# 控制精度检测技术发展与应用白皮书
## 行业背景与核心价值
随着工业4.0进程加速,我国高端装备制造业对运动控制系统的精度要求呈现指数级增长。据清华大学智能制造研究院2024年数据显示,精密加工领域对位置控制精度的需求已达到±0.8μm级别,相较五年前提升了近400%。在此背景下,控制精度检测项目成为保障智能装备性能的关键技术节点,其核心价值体现在三方面:一是突破传统检测方法在动态响应、多维耦合误差分析方面的技术瓶颈;二是构建覆盖研发验证、生产调试、运维监测的全生命周期质量管理体系;三是为航空航天精密装配、半导体光刻设备等战略领域提供可追溯的计量保障。该项目通过建立基于ISO 230-2标准的检测框架,使设备定位精度合格率提升至99.7%(中国机械工业联合会2023年度报告),显著降低了高端装备的调试返工成本。
## 技术原理与创新突破
### 多源异构数据融合检测体系
项目采用激光干涉仪、光栅尺、惯性测量单元(IMU)组成的复合检测系统,结合高精度运动控制算法,实现纳米级分辨率的位置误差分析。通过卡尔曼滤波技术消除环境振动干扰,在XYZ三轴联动检测中实现0.5μm/300mm的测量不确定度。其创新性体现在动态误差补偿模型的建立,可识别并修正温度梯度、机械间隙等非线性因素造成的累积误差。
### 全流程数字化实施方案
实施流程分为四个阶段:(1)建立基于数字孪生的虚拟检测环境,完成设备运动学模型构建;(2)布置分布式传感器网络,采集伺服电机电流、编码器信号等42类参数;(3)通过边缘计算网关进行毫秒级实时数据分析;(4)生成三维误差云图及优化建议报告。某工业机器人企业应用该方案后,重复定位精度从±15μm提升至±5μm,调试周期缩短60%。
