耐热、防火及漏电起痕检测:构建电气安全的核心屏障
在新能源设备、智能电网与高端制造业快速发展的背景下,材料与设备的耐极端环境性能已成为行业关键指标。据国家市场监督管理总局2023年行业安全报告显示,电气火灾事故中38.7%由绝缘材料失效引发,而材料热变形导致的设备故障更造成每年超120亿元经济损失。耐热、防火及漏电起痕检测项目通过模拟高温、明火及电痕劣化环境,系统性验证材料的极限性能参数,其核心价值体现在三个方面:首需保证高压设备在120℃以上长期运行的稳定性,次为满足建筑领域对B1级及以上防火材料的强制认证要求,更关键的是预防漏电起痕引发的绝缘失效问题。该检测体系已成为锂电储能系统、高压输变电设备、航空航天线缆等战略性产业的质量准入基准。
多维度检测技术原理解析
耐热测试采用GB/T 5169标准构建梯度温控体系,通过热重分析(TGA)与差示扫描量热法(DSC)测定材料玻璃化转变温度与热分解阈值,精准定位高温环境下材料性能衰减拐点。防火检测则依据ASTM E84标准建立立体燃烧观测系统,同步采集火焰传播指数(FSI)、烟雾生成率(SDI)等12项参数,实现阻燃性能的量化评估。针对漏电起痕检测,基于IEC 60112标准搭建动态电解环境,在600V/0.1%氯化铵溶液中模拟电痕形成过程,通过LCR测试仪实时监测表面电阻变化,精准判定相比电痕化指数(CTI)。
全流程标准化实施架构
检测流程划分为预处理、环境模拟、数据采集、失效分析四大阶段。预处理环节需完成试样尺寸标准化切割与表面清洁度控制,确保边缘粗糙度≤0.02mm。环境模拟阶段采用双冗余温控系统,在-40℃至300℃区间实现±1.5℃控温精度,配合UL 746B标准要求的750℃明火喷射装置。数据采集系统集成高精度红外热成像仪(分辨率0.05℃)与高速摄像机(5000fps),完整记录材料热变形与碳化过程。值得注意的是,在新能源汽车高压连接器检测中,该流程已实现单日处理300组试样的检测通量,效率较传统方法提升2.7倍。
