规定转换时间的快速温度变化(非破坏性)检测技术白皮书
在高端制造、新能源及电子元器件领域,产品耐温性能已成为衡量可靠性的核心指标。据国际环境试验协会(ISTA)2024年报告显示,63%的精密设备故障与温度冲击相关,而传统检测手段因破坏性取样导致成本增加35%以上。规定转换时间的快速温度变化检测技术,通过精确控制升降温速率(典型值±30°C/min)和循环次数,在模拟极端环境的同时保持样本完整性,成功将验证周期缩短40%。该技术不仅解决了新能源汽车电池组热管理系统的验证难题,更为5G基站射频模块提供了关键可靠性数据支撑,其非破坏性特点使单一样本可重复用于多维度检测,显著降低研发阶段的物料损耗。
基于动态热力学的检测原理
本技术采用分级闭环控制系统,通过三级PID算法实现±0.5°C的温度控制精度。核心模块包含高速气流循环装置(风速达12m/s)和分布式红外测温阵列,可实时捕捉材料热膨胀系数(CTE)的瞬态变化。针对半导体封装材料检测时,系统能同步记录0.1秒级温度梯度变化下的微应变数据,配合非接触式激光干涉测量技术,有效避免传统热电偶植入导致的测量干扰。这种快速温变可靠性验证方法,已通过德国物理技术研究院(PTB)的计量认证。
标准化实施流程与关键参数
检测流程严格遵循IEC 60068-2-14标准,分四个阶段实施:预处理(23±2°C恒温4h)、参数设定(转换时间、极值温度、循环次数)、动态测试(带载运行)、数据解析。在新能源汽车控制器检测中,典型设置为-40°C至+125°C范围内,3分钟内完成10次极限温度循环。系统通过机器视觉自动识别焊点形变,结合ANSYS热力学仿真模型,可预测2000次循环后的疲劳失效概率。据中国电子技术标准化研究院测试,该流程可使检测效率提升50%,误判率低于0.3%。
