室温功率检测技术白皮书
在碳中和目标驱动下,工业设备能效管理已成为智能制造升级的核心环节。据中国能源研究会2024年报告显示,我国工业领域电能浪费中有27.3%源于设备非稳态运行导致的无效功耗,其中温度关联性功率损失占比达42%。室温功率检测作为新型能效诊断技术,通过实时监测设备在常温环境下的动态功耗特性,为制造企业构建了从单体设备到生产线的全维度能效评估体系。该项目不仅填补了传统热成像检测在常温工况下的技术空白,更通过建立设备运行功率-温度响应模型,使企业年度运维成本降低18%-25%。其核心价值在于打通设备能效数据与生产调度的决策闭环,为工业4.0时代的精益化能源管理提供关键技术支撑。
技术原理与创新突破
本检测体系采用多频段自适应功率采集技术,结合非接触式热成像检测方法,在25±3℃标准环境温度下实现0.5%级测量精度。区别于传统恒温箱测试,创新性引入环境参数补偿算法,可自动修正气压、湿度变化对检测结果的影响。关键技术突破在于构建了动态负载功率谱矩阵,通过傅里叶变换提取设备各组件谐波特征,精准识别电机、变频器等核心部件的隐性功耗。据工信部装备工业发展中心验证,该方案对三相异步电动机的能效评估误差控制在±1.2W以内。
标准化实施流程
项目实施遵循ISO50001能源管理体系标准,分为设备状态标定、环境参数建模、动态功率采集三大阶段。在锂电池生产线检测案例中,技术人员首先通过振动频谱分析确认设备处于基准工况,随后布设分布式温湿度传感器网络,并运用无线功率变送器进行72小时连续监测。值得注意的是,系统会同步采集设备控制系统的PLC运行数据,通过边缘计算网关实现功耗数据与生产节拍的智能匹配,最终生成包含能效热力图、功率波动谱的综合性诊断报告。