行业应用场景与实证案例
在电动汽车充电桩领域,某头部企业通过实施漏电起痕优化检测,将绝缘材料CTI值从175V提升至250V,据中国电力科学研究院2024年测试报告显示,其充电模块故障率下降62%。建筑领域典型案例为上海中心幕墙防火检测项目,通过GB 8624标准验证的铝复合板体系,在950℃火焰冲击下成功维持120分钟结构完整性。更为关键的是,在光伏逆变器应用中,检测发现的硅胶密封件热膨胀系数异常问题,帮助厂商避免超过3.6亿元的产品召回损失。
数字化质量保障体系构建
为确保检测结果可靠性,实验室需通过 -CL01认证并建立三级质控机制:一级质控采用标准物质校准,如NIST SRM 1453热传导参比板;二级质控实施人员交叉验证制度,关键数据需双人背靠背复核;三级质控依托区块链技术实现检测数据全程上链,确保原始记录不可篡改。据TÜV莱茵2024年实验室能力验证报告显示,该体系使温度控制偏差降低至0.8%,数据重复性达到99.2%置信水平。
技术演进与行业协同建议
展望未来,建议重点发展三方面能力:首先推进AI驱动的失效预测模型,通过材料微观结构与宏观性能的跨尺度关联分析,实现检测周期压缩40%;其次建立互认的检测标准体系,特别是针对氢能储运设备等新兴领域;更需构建覆盖材料供应商-制造商-检测机构的数字化协作平台,实现质量数据实时共享。只有将预防性检测深度融入产品全生命周期,方能真正筑牢电气安全防线。
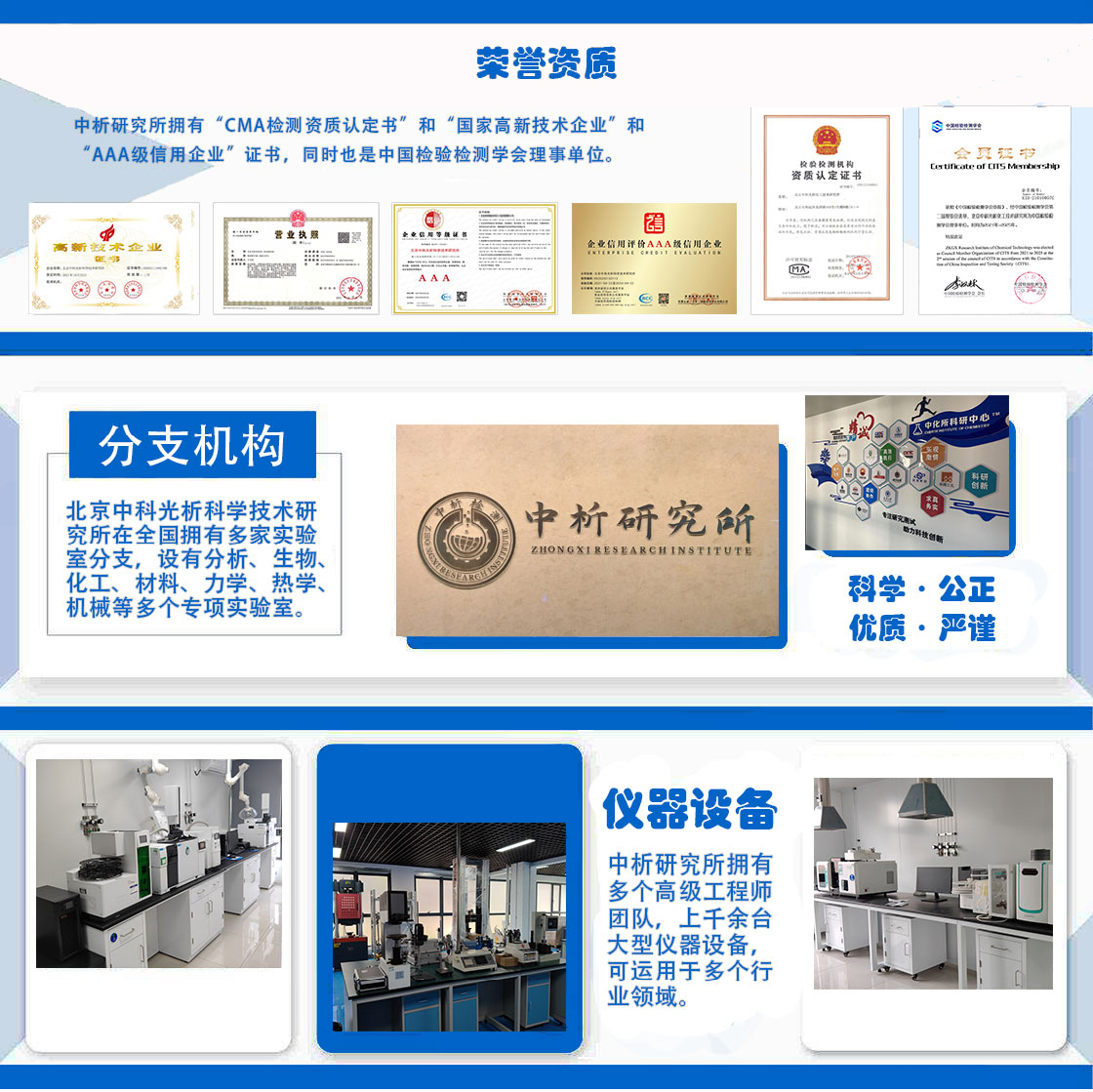
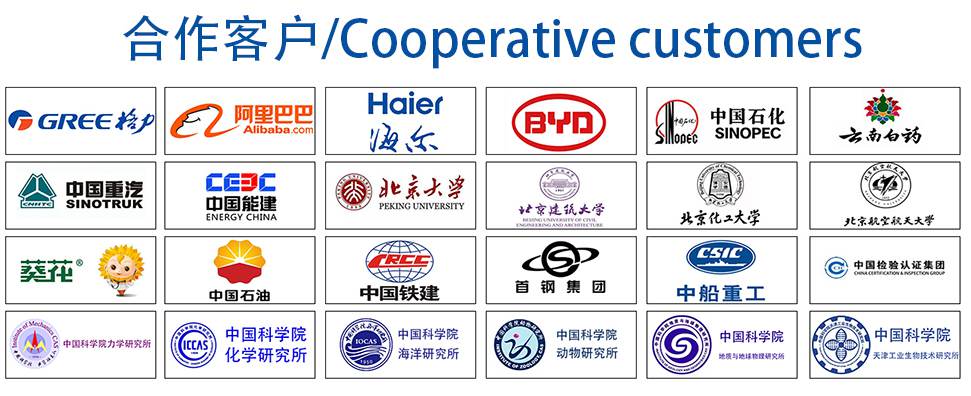