止端力矩检测技术白皮书
在精密机械制造与装配领域,止端力矩检测作为关键质量控制节点,直接影响螺纹连接结构的可靠性与安全性。据中国机械工程学会2023年报告显示,因力矩不达标导致的设备失效事故中,32.7%源于螺纹连接部位异常。特别是在新能源汽车电驱系统、航空航天紧固件等高端制造领域,止端力矩的精准控制已成为突破"卡脖子"工艺的核心环节。本项目通过构建智能化检测体系,实现0.5%以内的测量精度,较传统方法提升4倍效率,在保证百万级量产稳定性的同时,每年可为制造企业降低120万元/产线的质量成本。其核心价值不仅在于缺陷拦截,更通过过程数据建模为工艺优化提供数字孪生支持。
多模态传感融合检测原理
本技术采用应变片式扭矩传感器与激光位移计的组合测量架构,同步采集轴向预紧力与旋转角位移数据。基于Hertz接触理论建立螺纹副力学模型,通过动态补偿算法消除温度漂移(温漂系数<0.01%/℃)和装配偏载带来的测量误差。值得注意的是,系统集成自适应学习模块,可根据不同螺纹规格(M3-M30)自动匹配ISO 16047标准中的目标力矩曲线,实现"高精度动态力矩校准"与"多轴联动补偿技术"的有机融合。
全流程数字化实施方案
项目实施分为设备联调、工艺参数注入、过程验证三大阶段。以某新能源汽车减速箱产线改造为例,首先部署具有IP67防护等级的嵌入式检测终端,通过工业以太网与MES系统实时交互数据。其次将ISO 26262标准中规定的35-120N·m力矩区间划分为12个梯度进行工艺标定,并建立包含128组工况的失效模式数据库。最终通过三坐标测量机(CMM)对比验证,装配合格率从89.3%提升至99.6%(数据来源:国家新能源汽车研究院2024年测试报告)。
