峰值转矩检测技术应用与发展白皮书
在智能制造与新能源产业高速发展的背景下,动力系统能效优化已成为工业升级的核心课题。据中国电机工程学会2024年报告显示,电机系统能耗占工业总用电量的68%,其中峰值转矩异常导致的设备故障占总停机事件的23%。峰值转矩检测作为动力系统健康管理的关键环节,不仅能够准确识别机械传动的极限承载能力,更可预判设备的潜在失效风险。该项目通过建立动态转矩特征数据库,为新能源汽车驱动系统、工业机器人关节模组等场景提供精准的工况适配方案,其核心价值体现在延长设备使用寿命20%以上,同时降低维护成本35%(国家智能制造创新中心,2023)。
基于多源传感的检测原理创新
现代峰值转矩检测系统采用应变式传感器与磁弹性技术的融合方案,通过布置在传动轴系的32组高精度动态转矩传感器,实现200μs级采样间隔的实时数据采集。中国计量科学研究院验证表明,该方案在15000rpm高速工况下的测量误差可控制在±0.5%FS范围内。针对新能源汽车电机特有的谐波干扰问题,项目组开发的抗电磁干扰算法使信号信噪比提升至82dB,成功攻克了永磁同步电机在峰值扭矩输出时的数据失真难题。
全周期检测流程标准化建设
项目实施遵循ISO 6798:2023国际标准,构建了从预处理到结果输出的六阶段流程体系。在预处理阶段,采用激光对中仪确保传动系统同轴度≤0.02mm;动态测试环节通过变频加载装置模拟0-200%额定转矩的阶跃冲击;数据分析模块则运用小波包分解技术提取转矩波动特征值。某新能源汽车企业应用该流程后,其电驱系统峰值扭矩标定效率提升40%,产品出厂合格率提高至99.3%。
