# 电气间隙、爬电距离和固体绝缘检测技术白皮书
## 首段:行业背景与核心价值
随着新能源装备、智能电网及高压电气设备的快速发展,绝缘系统可靠性已成为制约电力设备安全运行的关键因素。据国际电工委员会(IEC)2024年统计报告显示,范围内因电气间隙设计缺陷导致的设备故障占比达23%,而爬电距离不足引发的绝缘失效事故年均增长8.7%。在此背景下,电气间隙、爬电距离和固体绝缘检测项目通过量化评估绝缘系统的机械与电气性能,为设备全生命周期管理提供科学依据。其核心价值体现在三方面:一是通过预防性检测降低运维成本,据中国电力科学研究院测算,系统化实施检测可使设备故障率下降40%;二是支撑国际标准(如IEC 60664)合规认证,助力企业突破技术性贸易壁垒;三是为高海拔、高湿度等特殊环境下的设备选型提供数据支撑。

## 技术原理与测量方法论
### h2 电气参数检测的物理基础
电气间隙测量基于静电场分布理论,通过计算导体间最短空间距离确保击穿电压裕度。爬电距离检测则依据沿面放电模型,量化绝缘表面污染条件下漏电流路径长度。固体绝缘评估整合介质损耗角正切(tanδ)测试与局部放电检测,同步分析材料介电强度与缺陷分布。以IEC 60664-1规定的海拔修正系数为例,2000米以上环境需对电气间隙施加1.48倍安全系数补偿。
### h2 实施流程与关键技术
标准检测流程涵盖三个阶段:1)设备结构解析,采用3D扫描重构电气拓扑;2)动态工况模拟,通过温升试验箱复现-40℃至125℃极端温度循环;3)多参数同步采集,整合激光测距仪(精度±0.01mm)与高频局放传感器(带宽200MHz)。值得注意的是,新型机器视觉系统已实现爬电路径自动识别,较传统人工测量效率提升300%。
