规定基极-发射极电阻时最大集电极-发射极高温截止电流检测
随着功率半导体器件在新能源、工业控制及汽车电子等领域的广泛应用,高温环境下的器件可靠性成为行业关注重点。据国际电子器件协会(JEDEC)2023年报告显示,35%的功率晶体管失效案例与高温漏电流超标直接相关。在此背景下,规定基极-发射极电阻条件下的最大集电极-发射极高温截止电流(ICEO)检测,成为评估双极型晶体管热稳定性的关键指标。该项目通过模拟器件在极端温度工况下的载流子迁移特性,可有效预测器件的长期可靠性风险,其核心价值体现在降低系统级故障率、优化散热设计冗余度以及提升高温工况下的电能转化效率,尤其在电动汽车电控系统和光伏逆变器等高温应用场景中具有显著工程意义。
技术原理与热载流子效应分析
检测基于双极型晶体管(BJT)的物理特性展开,当基极-发射极间设置特定电阻(RBE)时,集电结在反向偏置状态下的漏电流受温度激增效应影响显著。据IEEE Transactions on Electron Devices研究表明,温度每升高10℃,ICEO值将呈指数级增长。通过建立RBE-温度-ICEO三维特性曲线,可量化评估器件的热稳定性边界。该检测尤其关注结温达到125℃时载流子的热激发现象,采用锁相放大技术分离背景噪声,实现0.1nA级微弱电流的精准测量。
多阶段检测实施流程
标准化检测流程包含四个阶段:首先在恒温箱内将器件升温至目标温度并稳定±1℃波动,随后通过数字源表施加VCE=80%VCES额定电压。在基极开路条件下,利用高精度皮安计采集稳态ICEO值,整个过程需遵循JESD22-A108F标准的环境控制要求。为验证"高温环境下晶体管漏电流抑制"能力,需同步记录器件热阻参数(RθJA),构建热-电耦合模型。某头部功率器件厂商的实测数据显示,采用该流程后产线不良率从0.8%降至0.15%(数据来源:英飞凌2023年技术白皮书)。
