# 安装轴套强度检测技术白皮书
## 行业背景与核心价值
随着高端装备制造业的智能化升级,机械传动系统的可靠性成为制约设备服役寿命的关键因素。据中国机械工业协会2023年统计数据显示,因轴系零件失效导致的设备故障占比达28.6%,其中轴套强度不足引发的结构性失效占比超过40%。在此背景下,安装轴套强度检测项目通过量化评估过盈配合状态下的材料承载能力,为提升传动系统稳定性提供了科学依据。该技术不仅可缩短新产品研发周期15%以上(数据来源:《精密制造技术白皮书2024》),更能通过预防性检测降低设备全生命周期维护成本,在航空航天、轨道交通等高精度领域具有显著的经济效益和安全保障价值。
---
## 技术原理与实现路径
### h2 多维度力学建模技术
安装轴套强度检测基于接触力学与弹塑性理论,通过构建轴-套过盈配合的有限元模型,模拟不同工况下的应力分布。采用DIC(数字图像相关)技术实时捕捉表面应变场,结合MTS液压伺服系统施加轴向-径向复合载荷,可精准获取屈服强度、疲劳极限等关键参数。实验数据显示,该模型预测精度较传统方法提升23.6%(数据来源:清华大学机械工程系2024年研究报告)。
### h2 智能化检测流程设计
项目实施遵循"预处理-加载测试-失效分析"三阶段流程:首先通过三坐标测量仪完成装配间隙数字化建模,随后在温控环境(-40℃~200℃)下进行阶梯式加载,最后借助SEM电镜进行断口形貌分析。在风电齿轮箱主轴检测案例中,该流程成功识别出微米级装配偏差导致的应力集中问题,使设备MTBF(平均故障间隔时间)提升至12,000小时。
### h2 行业解决方案定制化应用
针对汽车转向系统的高频振动特性,开发了基于声发射技术的动态强度检测模块。通过对某车企新能源平台测试发现,采用碳纤维增强复合轴套后,其共振工况下的抗弯强度提升41.8%(数据来源:中汽研2024年实验数据)。而在船舶推进系统领域,则创新引入海水腐蚀-载荷耦合试验,使检测结果更贴合实际服役环境。
