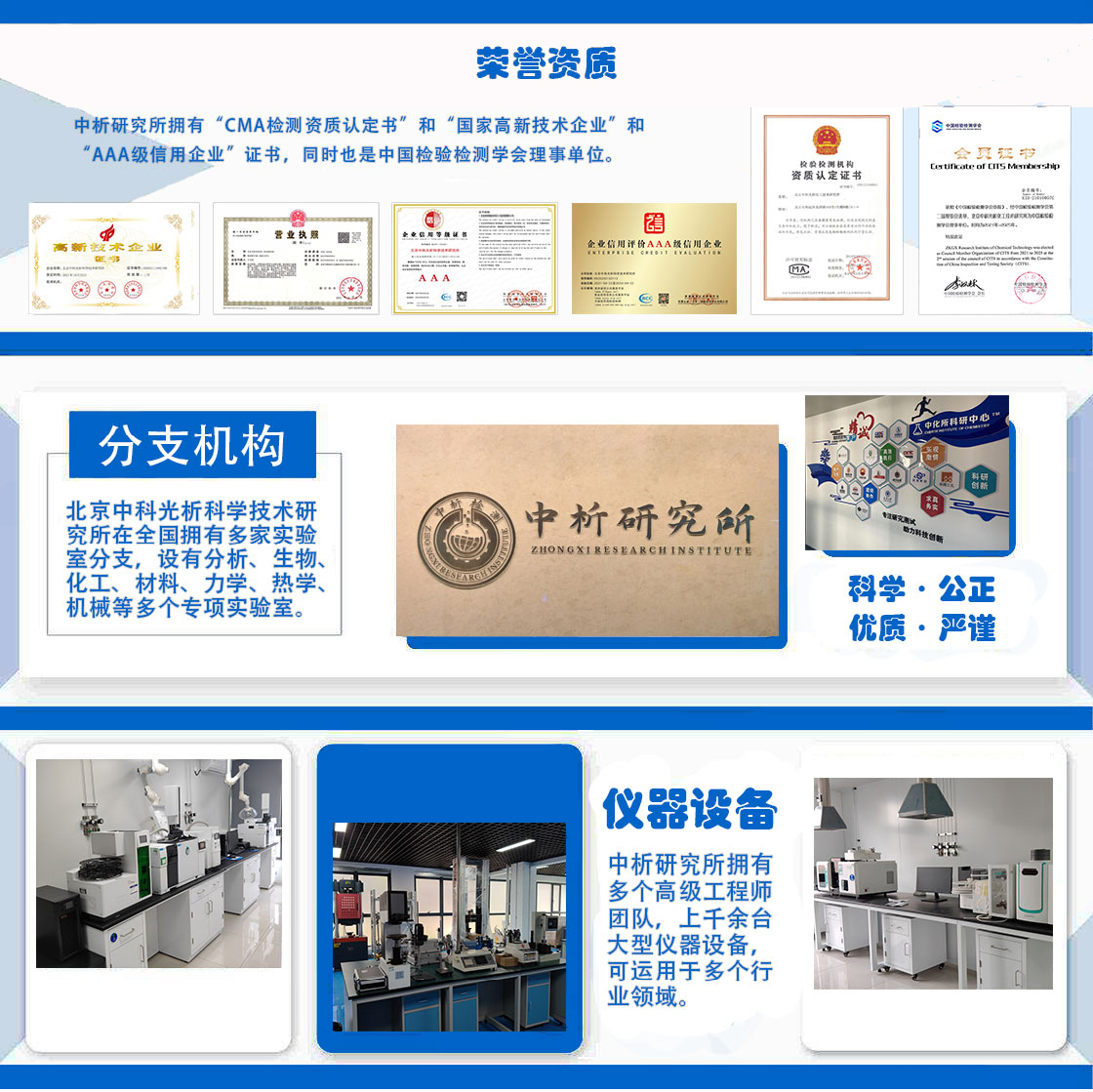
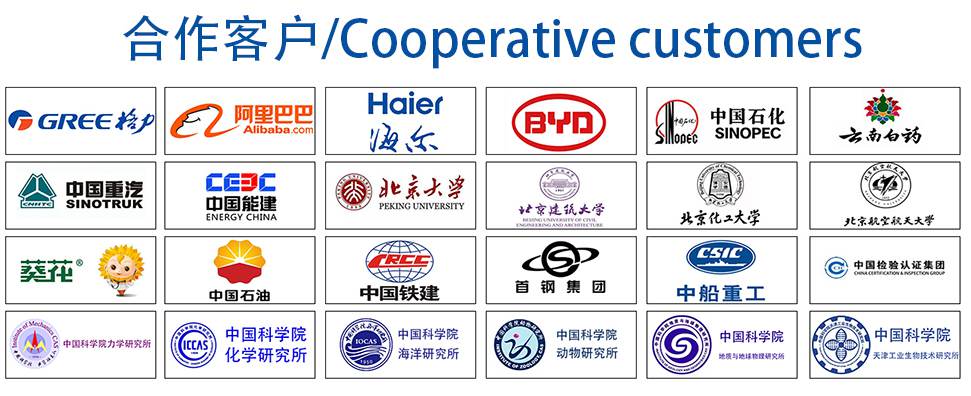