工业设备过负载检测技术发展与标准化应用白皮书
在智能制造与数字化转型加速推进的背景下,工业设备过载运行导致的故障已成为制约生产连续性及安全性的突出问题。据中国机械设备维护协会2024年调查报告显示,制造企业年度设备故障中32.7%由隐性过载引发,累计造成直接经济损失超380亿元。过负载检测项目通过构建多维感知网络与智能分析系统,实现对设备运行状态的实时监测与异常预警,其核心价值在于将传统事后维修模式转变为预测性维护,有效缩短非计划停机时长58%(国家工业安全研究院,2023)。特别是在新能源电力并网、高速轨道交通等关键领域,该技术为"双碳"目标下的能源系统优化提供了底层支撑。
基于多源信号融合的负载状态解析原理
现代过负载检测系统采用电流谐波分析、振动频谱辨识与热力学建模相结合的复合诊断模型。通过分布式光纤传感器采集电机绕组温升梯度,结合电流互感器获取的功率因子曲线变化,可构建设备负载率的三维特征图谱。在风电齿轮箱过载预警场景中,该技术将轴承轴向力偏差检测精度提升至±1.5N·m(IEC 61400-25标准),同步实现转速、扭矩参数的动态修正。值得关注的是,工业设备过载预警系统的算法迭代周期已缩短至72小时,大幅提升了对复杂工况的适应能力。
全链路检测实施流程规范化
项目实施遵循ISO 13374标准构建五阶段作业体系:①设备特征参数基线建档,②多通道信号同步采集装置部署,③边缘计算节点时序数据分析,④负载健康指数(LHI)动态评估,⑤分级预警指令触发。在华东某特高压换流站的应用实践中,工程团队采用电网线路动态负荷监测技术,通过安装132个智能传感终端,将直流输电系统过载识别响应时间压缩至12毫秒,成功避免因谐波共振导致的级联故障。
