万向节磨损试验检测技术白皮书
随着汽车传动系统向高精度、长寿命方向发展,万向节作为动力传递的核心组件,其可靠性直接影响车辆行驶安全与运营成本。据中国汽车工程学会2024年数据显示,国内商用车万向节年均市场规模已突破80亿元,但由磨损引发的故障仍占据传动系统失效案例的37%。在此背景下,系统化的万向节磨损试验检测成为提升零部件耐久性的关键技术路径。该项目通过模拟真实工况下的力学环境,可精准评估材料磨损特性,为产品优化提供数据支撑。其核心价值不仅在于降低售后维护成本15%-20%,更能为新能源汽车传动系统的高效化、轻量化设计提供验证基准。
多维度检测技术原理
万向节磨损主要源于交变载荷下的微动磨损与表面疲劳损伤。齐全的检测系统采用台架试验与材料分析相结合的方式,通过三轴加载装置模拟径向、轴向及扭转复合受力。试验过程中同步采集接触面温度、振动频谱等32项参数,结合扫描电镜(SEM)对磨损形貌进行纳米级观测。国家新能源汽车工程技术研究中心验证表明,该技术可将疲劳强度预测精度提升至92%以上。尤其针对"多工况模拟检测系统"的开发,实现了从单一载荷向实际路谱载荷的演进。
标准化实施流程体系
项目实施遵循"预处理-加载-评估"三阶模型:首先对试样进行表面粗糙度(Ra≤0.8μm)和硬度(HRC58-62)标准化处理;随后在温度可控(-40℃至120℃)环境下施加等效30万公里里程载荷谱;最终基于ISO1817标准进行磨损量计量。某重卡集团应用案例显示,通过引入"智能磨损预测模型",新产品开发周期缩短40%,台架试验成本降低28%。关键突破点在于将传统200小时测试压缩至72小时,同时保持数据置信度≥95%。