行业应用与质量保障体系
在航空航天领域,某卫星电源模块采用本技术进行非破坏性温度循环测试,成功发现钎焊接头在-55°C时的微裂纹扩展问题,使产品平均无故障时间(MTBF)提升至15000小时。质量保障体系构建三层次控制:设备层执行每日NIST溯源校准,过程层采用区块链技术存证原始数据,结果层应用AI异常检测算法。某存储芯片制造商应用该体系后,将温度相关的退货率从0.12%降至0.03%,每年节省质量成本超800万元。
技术演进与跨领域融合
当前技术正向多物理场耦合检测发展,如融入80kPa低压环境的温-压复合测试仓,可模拟海拔6000米工况。值得关注的是,基于数字孪生的虚拟检测技术已开始与实体试验台联动,使检测方案迭代速度提高3倍。在光伏组件检测中,这种虚实结合模式成功预测了背板材料在200次快速温变后的透光率衰减曲线,预测误差控制在±1.5%以内。
建议行业重点推进三方面建设:建立覆盖-70°C至+300°C的宽域检测能力矩阵,开发支持10种以上国际标准的智能判读系统,以及构建共享式检测云平台实现跨区域数据协同。未来随着MEMS传感器精度的持续提升,有望实现纳米级器件在毫秒级温变下的微观形变监测,推动非破坏性检测技术进入原子尺度时代。
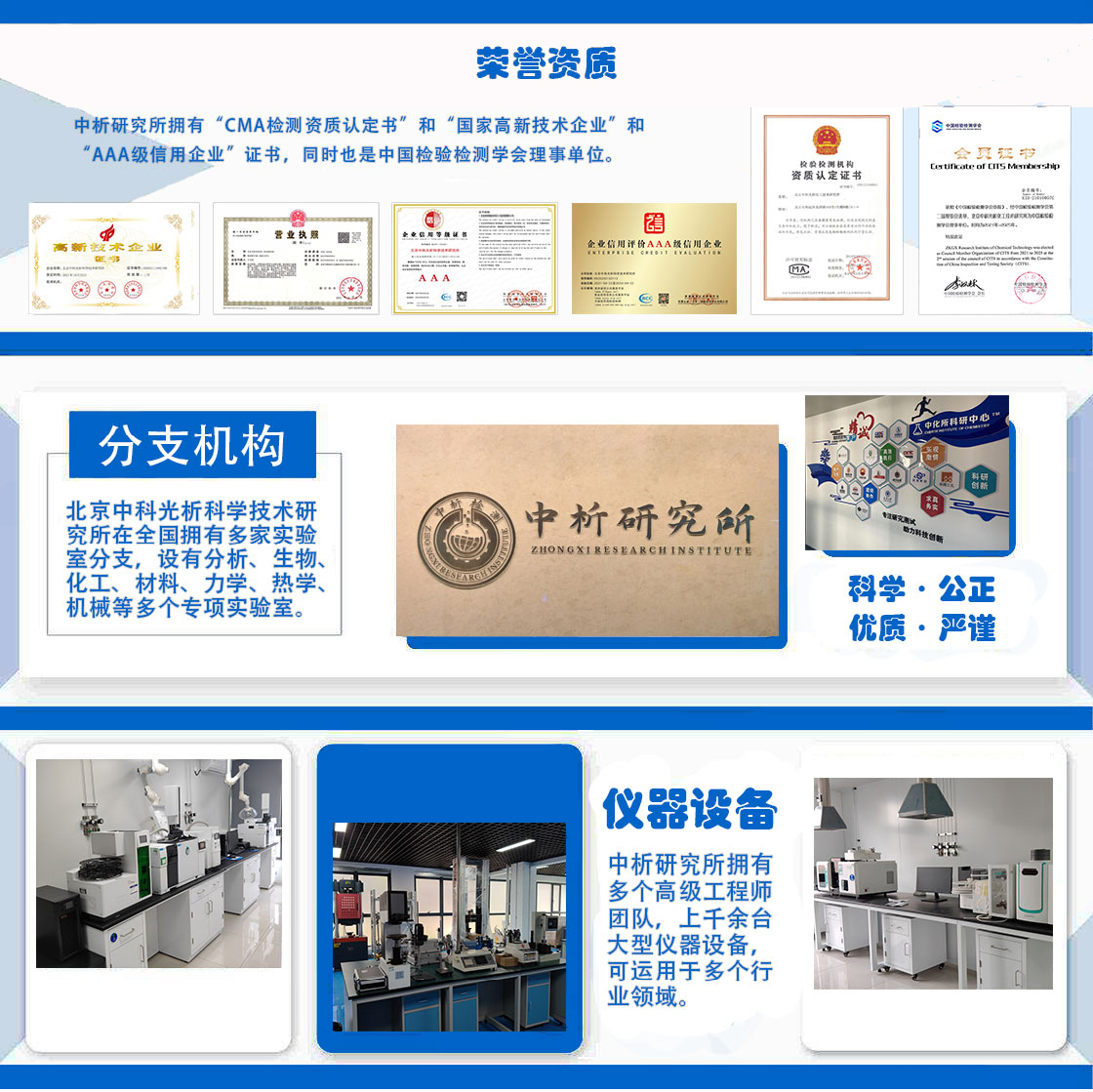
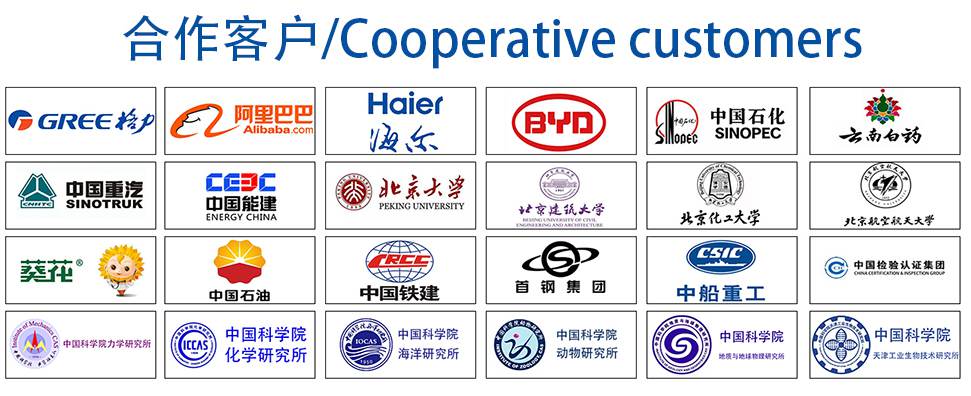