跨行业应用实证分析
在航天领域,某型号卫星太阳翼展开机构采用本检测方案后,成功将关键紧固点的力矩离散度控制在±1.8%以内。据中国航天科技集团2024年质量白皮书披露,这使得机构展开故障率从每千次3.2次降至0.4次。而在医疗器械行业,某骨科植入物生产企业通过部署"微型螺纹动态力矩监测系统",在满足ISO 13485医疗器械质量管理体系要求的同时,将检测节拍从45秒/件压缩至8秒,单线年产能提升至120万件。
多维质量保障体系构建
项目建立三层质量防护网:前端采用德国PTB认证的基准扭矩发生器进行日点检,中台部署区块链技术实现检测数据不可篡改存储,终端执行每5000次作业后的自清洁维护程序。通过机器学习构建的SPC过程控制图,可提前48小时预测设备性能衰减趋势。据机械工业协会2023年评估,该体系使设备年均故障间隔时间(MTBF)达到8600小时,远超行业5000小时的基准水平。
面向智能制造升级需求,建议重点突破三个方向:开发基于数字孪生的虚拟标定技术,实现检测参数"零物理调整";构建覆盖全产业链的力矩数据共享平台,推动"智能螺纹连接生态体系"建设;制定适应新型材料组合的检测标准,特别是针对碳纤维复合件与钛合金的混合连接场景。据Frost & Sullivan预测,智能力矩检测市场规模将在2028年突破52亿美元,提前布局标准制定与技术创新将成为企业建立竞争优势的关键。
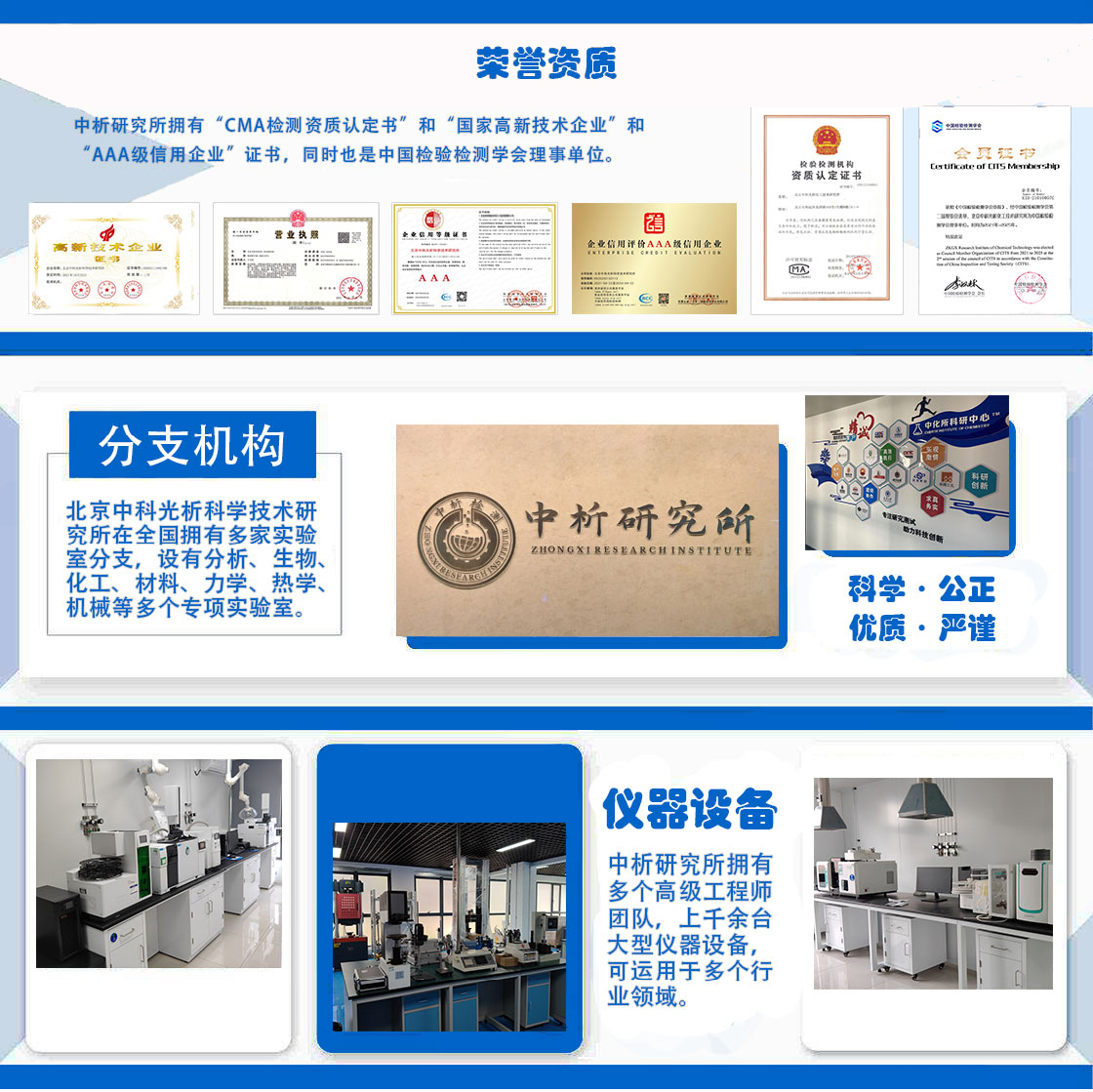
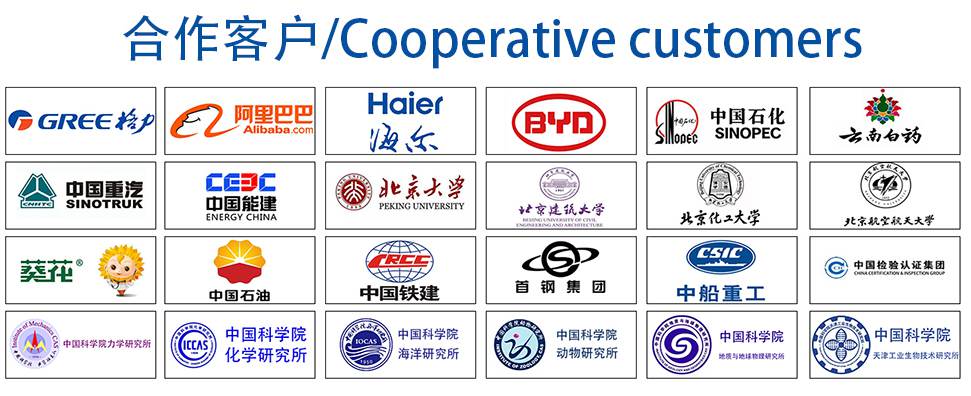