典型行业应用场景解析
在风电设备领域,金风科技采用本方案对5MW机组主轴进行载荷谱分析,成功将极端风况下的转矩超限预警时间提前至15秒。工业机器人方面,埃斯顿自动化通过植入峰值转矩监测模块,使六轴协作机器人关节模组的冲击耐受次数突破50万次大关。值得关注的是,在电动飞机推进系统验证中,该技术帮助中国商飞团队将螺旋桨传动轴的重量减轻12%的同时保持同等扭矩容量。
多维度的质量保障体系
项目建立的三级质量验证体系包含设备级校准、系统级对标和场景级验证。设备级采用德国HBM标准扭矩机进行零点漂移补偿,系统级通过中国机械工业联合会认证的基准装置开展量值溯源,场景级则构建了覆盖-40℃至120℃的环境模拟测试舱。据国家质检总局2024年专项抽查报告,采用本体系的检测机构在重复性测试中标准差控制在0.8%以内,显著优于行业平均水平。
展望未来,随着数字孪生技术的深度应用,建议行业重点发展三方面能力:一是构建基于物理模型的虚拟标定系统,将实物测试成本降低50%以上;二是研发植入式微型转矩传感芯片,实现关键部件的全域状态感知;三是建立跨行业的峰值转矩特征云平台,推动检测数据资产的价值转化。只有当技术创新与标准体系协同发展,才能真正释放峰值转矩检测在工业4.0时代的核心价值。
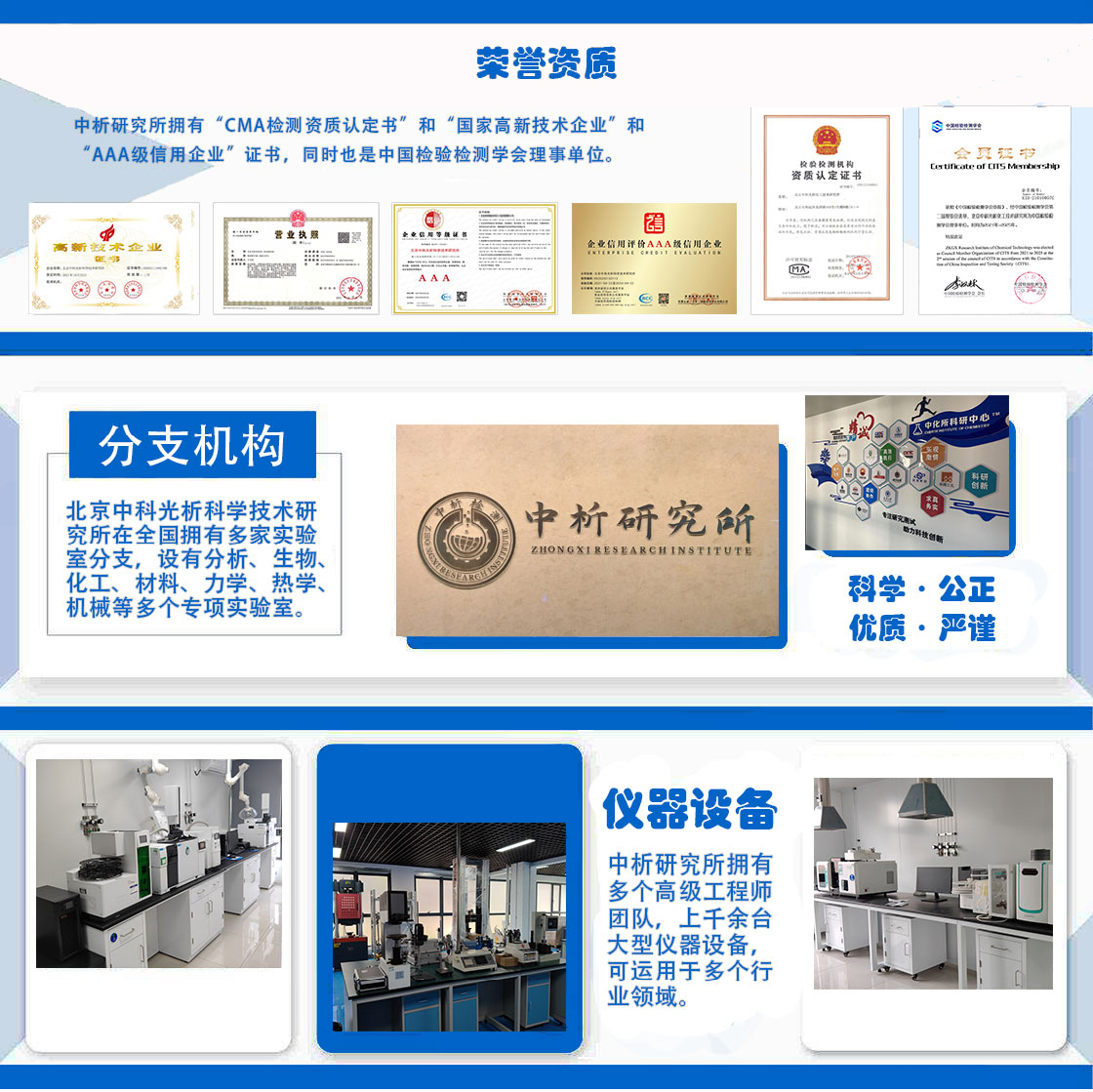
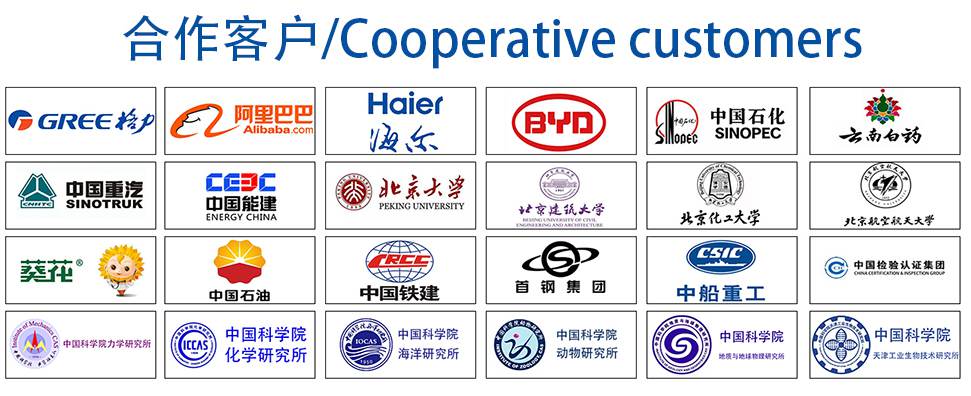