盐雾试验检测技术与应用白皮书
在装备制造、汽车工业和海洋工程领域,金属材料腐蚀防护性能直接影响产品服役周期与安全可靠性。据中国腐蚀与防护学会2023年度报告显示,我国因金属腐蚀造成的直接经济损失达2.5万亿元,占GDP总量的2.1%。盐雾试验作为环境适应性检测的核心手段,通过模拟海洋大气、工业污染等腐蚀环境,系统评估材料及表面处理工艺的抗腐蚀能力。项目覆盖汽车零部件、电子元器件、航空航天部件等38个细分领域,形成从原材料筛选到成品验证的闭环质量管控体系。其核心价值在于建立产品全生命周期耐腐蚀性能数据库,为研发改进提供量化依据,同时满足ISO 9227、ASTM B117等国际标准认证要求。
技术原理与试验方法创新
现行盐雾试验主要分为中性盐雾试验(NSS)、醋酸盐雾试验(ASS)和铜加速醋酸盐雾试验(CASS)三大类,分别对应不同腐蚀场景的加速模拟。以ASTM B117标准为例,试验箱内维持(35±2)℃恒温环境,5%氯化钠溶液经雾化装置形成持续盐雾,实现材料表面均匀腐蚀。值得注意的是,新型复合循环腐蚀测试(CCT)技术正在逐步替代传统单一盐雾试验,通过湿热、干燥、盐雾多阶段循环,将试验周期缩短40%的同时更贴合实际服役环境。中国材料研究学会2024年数据显示,采用CCT技术的"汽车底盘件耐腐蚀检测方案"使故障复现准确率提升至92%。
标准化实施流程解析
完整的盐雾试验检测流程包含六大关键节点:样品预处理、试验参数设定、环境监控、中间检查、结果评定和报告生成。在新能源汽车电池箱体检测中,技术人员首先依据GB/T 10125进行表面清洁,随后将样品以15°倾斜角置入试验箱,确保盐雾自由沉降。试验过程中通过电化学工作站实时监测开路电位变化,每24小时采集一次腐蚀产物形态数据。值得注意的是,针对"三电系统"防护等级验证,需要同步执行GB 38031规定的浸水试验,形成多维性能评价矩阵。
