控制极不触发电压检测技术指南
一、概述
二、核心检测项目
1. 静态参数检测
-
- 测试条件:常温(25℃±3℃)、额定反向电压下。
- 方法:逐步升高控制极电压,直至器件导通,记录临界值。
- 判定标准:实测值需高于规格书标称值的20%以上。
-
- 测试点:控制极与阴极/发射极间。
- 设备:高精度微安表(分辨率≤1μA)。
- 要求:漏电流应<10μA(典型值为1-5μA)。
2. 动态参数检测
- 脉冲电压耐受测试
- 输入波形:施加高频脉冲(如1kHz方波,脉宽50μs)。
- 目的:验证器件在瞬态干扰下的抗触发能力。
- 标准:连续1000次脉冲后,不触发电压降幅≤5%。
3. 环境适应性检测
-
- 范围:-40℃至+125℃(按器件等级调整)。
- 流程:温度箱内循环10次,每次停留30分钟。
- 判定:高温/低温极端条件下,GNTV波动<±3%。
-
- 条件:85%相对湿度、85℃环境,持续96小时。
- 检测项:绝缘电阻下降率≤20%。
4. 可靠性测试
- 长时间耐压测试
- 方法:施加80%额定GNTV,持续1000小时。
- 失效标准:出现≥1次误触发即视为不合格。
5. 安全性能检测
- 绝缘耐压测试
- 电压等级:AC 2500V(50Hz),持续1分钟。
- 泄漏电流限值:≤1mA。
6. 失效模式分析(FMA)
- 常见故障:
- 控制极氧化层击穿(需SEM显微分析)
- 封装漏气导致湿度敏感失效(氦质谱检漏)
三、检测设备配置