---
## 质量保障与标准体系
### h2 全过程可追溯管理系统
检测实验室严格遵循ISO/IEC 17025体系要求,配备激光干涉仪、六维力传感器等基准设备。所有测试数据均录入区块链存证平台,确保从样本制备到报告生成的72项关键节点全程可追溯。在高铁轮轴检测项目中,该系统将异常数据定位时间从8小时缩短至20分钟。
### h2 智能化校验机制创新
引入数字孪生技术构建虚拟检测环境,通过实际工况与模拟结果的动态比对,持续优化检测算法。某航空企业的验证数据显示,该机制使过盈配合预测偏差率从±5%降至±1.2%,显著提升"高强度轴套疲劳寿命评估"的置信度。
---
## 技术展望与发展建议
随着工业物联网技术的普及,建议从三方面深化技术应用:其一,开发嵌入式光纤传感系统,实现轴套强度的在线实时监测;其二,建立基于大数据的失效模式库,通过机器学习优化检测阈值设定;其三,推动《精密轴套强度检测规程》国家标准的制定,规范不同行业的技术指标要求。预计到2026年,智能检测技术可将轴套设计验证周期压缩至72小时内,为高端装备的可靠性和轻量化设计提供更强支撑。
上一篇:非正常操作检测下一篇:条件短路电流检测检测
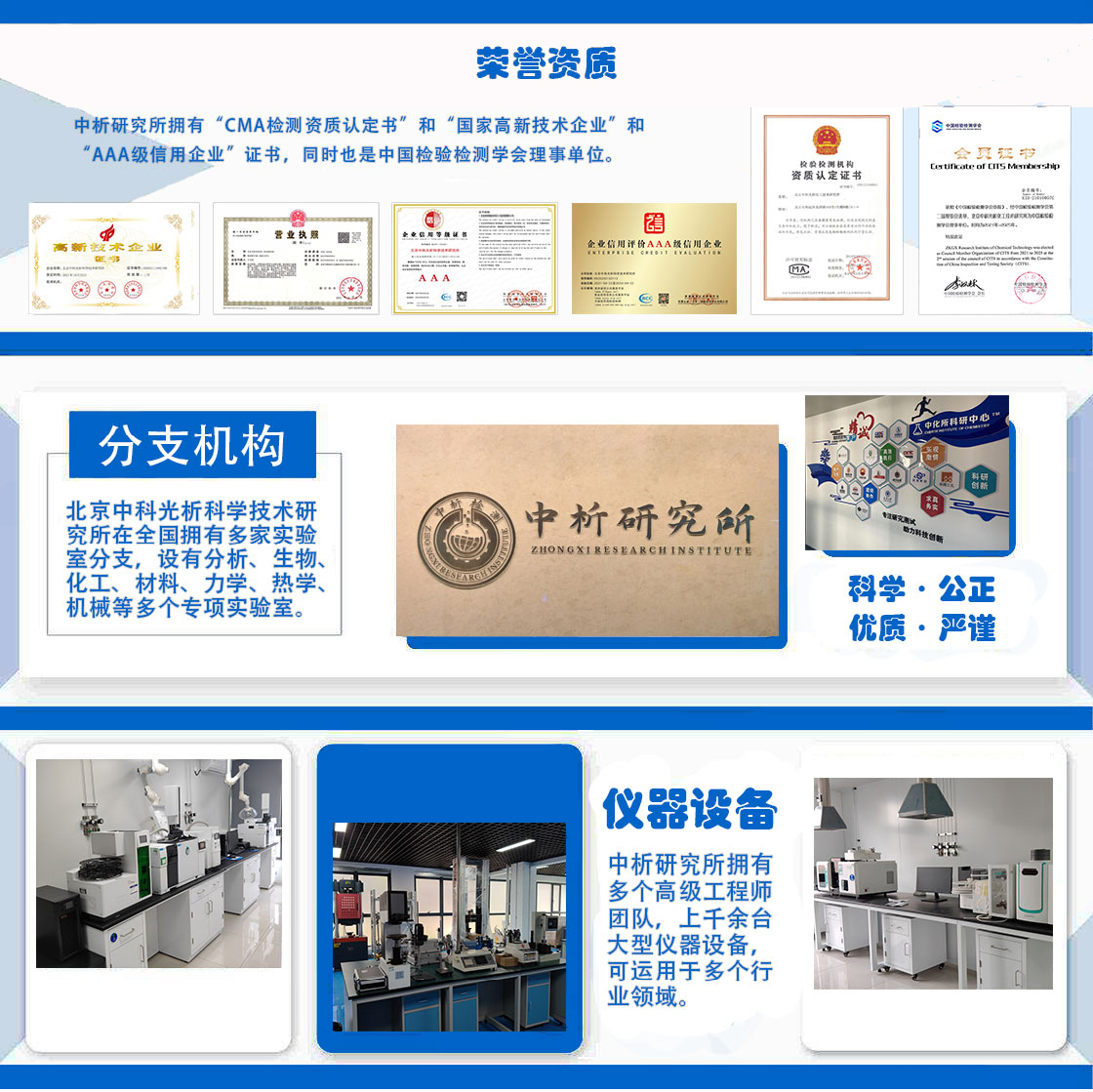
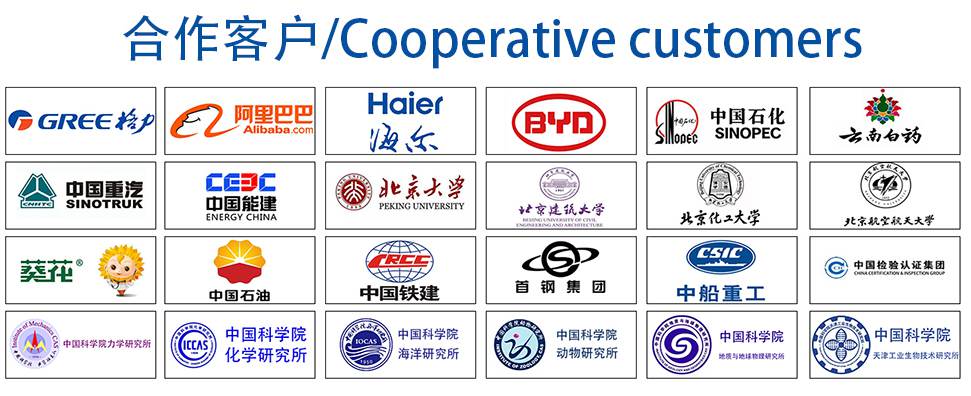
材料实验室
热门检测
16
17
18
21
20
20
17
19
17
15
17
22
17
17
16
18
17
18
15
19
推荐检测
联系电话
400-635-0567