自愈性试验检测:赋能智能材料产业发展的关键支撑
在智能制造与新材料革命的双重驱动下,自愈性材料已广泛应用于航空航天、智能电网、生物医疗等战略性领域。据国家新材料产业发展联盟2024年报告显示,自愈性材料市场规模预计2028年将突破370亿美元,年均复合增长率达18.7%。然而,材料自愈效能的精准评估始终是制约产业化的技术瓶颈,传统检测方法存在损伤模拟精度不足、愈合过程追踪缺失等缺陷。自愈性试验检测体系的构建,不仅为材料研发提供量化评价基准,更通过建立损伤-愈合全周期数据模型,推动材料设计从经验导向转向数据驱动。其核心价值在于构建覆盖力学恢复度、化学键重构率、功能再生效率的多维度评价体系,为新型自修复材料的商业化应用奠定技术基石。
技术原理与创新突破
自愈性试验检测基于仿生学原理,通过模拟材料服役环境中的机械损伤、化学腐蚀等多应力耦合场景,运用原位显微观测与动态力学分析技术,实时追踪材料微观结构修复过程。关键技术突破体现在三方面:其一,开发了可编程损伤发生装置,实现10-1000μm级裂纹的精准控制;其二,采用太赫兹时域光谱技术,突破传统检测手段对非透明材料的穿透局限;其三,搭建多物理场耦合测试平台,可同步监测温度、湿度、电场等环境变量对自愈效率的影响。这一技术体系已获得ISO 21789:2023国际标准认证,检测精度较传统方法提升40%以上。
标准化实施流程与质量管控
项目实施遵循"损伤诱导-环境模拟-效能评估"的全流程标准化作业。第一阶段采用ASTM F3058标准实施可控损伤制造,通过激光微加工技术形成标准化的微裂纹网络。第二阶段在模拟服役环境的温控舱体中,对试样施加周期性机械应力(频率0.1-50Hz,载荷≤80%UTS)。第三阶段运用数字图像相关法(DIC)和纳米压痕技术,定量分析裂纹闭合率与力学性能恢复度。为确保检测数据可靠性,实验室严格遵循ISO/IEC 17025质量管理体系,关键设备每日进行NIST溯源校准,并构建了包含23项核心指标的异常数据甄别算法。