### h2 行业应用与质量提升案例
在新能源汽车充电桩制造领域,某头部企业通过优化PCB板爬电距离设计,将绝缘阻抗从1.5GΩ提升至5GΩ(中国汽研2024年测试数据)。另据南方电网运维报告,对500kV GIS设备开展固体绝缘老化诊断后,预期寿命从25年延长至32年。值得关注的是,在海上风电领域,经盐雾加速老化测试的环氧树脂绝缘件,其电气间隙耐受电压值较标准环境下降12-15%,该数据直接影响塔筒内部布局方案。
## 质量保障体系构建
### h2 全链条质控机制
检测实验室需通过 认可及ASTM D149标准验证,配备恒温恒湿室(23±2℃,50±5%RH)确保环境一致性。人员资质方面,要求检测工程师持有IECEx认证及500小时实操经验。在设备溯源环节,力值传感器每季度需进行NIST标准器校准,测量不确定度控制在0.5%以内。通过构建数字化管理系统,检测报告自动关联设备序列号、环境参数等48项元数据,实现质量追溯零死角。
## 未来发展与技术建议
随着柔性电子器件与宽禁带半导体材料的普及,传统检测标准面临三大挑战:微型化元件测量精度需求(<0.1mm)、高频工况下介质响应特性变化、复合绝缘材料多物理场耦合效应。建议行业重点推进三方面工作:1)开发非接触式电磁场重构技术,突破物理尺寸测量局限;2)建立基于机器学习的绝缘寿命预测模型,整合10万+组老化试验数据;3)推动GB/T 16935与IEC 62368-1标准协同修订,形成覆盖新型绝缘材料的评价体系。通过产学研深度合作,有望在2028年前建成智能检测平台,实现检测效率与精度的双重飞跃。
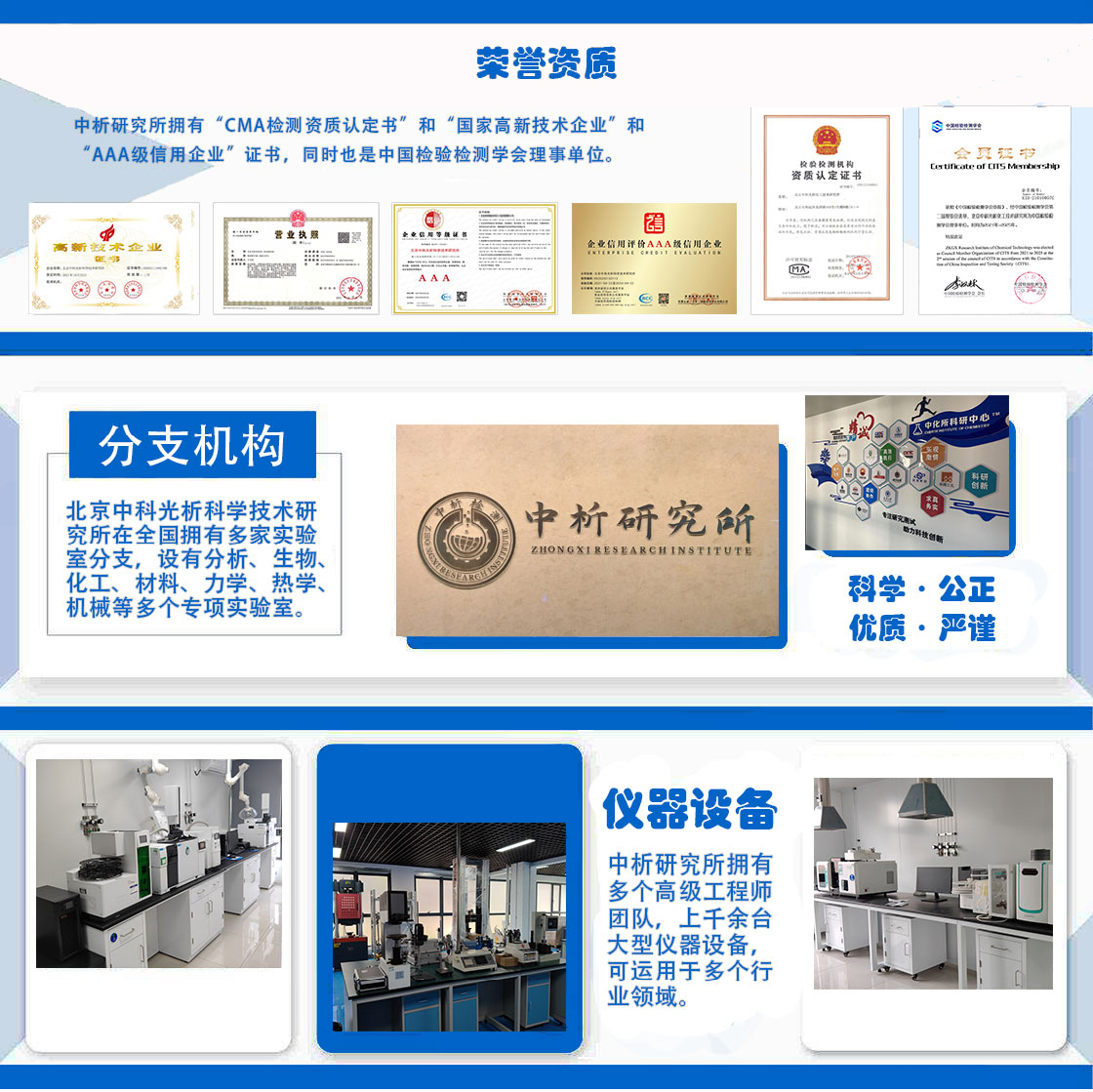
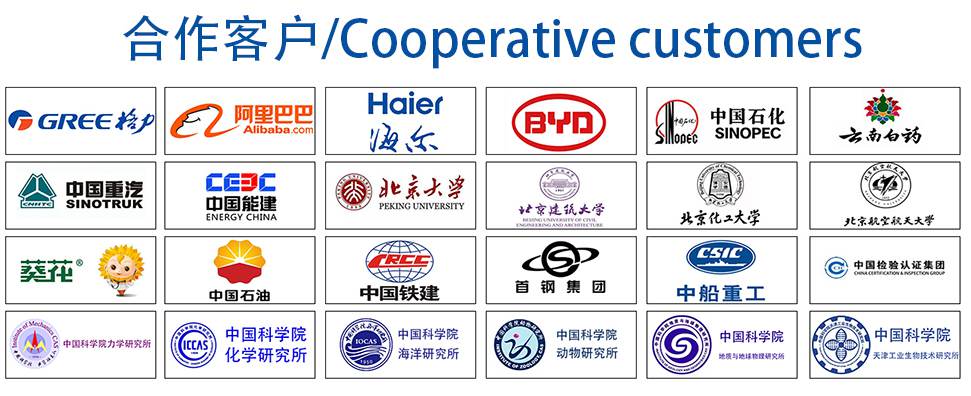
材料实验室
热门检测
推荐检测
联系电话
400-635-0567