行业应用与质量保障体系
在船舶压载舱涂层检测领域,DNV认证机构要求涂层试样通过4000小时盐雾试验后,划痕处单边腐蚀扩展不超过2mm。某船用涂料企业引入自动化盐雾试验系统后,将检测效率提升60%,成功获得LR、ABS等九大船级社认证。质量保障方面,检测机构需建立包含设备校准(±1℃温控精度)、溶液浓度检测(比重计±0.001g/cm³误差控制)、人员能力验证的三级管控体系。经 认可实验室统计,实施ISO/IEC 17025管理体系后,试验结果复现性标准差由0.35降至0.12。
智能化检测技术发展
基于机器视觉的腐蚀特征识别系统正在改变传统人工评级模式。某第三方检测机构开发的AI分析平台,可自动识别72类腐蚀形貌,量化评估起泡面积、锈蚀等级等12项参数,使结果判定时间缩短80%。在5G基站外壳检测场景中,该系统实现每平方米0.1mm²的微小点蚀识别精度。同时,物联网技术的应用使试验箱群实现远程监控,据机械工业仪器仪表综合技术经济研究所报告显示,智能盐雾试验系统使设备利用率从65%提升至89%。
面向未来,建议行业重点关注三个发展方向:首先建立基于大数据的腐蚀图谱数据库,推动检测标准动态更新;其次发展多因素耦合环境模拟技术,实现真实工况下的腐蚀行为预测;最后加强检测-防护-修复技术链条整合,构建全生命周期腐蚀防控体系。随着《中国制造2025》对产品质量要求的持续提升,盐雾试验检测将向智能化、精准化、场景化方向纵深发展,为高端装备可靠性保驾护航。
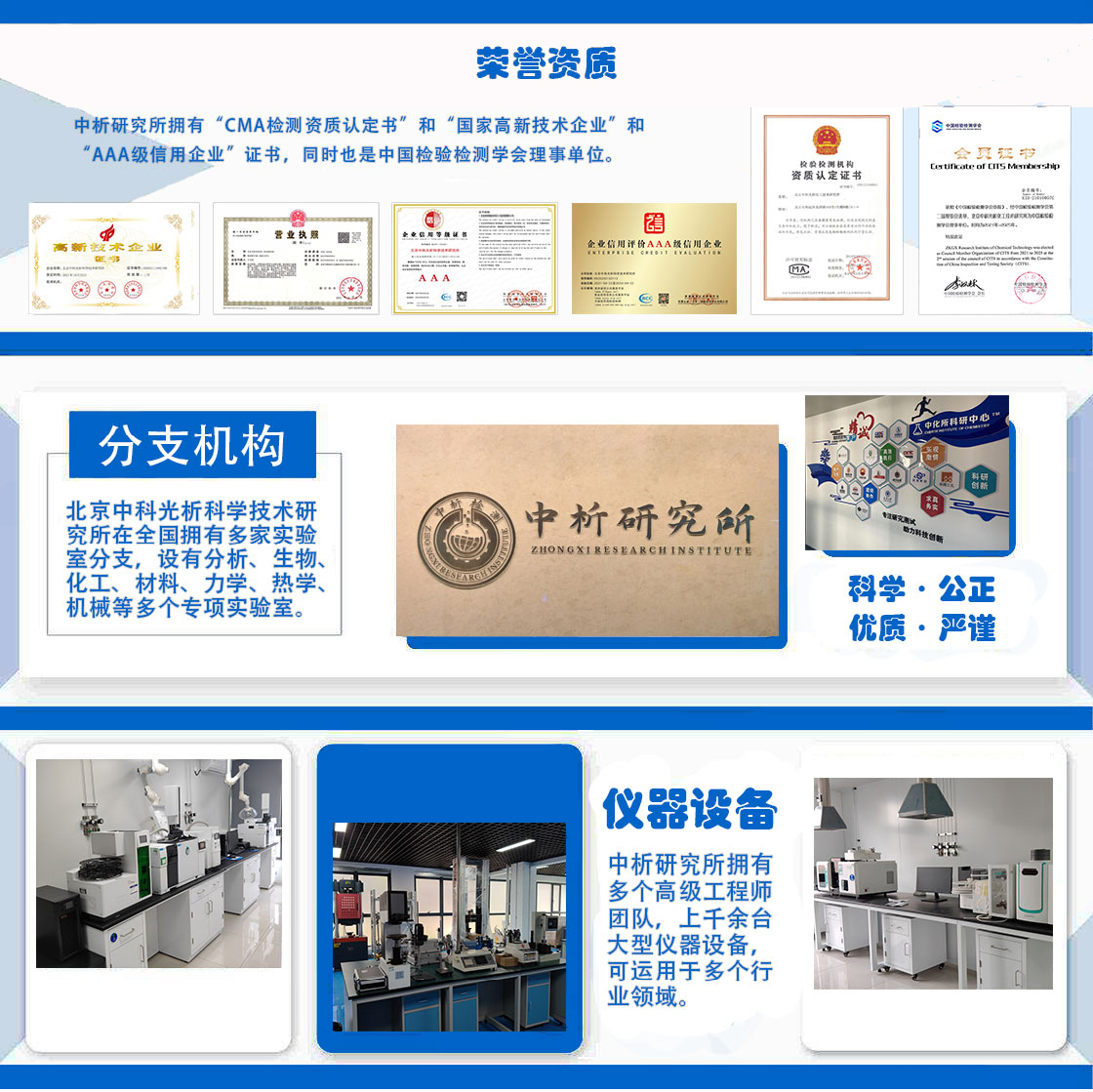
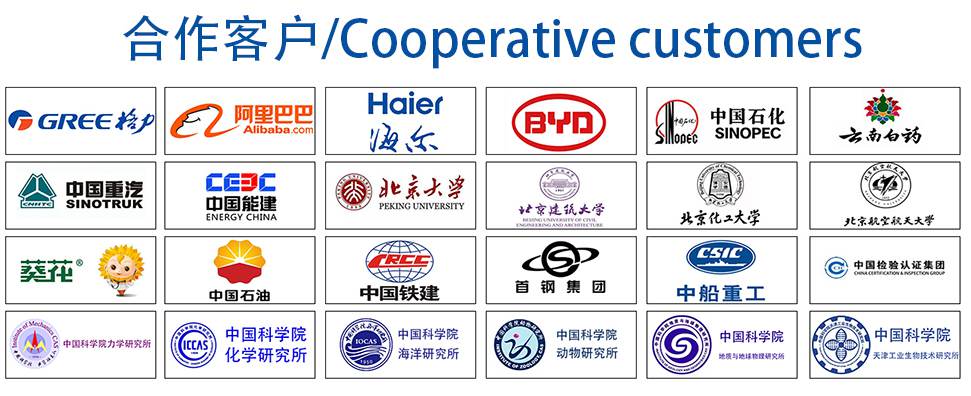