设备类型 | 规格要求 | 典型型号示例 |
---|---|---|
高压直流电源 | 0-1000V, 精度±0.1% | Keysight N6705C |
示波器 | 带宽≥200MHz, 采样率2GSa/s | Tektronix MSO64 |
高低温试验箱 | -70℃至+180℃, 均匀度±1.5℃ | ESPEC SH-641 |
绝缘测试仪 | 0-5kV, 分辨率0.1MΩ | Megger MIT430 |
四、注意事项
- 安全防护:高压测试需使用屏蔽舱,操作者穿戴绝缘装备。
- 校准要求:所有仪表需通过ISO 17025认证实验室年度校准。
- 器件差异:晶闸管与IGBT的GNTV检测阈值相差3-5倍,需严格区分测试规程。
五、典型应用案例
- 问题:车辆启停时误触发导致过电流。
- 解决方案:
- 优化GNTV检测范围(从15V提升至22V)
- 增加脉冲群抗扰度测试(IEC 61000-4-4 Level 4)
- 成果:故障率下降92%,MTBF提升至10万小时。
六、总结
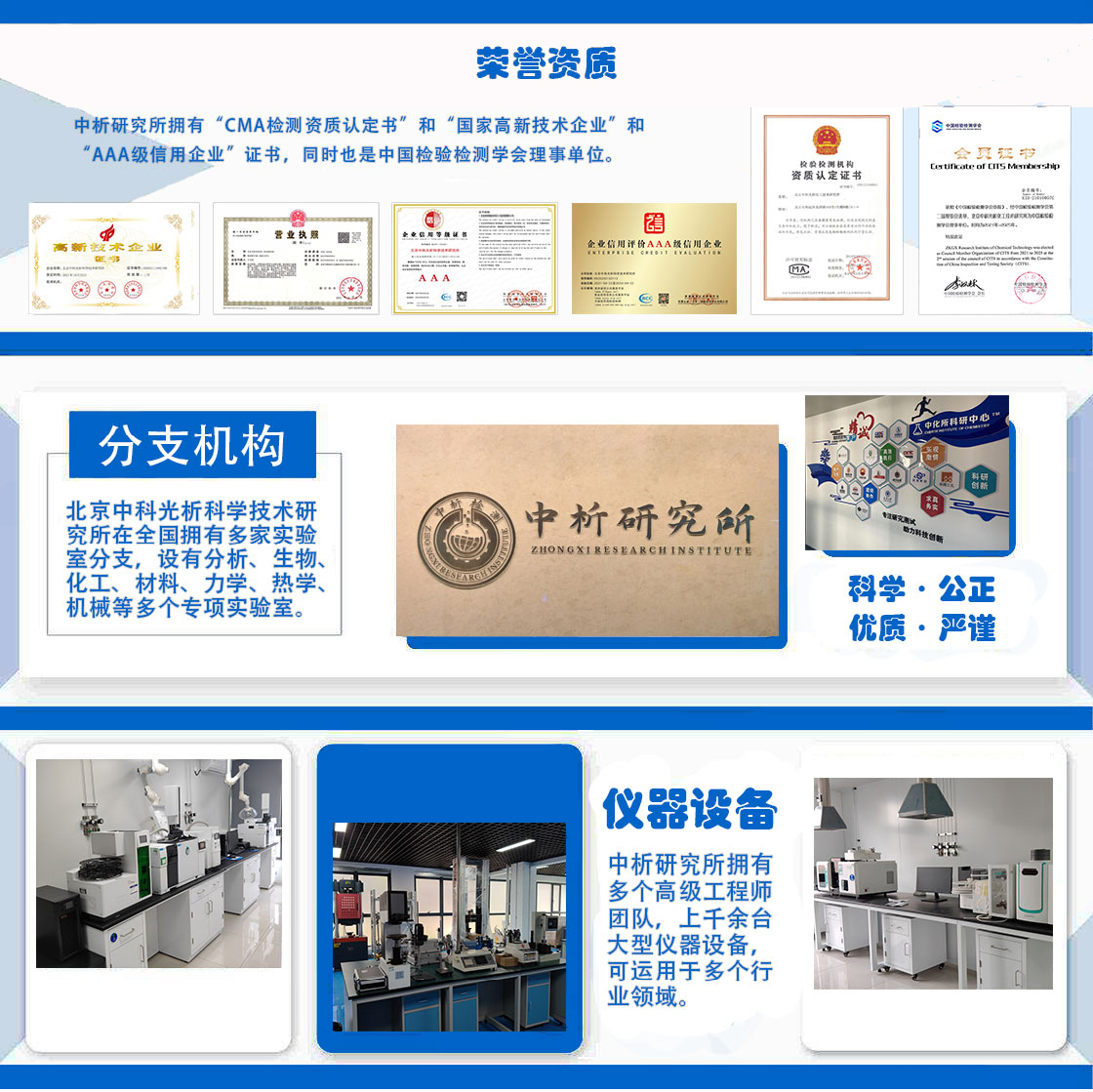
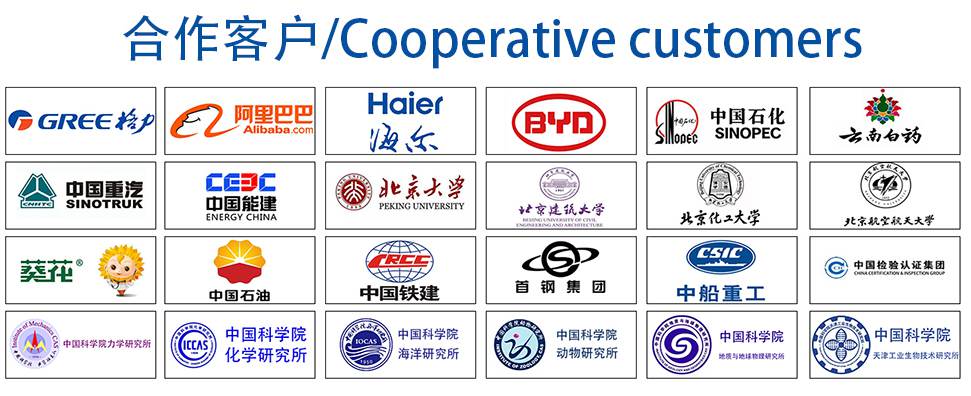
材料实验室
热门检测
251
211
183
201
193
197
203
197
202
210
199
195
192
198
192
188
203
194
204
197
推荐检测
联系电话
400-635-0567