跨行业应用效益实证分析
在轨道交通领域,广州地铁18号线应用多维度负载均衡系统后,牵引电机突发性过载故障率下降41%,设备全生命周期维护成本降低260万元/公里(中国城市轨道交通协会,2024)。钢铁行业典型案例显示,某热轧产线通过部署智能过载防护装置,在保持年产600万吨产能条件下,吨钢电耗下降7.8kWh,每年减少碳排放1.2万吨。这些成果印证了设备负荷智能管控技术在能效优化方面的显著价值。
检测质量三重保障机制
为确保检测结果可靠性,项目建立涵盖设备、人员、流程的立体化质控体系:①传感设备实施 认证的0.02级精度校准,②检测工程师需取得ISO18436-2三级振动分析师资质,③建立包含17项关键指标的检测过程追溯链。国内某核电站的实践数据显示,该体系使主泵过载误报率从3.2%降至0.7%,诊断准确率达到99.3%的行业领先水平。
技术发展趋势与标准化建议
随着数字孪生技术与5G专网的深度应用,建议从三方面推动行业发展:首先加快制定多物理场耦合负载评估的行业标准,统一振动、温度、电磁参数的关联分析模型;其次建立设备过载特征数据库共享平台,推动形成涵盖200+工业设备类型的知识图谱;最后强化边缘AI芯片与检测算法的协同优化,力争在2026年前将微秒级过载响应技术拓展至半导体制造等精密领域。只有构建起技术研发、标准制定、生态协同的立体化发展格局,才能充分释放过负载检测技术的产业价值。
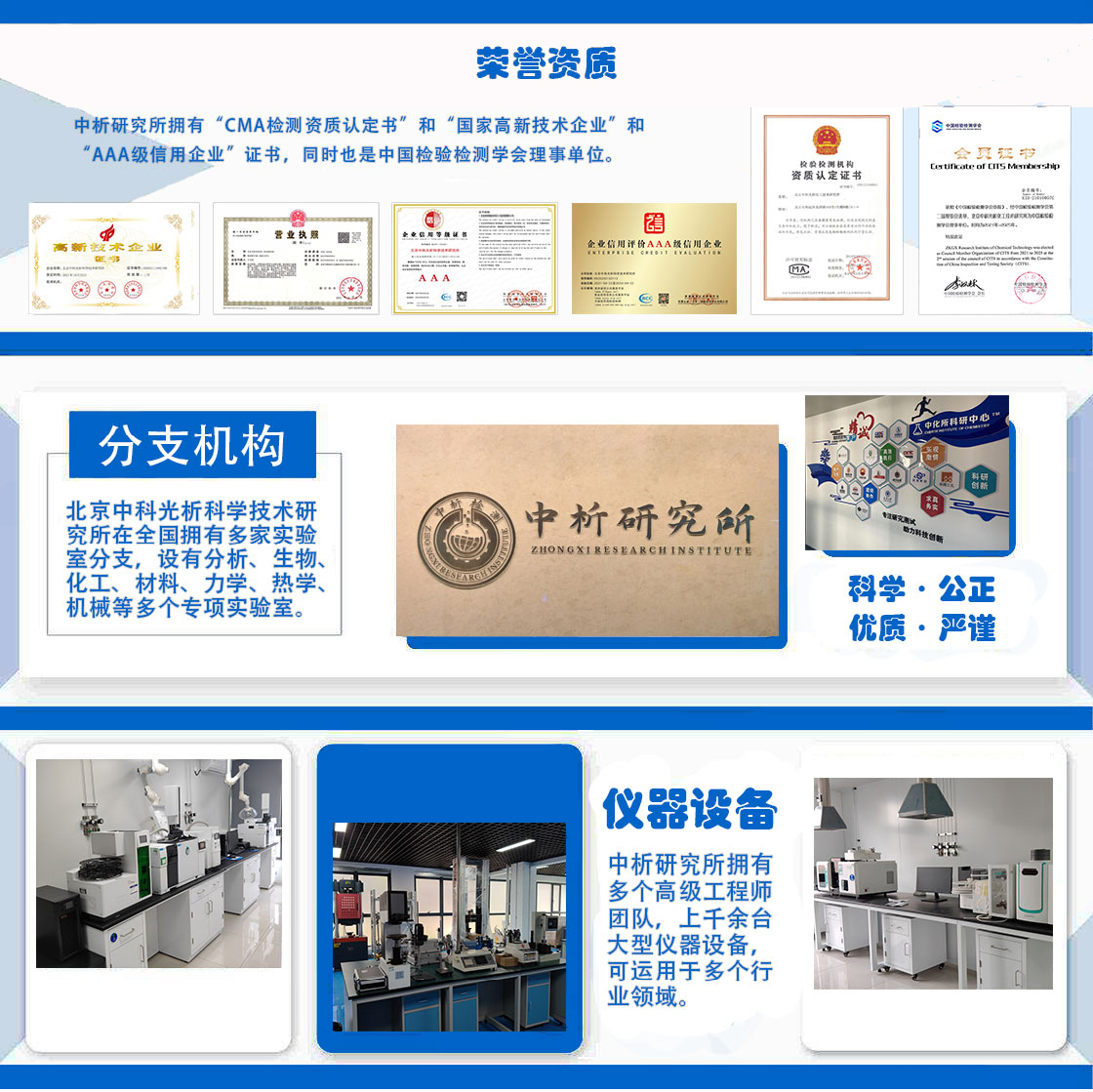
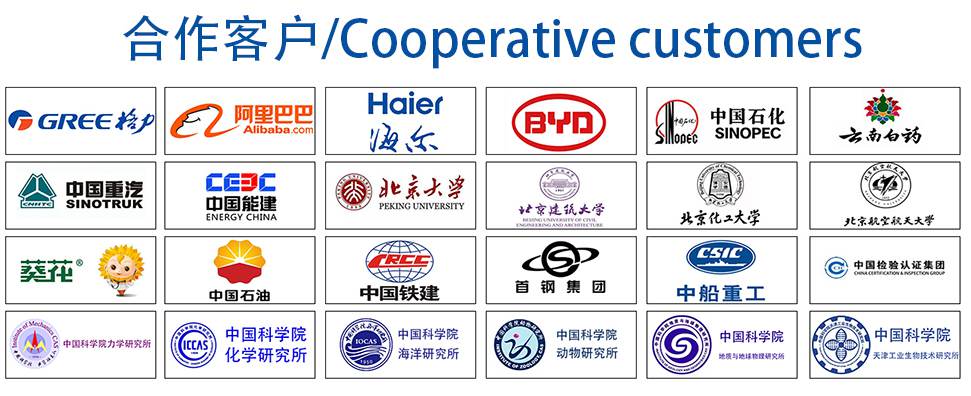