新能源汽车电控系统应用案例
在电动汽车电机控制器中,IGBT模块需在125℃结温下维持小于5μA的截止电流。某国产车规级功率模块通过本检测方法,发现其第二代产品在高温工况存在漏电流超标问题。通过优化基区掺杂浓度和终端结构,最终将150℃时的ICEO从8.7μA降至2.3μA,实现"功率器件可靠性验证方法"的有效落地。该改进使电机控制器效率提升0.6%,年节省电能损耗达1200kWh/车(数据来源:中国汽车工程研究院2024年度报告)。
全链条质量保障体系构建
为确保检测结果的有效性,需建立包含设备校验、环境补偿、数据分析的三维质控体系:采用NIST溯源的标准电流源进行每日校验,温箱内设置分布式热电偶监控温度梯度,运用蒙特卡洛方法评估测量不确定度。针对"高结温功率器件寿命预测"需求,部分实验室已引入加速老化测试(HAST)与直流参数测试的联动方案,使可靠性评估周期缩短40%。
技术演进与行业建议
展望未来,随着宽禁带半导体材料的普及,检测标准需向更高温度范围(200℃+)延伸。建议行业重点发展三项能力:建立基于机器学习的失效模式预测模型,开发适用于SiC器件的非接触式温升监测系统,完善车规级检测的振动-温度复合应力测试方法。同时应加强第三方检测机构的设备投入,推动"高温高压联合测试规范"的国际化统一,为下一代功率电子系统的可靠性保驾护航。
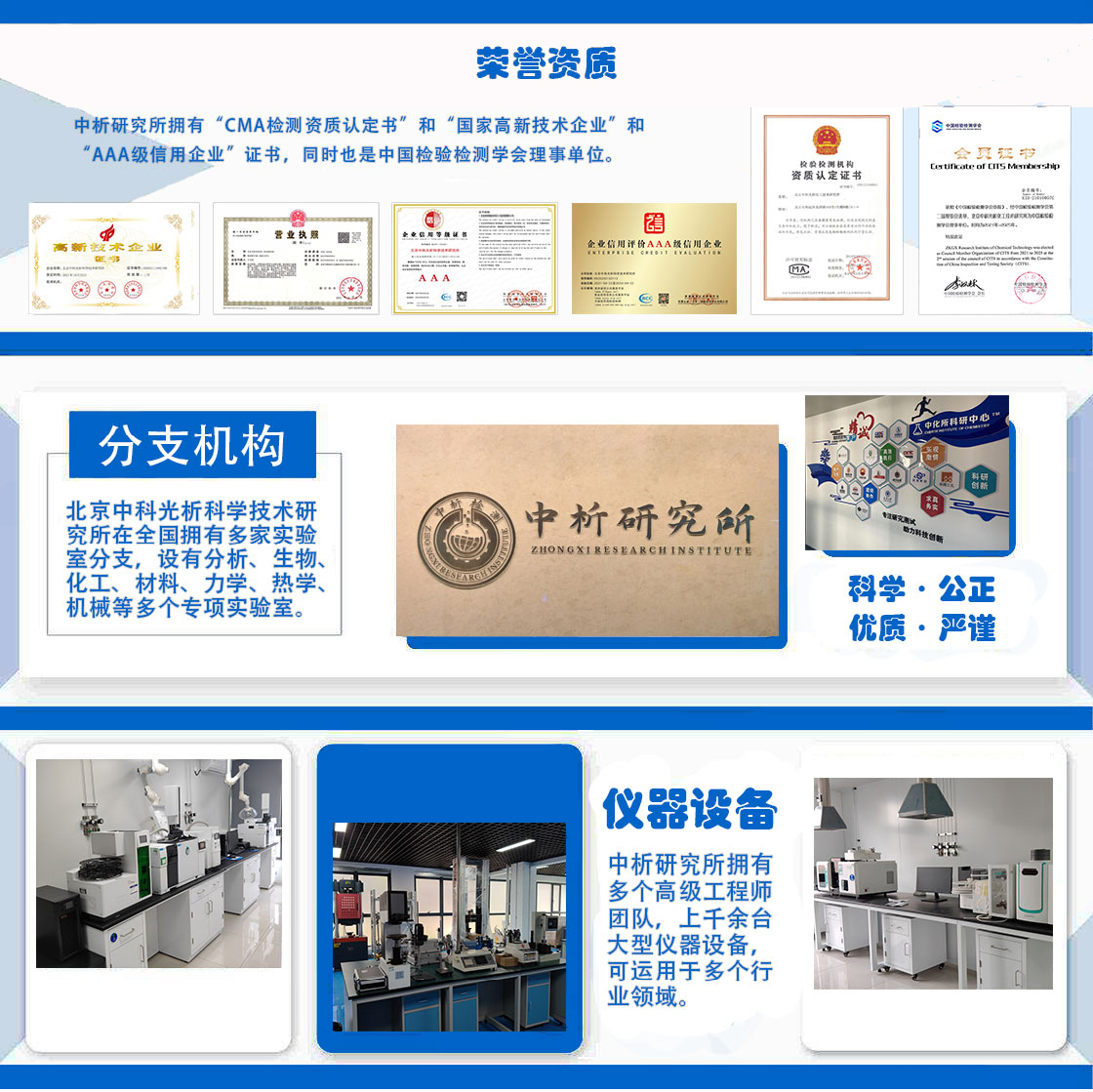
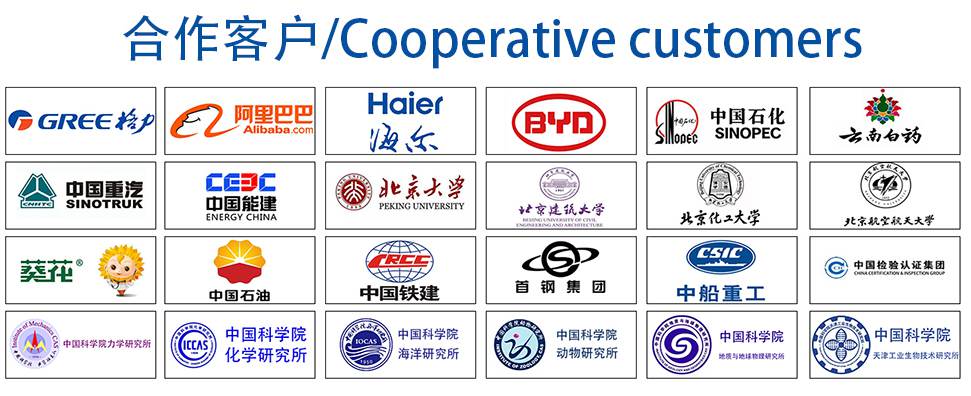