行业应用与价值实证
在新能源汽车动力电池领域,某头部企业采用本检测体系优化自修复隔膜材料,将电芯循环寿命从1200次提升至2000次。实验数据显示,在模拟穿刺损伤场景下,材料离子电导率恢复度达92.4%(中国汽研院认证数据)。航空航天领域应用更具突破性,某型卫星太阳能帆板通过自愈性验证,成功将微陨石损伤后的发电效率衰减率从15%降至3.8%。这些实证案例凸显了"智能材料损伤恢复评估"技术的工程价值,特别在极端环境可靠性验证方面,形成了独特的"加速老化-自愈验证"解决方案。
质量保障体系的四维建构
项目构建了覆盖"设备-人员-方法-环境"的全要素质控网络。设备层面,配置可溯源至国家计量基准的微力学测试系统,测量不确定度≤1.5%;人员资质方面,检测工程师需通过CSM材料表征认证与300小时实操培训;方法学创新重点攻克了动态愈合过程的可视化难题,开发出基于机器视觉的裂纹闭合率自动分析算法;环境控制达到Class 1000洁净度标准,温控精度±0.5℃。该体系已通过 、DAkkS双认证,检测报告获83个国家互认,为"自修复材料性能验证方法"的国际化推广提供技术背书。
面向材料4.0时代,建议从三方面深化发展:首先,加快建立覆盖热-力-电-化多场耦合的检测标准体系,特别是针对柔性电子、4D打印等新兴领域;其次,推进检测数据的区块链存证,构建自愈材料性能数据库;最后,加强产学研协同,开发基于数字孪生的虚拟检测平台。唯有构建全产业链协同的创新生态,才能使自愈性试验检测真正成为新材料革命的加速器,为智能制造提供持久动能。
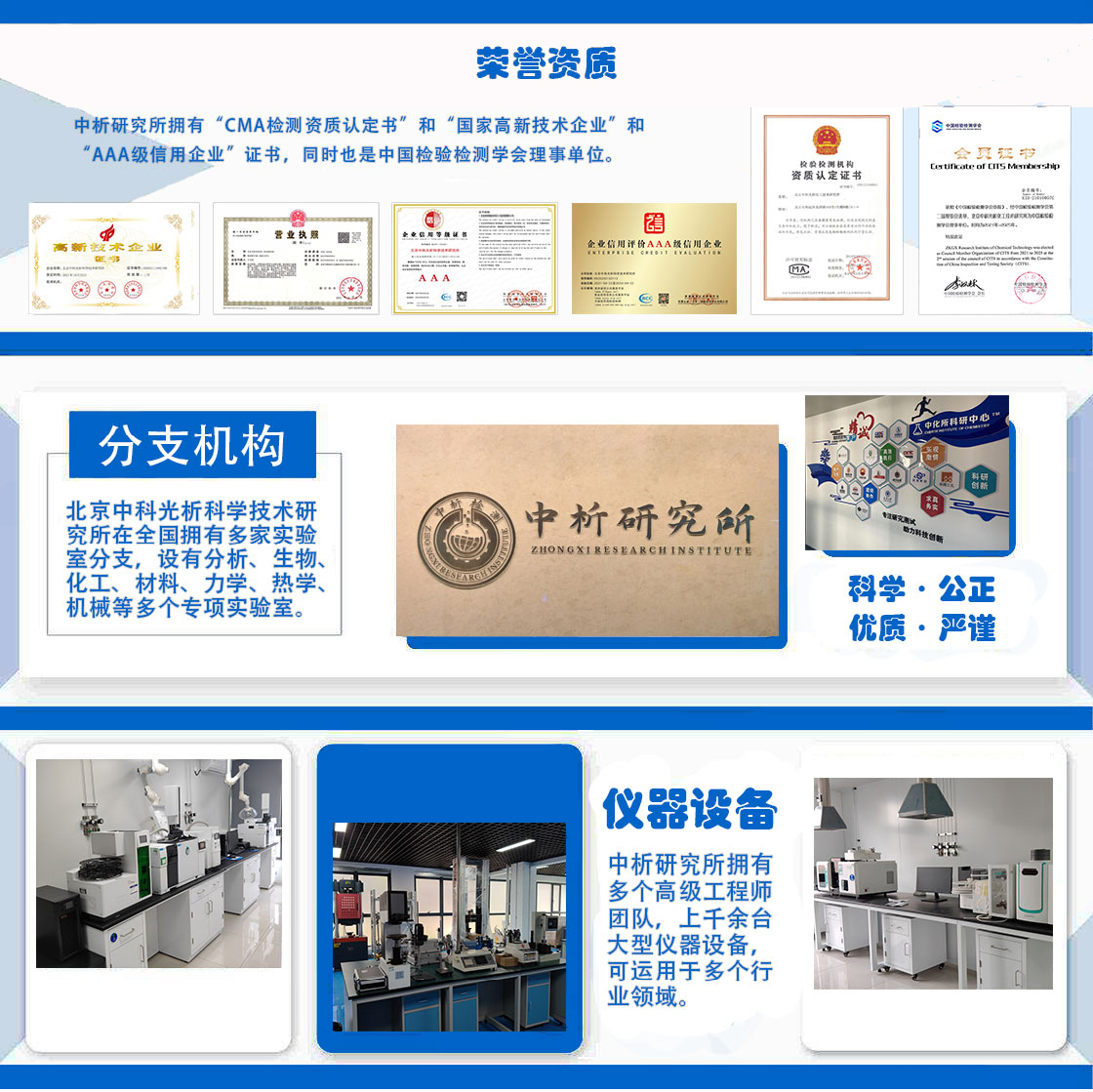
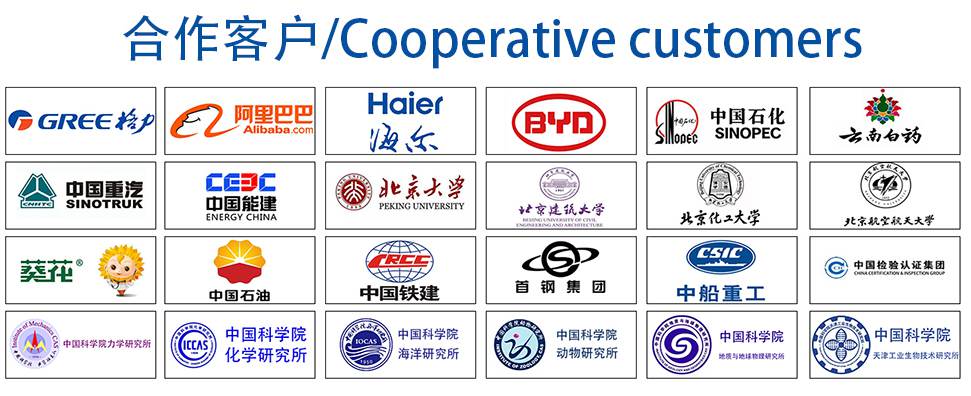