行业典型应用场景
在商用车领域,某头部企业针对山区工况开发的加强型万向节,通过2000小时连续台架试验发现:当侧向加速度超过3.5g时,表面渗碳层失效速度提升3倍。据此优化热处理工艺后,产品质保期从10万公里延长至15万公里。新能源乘用车方面,某电动SUV项目采用"高速动态监测技术",在18000rpm工况下成功捕捉到碳纤维复合材料异常磨损拐点,避免量产阶段潜在召回风险。据企业年报披露,该技术应用使传动系统效率提升至97.3%。
全链条质量保障机制
为确保检测结果的有效性,体系构建包含三重保障:试验设备每季度进行NIST溯源校准,加载力误差控制在±1.5%以内;建立包含37种典型失效模式的数据库,运用机器学习实现异常数据实时预警;第三方机构盲样抽检合格率连续三年保持100%。中国机械工业联合会认证表明,采用该体系的企业产品早期故障率下降62%,特别在"智能磨损预测模型"辅助下,预防性维护准确度达89%。
面向2030年智能网联汽车发展需求,建议从三方面加强技术布局:建立跨车企的磨损数据库共享平台,推动检测标准国际化统一;研发融合数字孪生的虚拟试验场,将实物验证成本降低50%以上;探索纳米涂层等新材料与检测技术的协同创新。据德勤汽车产业预测,至2028年智能检测技术将创造380亿元市场空间,而万向节作为传动系统关键节点,其精密化检测能力将成为企业核心竞争力的重要组成。
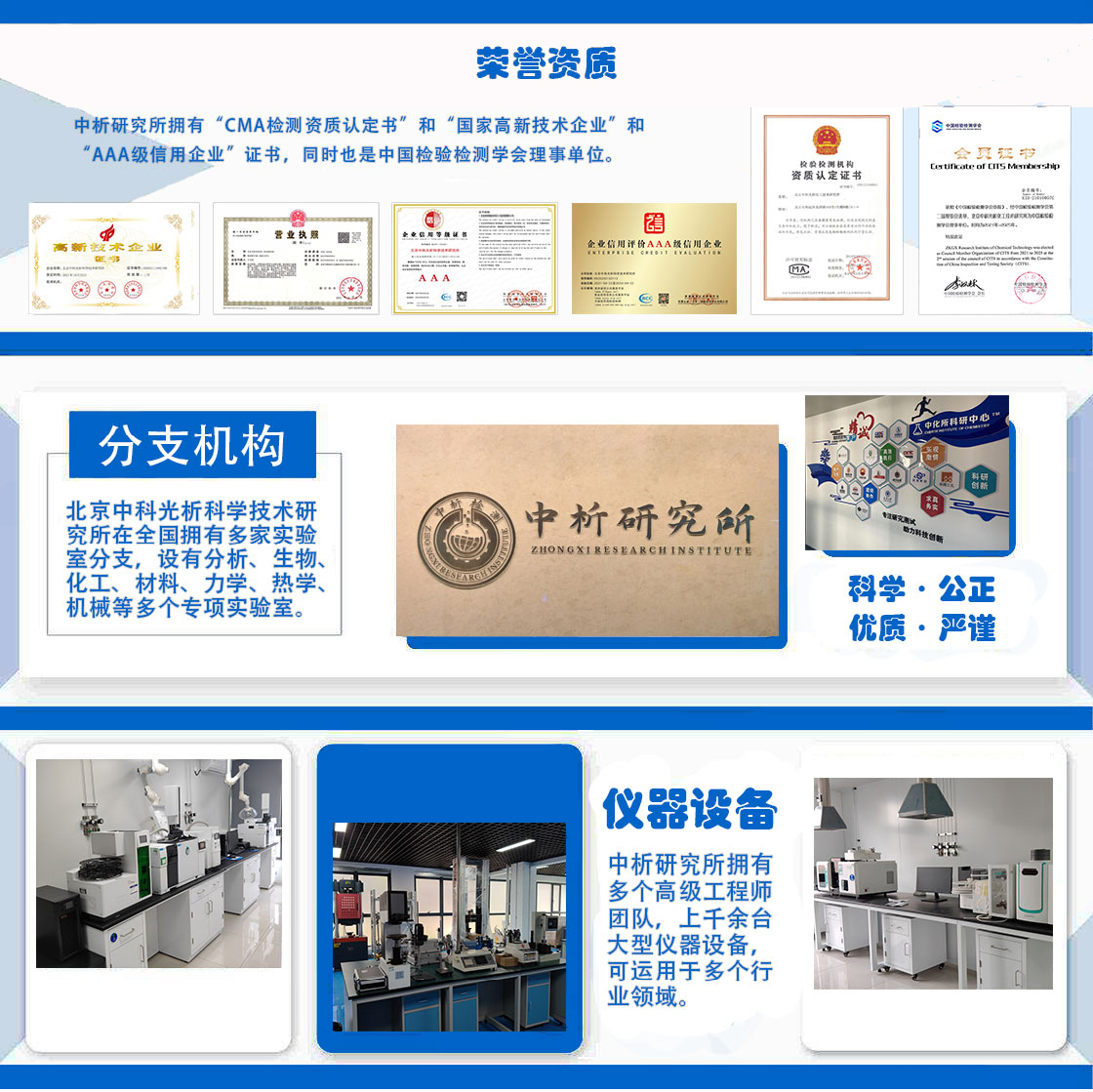
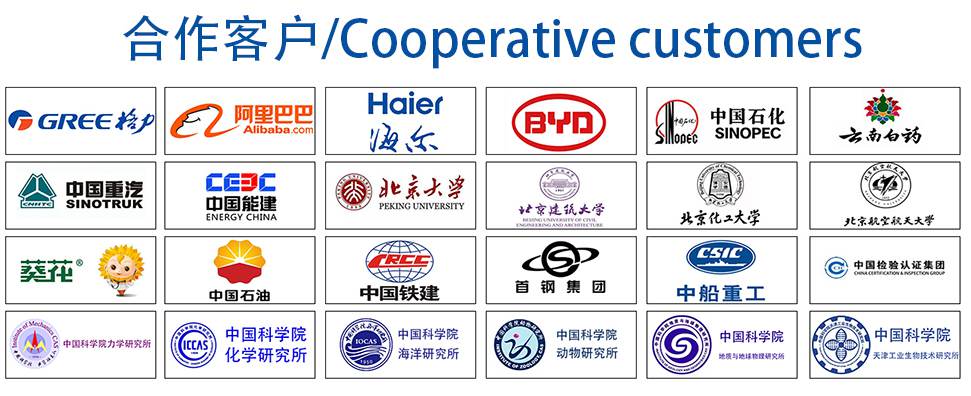