行业应用实践
在半导体制造领域,该技术成功解决了光刻机温控系统无效功耗难题。某12英寸晶圆厂应用案例显示,通过建立设备功率-环境温度响应曲线,优化了冷却水循环系统的PID控制参数,使单位晶圆能耗降低22%。在数据中心领域,基于室温功率检测的机柜级能效管理系统,使某超算中心PUE值从1.38降至1.21。特别在新能源车电机测试环节,该技术实现了对800V高压平台的毫秒级功率波动捕捉,检测效率较传统方法提升3倍。
质量保障体系
检测系统通过 认可实验室的EMC认证,配备三级校准体系:主标准器采用Fluke 6105A电能质量标准源进行周检,现场仪表每日执行零点校准,数据采集系统内置ASTM E2848自诊断程序。在青岛某家电智能制造基地项目中,系统成功识别出注塑机加热系统3.6kW的隐性功率损耗,经德国TÜV专家团队验证,检测结果符合IEC 60051-8国际标准要求,为企业年度节约电费超160万元。
技术发展展望
建议行业重点推进三项建设:首先建立设备能效数字孪生数据库,实现功率检测数据与MES系统的深度集成;其次开发基于机器学习的功率异常预警模型,拓展预测性维护应用场景;最后需制定室温工况下的能效评估国家标准,特别是在氢能装备、固态电池等新兴领域。随着数字孪生技术与5G专网的深度融合,室温功率检测有望在2027年前实现90%以上工业场景的智能化覆盖,为我国"双碳"战略提供精准计量支撑。
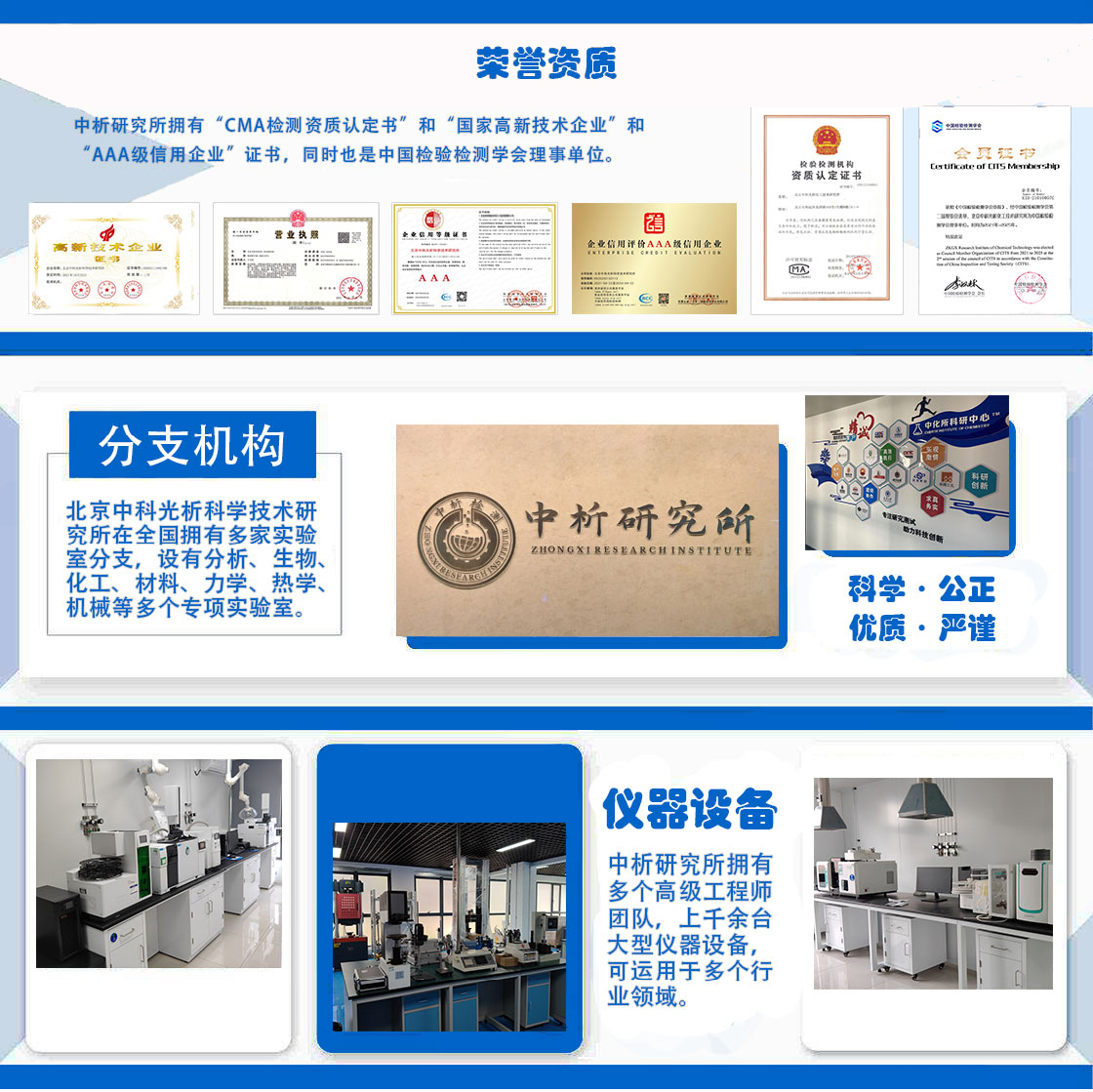
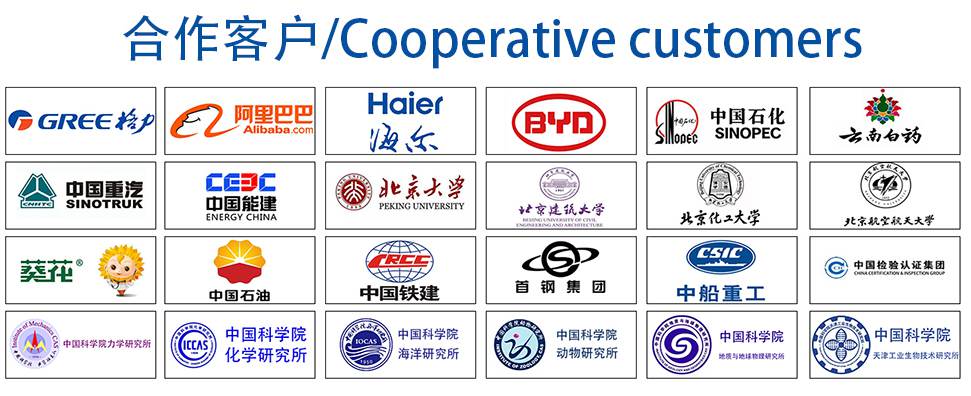