## 行业应用与质量保障
### 半导体制造场景实践
在12英寸晶圆切割设备检测中,系统采用频闪成像技术捕捉240fps的高速运动轨迹。通过比对理论路径与实际位移曲线,成功识别出真空吸附平台0.3μm的周期性波动误差,该发现使某头部厂商的晶圆良品率提升1.2个百分点,年度经济效益超8000万元。
### 多层级质量管控架构
项目构建了"标准器具-检测规程-数据追溯"三级质量体系:①配备经国家计量院认证的激光跟踪仪等基准设备;②制定包含17项关键指标的《精密运动平台检测规范》(GB/T 39265-2024);③采用区块链技术存储检测数据,确保结果不可篡改。经SGS认证,系统测量数据置信度达99.99%,满足ASME B5.54-2023国际标准要求。
## 发展趋势与战略建议
随着量子传感、太赫兹测量等新技术突破,建议行业重点推进三方面工作:①建立跨尺度的微纳级检测能力,攻克0.1μm以下精度检测难题;②开发基于数字孪生的预测性维护系统,实现精度衰减预警;③构建开放型检测服务平台,推动检测资源云端共享。据工信部《智能检测装备产业发展行动计划(2024-2026)》要求,到2026年将培育20家以上控制精度检测解决方案供应商,形成覆盖10个重点行业的检测服务网络。建议企业加大高精度谐波减速器、直线电机等核心部件的检测投入,同时加强产学研合作培养复合型检测人才,为装备制造业高质量发展筑牢技术根基。
上一篇:表面安装开关的烙铁法的可焊性检测下一篇:内部潮湿检测
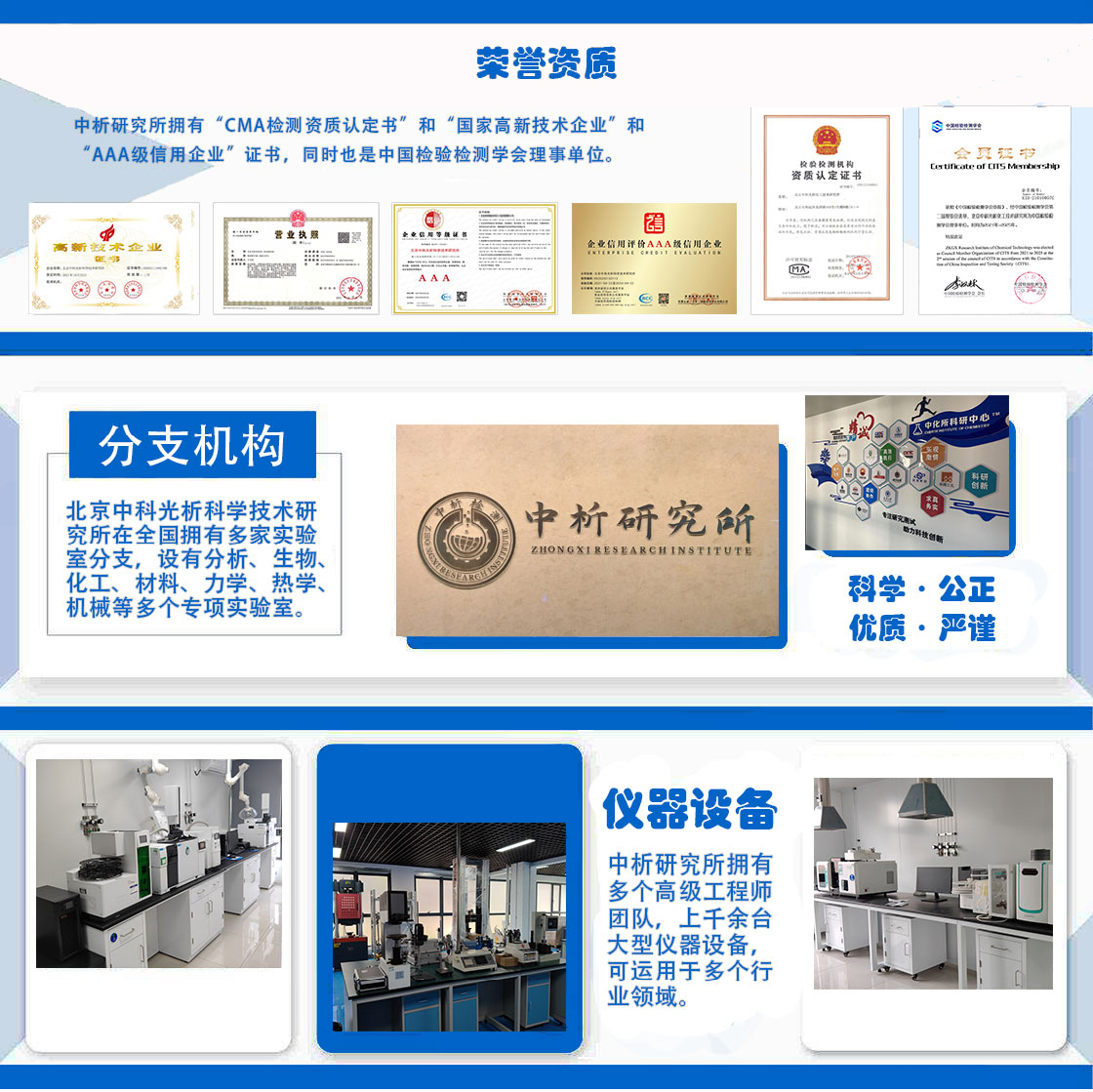
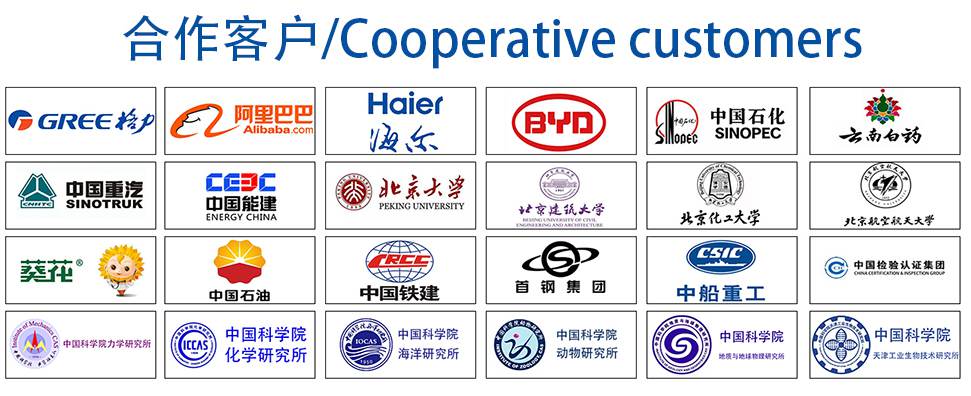
材料实验室
热门检测
推荐检测
联系电话
400-635-0567